What are PCBs?
PCB stands for Printed Circuit Board. It is a thin board made of fiberglass or other composite material, with conductive pathways etched or printed onto the surface. These pathways, known as traces, connect electronic components such as resistors, capacitors, and integrated circuits (ICs) to form a complete electrical circuit.
PCBs are used in nearly all electronic devices, from simple gadgets like calculators and digital clocks to complex systems such as computers, smartphones, and industrial equipment. They provide a reliable and compact way to assemble electronic circuits, making them essential in modern electronics manufacturing.
Types of PCBs
There are several types of PCBs, each designed for specific applications and manufacturing processes:
-
Single-sided PCBs: These have conductive traces on only one side of the board. They are the simplest and most cost-effective type of PCB, suitable for basic electronic projects.
-
Double-sided PCBs: These have conductive traces on both sides of the board, allowing for more complex circuits and higher component density. The two sides are connected using through-hole vias.
-
Multi-layer PCBs: These consist of three or more layers of conductive traces, separated by insulating layers. They offer the highest component density and are used in complex electronic devices such as smartphones and computers.
-
Flexible PCBs: These are made from flexible materials, allowing them to bend and conform to various shapes. They are used in applications where space is limited or where the PCB needs to flex during use, such as in wearable electronics.
-
Rigid-Flex PCBs: These combine the benefits of rigid and flexible PCBs, with rigid sections for mounting components and flexible sections for connecting them. They are used in applications that require both high component density and flexibility, such as in aerospace and medical devices.
PCB Design Process
The PCB design process involves several steps, from concept to manufacturing:
1. Schematic Design
The first step in PCB design is creating a schematic diagram, which represents the electrical connections between components using standardized symbols. The schematic is developed using Electronic Design Automation (EDA) software, such as KiCad, Eagle, or Altium Designer.
2. Component Selection
Once the schematic is complete, the next step is to select the appropriate components for the circuit. This involves choosing components with the right specifications, such as voltage rating, power dissipation, and package size, to ensure proper functionality and compatibility with the PCB layout.
3. PCB Layout
With the schematic and components finalized, the PCB layout can be created using EDA software. The layout involves arranging the components on the board and routing the traces between them, while adhering to design rules and constraints such as minimum trace width, spacing, and via size.
The PCB layout process typically involves the following sub-steps:
a. Component Placement: Components are placed on the board in a logical and efficient manner, considering factors such as signal integrity, thermal management, and mechanical constraints.
b. Trace Routing: Conductive traces are routed between components, following the schematic connections. The routing process can be manual or automated, depending on the complexity of the circuit and the designer’s preference.
c. Design Rule Check (DRC): The layout is checked against a set of design rules to ensure that it meets manufacturing constraints and industry standards. This helps to identify and resolve issues such as short circuits, insufficient clearances, and improper trace widths.
4. Gerber File Generation
Once the PCB layout is complete and has passed the DRC, Gerber files are generated. Gerber files are the industry-standard format for PCB manufacturing, containing information about the copper layers, solder mask, silkscreen, and drill holes.
5. PCB Fabrication
The Gerber files are sent to a PCB fabrication house, where the physical PCB is manufactured. The fabrication process involves several steps, such as:
a. Copper Deposition: A thin layer of copper is deposited onto the base material, typically using electroplating or lamination.
b. Photoresist Application: A light-sensitive material called photoresist is applied to the copper layer.
c. Exposure and Development: The photoresist is exposed to light through a photomask, which contains the PCB layout pattern. The exposed areas of the photoresist are then removed using a developer solution.
d. Etching: The exposed copper is etched away using a chemical solution, leaving behind the desired conductive traces.
e. Solder Mask Application: A protective layer called solder mask is applied to the PCB, covering the traces and leaving only the exposed pads for component soldering.
f. Silkscreen Printing: Text, logos, and component outlines are printed onto the PCB using a silkscreen process, making it easier to identify components and their orientations.
g. Surface Finish: A surface finish, such as HASL (Hot Air Solder Leveling), ENIG (Electroless Nickel Immersion Gold), or OSP (Organic Solderability Preservative), is applied to the exposed pads to protect them from oxidation and improve solderability.
6. PCB Assembly
After fabrication, the PCB is populated with components using either through-hole or surface-mount technology (SMT). Through-hole components have leads that are inserted into holes drilled in the PCB and soldered on the opposite side, while SMT components are placed and soldered directly onto the surface of the PCB.
PCB assembly can be done manually for low-volume or prototype production, or using automated pick-and-place machines for high-volume manufacturing.
PCB Materials
PCBs are made from a combination of materials, each serving a specific purpose:
1. Substrate
The substrate is the base material of the PCB, providing mechanical support and electrical insulation. The most common substrate materials are:
a. FR-4: A composite material made of fiberglass and epoxy resin, FR-4 is the most widely used substrate for PCBs due to its excellent mechanical and electrical properties, as well as its cost-effectiveness.
b. Rogers: Rogers materials, such as RO4003 and RO4350B, are high-performance substrates designed for high-frequency applications, such as RF and microwave circuits. They offer lower dielectric loss and better controlled dielectric constant compared to FR-4.
c. Polyimide: Polyimide is a flexible substrate material used in flexible and rigid-flex PCBs. It offers excellent thermal stability and mechanical strength, making it suitable for applications that require bending or high-temperature operation.
2. Copper
Copper is used for the conductive traces and pads on the PCB. The thickness of the copper layer is measured in ounces per square foot (oz/ft²), with common thicknesses being 0.5 oz/ft², 1 oz/ft², and 2 oz/ft². Thicker copper layers are used for high-current applications or to improve thermal dissipation.
3. Solder Mask
Solder mask is a protective layer applied to the PCB to cover the copper traces and prevent accidental short circuits during soldering. It also helps to protect the traces from oxidation and mechanical damage. Solder mask is typically green in color, but other colors, such as red, blue, and black, are also available.
4. Silkscreen
Silkscreen is a layer of ink printed onto the PCB to provide text, logos, and component outlines. It helps to identify components and their orientations, making it easier to assemble and debug the PCB. Silkscreen is typically white in color, but other colors, such as black and yellow, are also available.
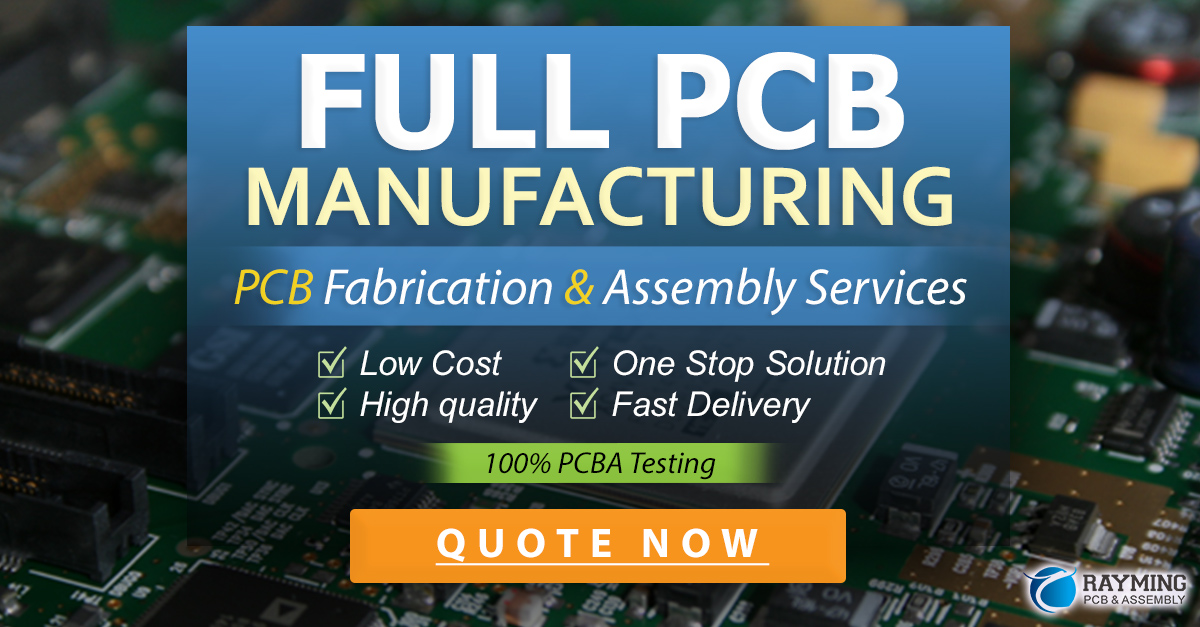
PCB Design Considerations
When designing a PCB, several factors must be considered to ensure proper functionality, reliability, and manufacturability:
1. Signal Integrity
Signal integrity refers to the quality of the electrical signals transmitted through the PCB. It is affected by factors such as trace impedance, crosstalk, and reflections. To maintain signal integrity, designers must consider:
a. Trace Width and Spacing: Trace width and spacing should be designed to match the impedance of the source and load, minimizing reflections and ensuring proper signal transmission.
b. Termination: Proper termination techniques, such as series and parallel termination, should be used to minimize reflections and improve signal quality.
c. Shielding: Sensitive signals should be shielded from external noise sources using techniques such as ground planes, shielded traces, and differential signaling.
2. Power Integrity
Power integrity refers to the quality of the power supply distribution on the PCB. It is affected by factors such as voltage drop, power plane impedance, and decoupling. To maintain power integrity, designers must consider:
a. Power Plane Design: Power planes should be designed to minimize impedance and provide a low-inductance path for current flow. This can be achieved by using thick copper layers and minimizing the distance between the power plane and the ground plane.
b. Decoupling: Decoupling capacitors should be placed close to the power pins of ICs to minimize the effects of power supply noise and transients.
c. Voltage Regulation: Proper voltage regulation techniques, such as using voltage regulators and ferrite beads, should be used to ensure stable and clean power supply to the components.
3. Thermal Management
Thermal management refers to the ability of the PCB to dissipate heat generated by the components. Poor thermal management can lead to component overheating, reduced reliability, and even failure. To ensure proper thermal management, designers must consider:
a. Component Placement: Components should be placed in a way that minimizes thermal interaction and allows for efficient heat dissipation. High-power components should be placed away from temperature-sensitive components, and sufficient space should be provided for airflow.
b. Copper Pours: Copper pours, also known as ground planes or power planes, can be used to improve heat dissipation by providing a large surface area for heat conduction.
c. Thermal Vias: Thermal vias, which are small holes filled with conductive material, can be used to transfer heat from the component side of the PCB to the opposite side, where it can be dissipated by heatsinks or other cooling methods.
4. Manufacturability
Manufacturability refers to the ease and reliability of manufacturing the PCB. To ensure good manufacturability, designers must consider:
a. Design Rules: PCB design rules, such as minimum trace width, spacing, and via size, should be followed to ensure that the PCB can be manufactured reliably and cost-effectively.
b. Component Selection: Components should be selected based on their availability, cost, and compatibility with the manufacturing process. Surface-mount components are generally preferred over through-hole components for their smaller size and better automation compatibility.
c. Panelization: PCBs should be designed to fit efficiently into standard panel sizes to minimize material waste and reduce manufacturing costs. Panelization also involves adding features such as fiducial markers and tooling holes to facilitate automated assembly.
PCB Testing and Inspection
After manufacturing and assembly, PCBs must be tested and inspected to ensure proper functionality and quality. Common testing and inspection methods include:
1. Visual Inspection
Visual inspection is the first step in PCB testing, involving a manual or automated check of the PCB for visible defects such as incorrect component placement, solder bridges, and damaged traces.
2. Automated Optical Inspection (AOI)
AOI uses cameras and image processing software to automatically detect surface-level defects on the PCB, such as missing components, incorrect component polarity, and solder defects.
3. X-Ray Inspection
X-ray inspection is used to detect internal defects in the PCB, such as voids in solder joints, broken traces, and delamination. It is particularly useful for inspecting high-density PCBs and ball grid array (BGA) packages.
4. In-Circuit Testing (ICT)
ICT involves using a bed-of-nails fixture to make electrical contact with the PCB and test the functionality of individual components and circuits. It can detect faults such as open and short circuits, incorrect component values, and missing components.
5. Functional Testing
Functional testing involves powering up the PCB and testing its overall functionality, including input/output, communication, and system-level performance. It is typically done using specialized test equipment and software, such as LabVIEW or custom-designed test fixtures.
Frequently Asked Questions (FAQ)
1. What is the difference between through-hole and surface-mount components?
Through-hole components have leads that are inserted into holes drilled in the PCB and soldered on the opposite side, while surface-mount components are placed and soldered directly onto the surface of the PCB. Surface-mount components are generally smaller and better suited for automated assembly, while through-hole components are easier to hand-solder and replace.
2. What is the purpose of a ground plane in a PCB?
A ground plane is a large area of copper on a PCB layer that is connected to the ground potential. It serves several purposes, including:
a. Providing a low-impedance return path for electrical currents
b. Reducing electromagnetic interference (EMI) by shielding sensitive signals
c. Improving heat dissipation by providing a large surface area for thermal conduction
3. What is the difference between a solder mask and a silkscreen?
A solder mask is a protective layer applied to the PCB to cover the copper traces and prevent accidental short circuits during soldering. It also helps to protect the traces from oxidation and mechanical damage. Silkscreen, on the other hand, is a layer of ink printed onto the PCB to provide text, logos, and component outlines, making it easier to identify components and their orientations.
4. What is the purpose of a decoupling capacitor in a PCB?
Decoupling capacitors are used to reduce power supply noise and transients in a PCB. They are placed close to the power pins of ICs, providing a local reservoir of charge that can quickly supply current when needed and absorb high-frequency noise. This helps to ensure stable and clean power supply to the components, improving signal integrity and overall system performance.
5. What is the difference between a rigid PCB and a flexible PCB?
A rigid PCB is made from a solid substrate material, such as FR-4, and is designed to maintain its shape and structure. Rigid PCBs are the most common type and are used in a wide range of electronic devices. Flexible PCBs, on the other hand, are made from flexible substrate materials, such as polyimide, and can bend and conform to various shapes. They are used in applications where space is limited or where the PCB needs to flex during use, such as in wearable electronics and automotive systems. Rigid-flex PCBs combine the benefits of both types, with rigid sections for mounting components and flexible sections for connecting them.
In conclusion, PCBs are essential components in modern electronics, providing a reliable and efficient way to assemble complex circuits. Understanding the fundamentals of PCB design, materials, manufacturing, and testing is crucial for anyone involved in electronics design and development. By considering factors such as signal integrity, power integrity, thermal management, and manufacturability, designers can create high-quality PCBs that meet the requirements of their applications and ensure reliable performance over the long term.
Leave a Reply