What is a PCB Etcher?
A PCB etcher, also known as a PCB Etching machine, is a device used to remove unwanted copper from a printed circuit board, leaving behind the desired conductive traces that form the electrical connections of the circuit. The etching process involves exposing the copper-clad board to a corrosive solution, which eats away the unprotected copper, while the areas covered by etch-resistant material remain intact.
Types of PCB Etchers
There are several types of PCB etchers available, each with its own advantages and disadvantages:
-
Chemical Etchers: These etchers use a chemical solution, typically ferric chloride or ammonium persulfate, to remove the unwanted copper. Chemical etchers are the most common type used by hobbyists and small-scale PCB Manufacturers.
-
Spray Etchers: Spray etchers use a pressurized spray of etchant solution to remove the copper. This method is faster than chemical etching but requires more specialized equipment.
-
Bubble Etchers: Bubble etchers use a bubbler to agitate the etchant solution, which helps to speed up the etching process and ensures even etching across the PCB.
-
Laser Etchers: Laser etchers use a high-powered laser to remove the copper from the PCB. While this method is highly precise and efficient, it is also the most expensive and requires specialized equipment.
How Does a PCB Etcher Work?
A PCB etcher works by exposing the copper-clad board to a corrosive solution that dissolves the unwanted copper. The process typically involves the following steps:
-
PCB Design: The first step is to design the PCB using specialized software or by hand-drawing the circuit layout.
-
Transfer Design to PCB: The design is then transferred onto the copper-clad board using various methods, such as photoresist, toner transfer, or direct printing.
-
Etching: The prepared PCB is immersed in the etchant solution, which removes the unprotected copper, leaving behind the desired conductive traces.
-
Cleaning: After etching, the board is cleaned to remove any remaining etchant and protective material.
How to Make a PCB Etcher
Now that you understand what a PCB etcher is and how it works, let’s dive into the process of making your own chemical PCB etcher.
Materials Needed
- Plastic container (large enough to accommodate your PCB)
- Aquarium air pump
- Air stone
- Tubing
- Ferric chloride or ammonium persulfate etchant solution
- Protective gloves and eyewear
- Copper-clad board
- Etch-resistant marker or transfer paper
Step-by-Step Instructions
-
Prepare the Container: Drill two holes in the lid of the plastic container, one for the air tubing and one for ventilation. Place the air stone inside the container and connect it to the air pump using the tubing.
-
Add Etchant Solution: Pour the etchant solution into the container, following the manufacturer’s instructions for the appropriate amount based on the size of your PCB.
-
Prepare the PCB: Design your PCB and transfer the design onto the copper-clad board using your preferred method (e.g., etch-resistant marker or transfer paper).
-
Etching: Place the prepared PCB into the container with the etchant solution. Turn on the air pump to begin bubbling the solution, which will agitate it and speed up the etching process. Monitor the progress closely and remove the PCB once all the unwanted copper has been etched away.
-
Clean the PCB: Rinse the etched PCB thoroughly with water to remove any remaining etchant solution. Use a solvent to remove the etch-resistant material, revealing the final circuit layout.
Safety Considerations
When working with etchant solutions and PCB etching machines, it’s essential to prioritize safety:
- Always wear protective gloves and eyewear when handling etchant solutions
- Work in a well-ventilated area to avoid inhaling fumes
- Properly dispose of used etchant solution according to local regulations
- Store etchant solutions and PCB etching equipment out of reach of children and pets
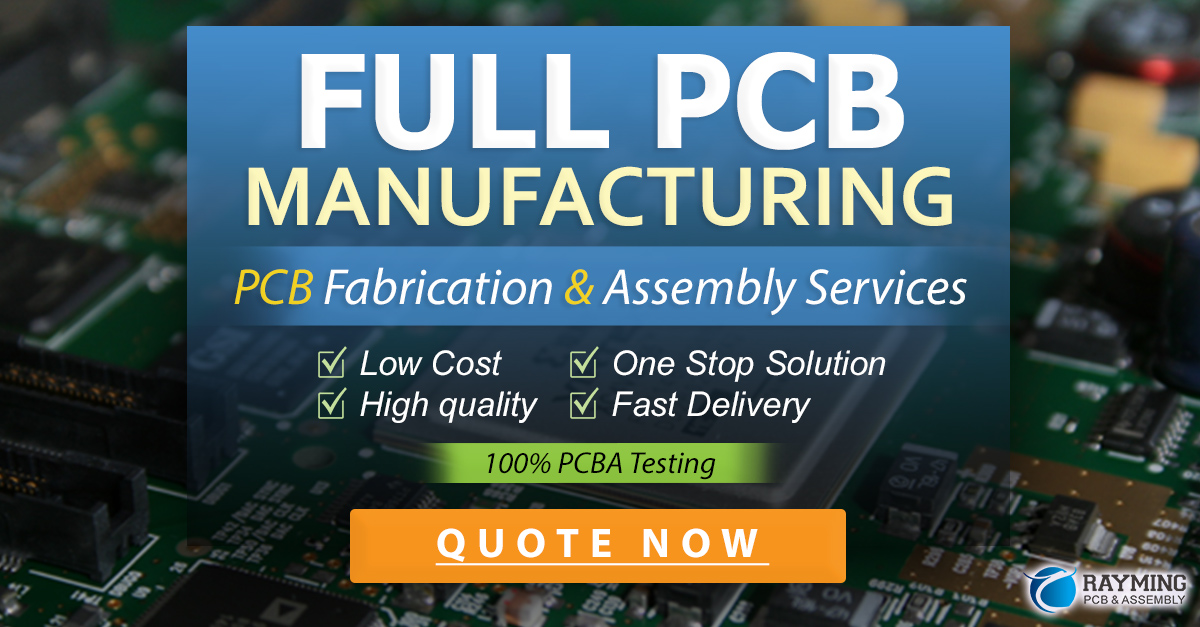
Advantages of Using a PCB Etcher
Using a PCB etcher to create your own printed circuit boards offers several advantages:
-
Cost-effective: Making your own PCBs can be significantly cheaper than ordering them from a manufacturer, especially for small-scale projects or prototypes.
-
Customization: With a PCB etcher, you have complete control over the design and layout of your PCBs, allowing for greater customization and flexibility.
-
Rapid prototyping: PCB etchers enable you to quickly create and test prototypes, reducing the time between design iterations.
-
Educational: Building and using a PCB etcher can be a valuable learning experience for those interested in electronics and circuit design.
Troubleshooting Common Issues
When using a PCB etcher, you may encounter some common issues. Here are a few tips for troubleshooting:
-
Uneven etching: Ensure that the etchant solution is properly agitated and that the PCB is completely submerged. Adjust the position of the air stone if necessary.
-
Over-etching: Monitor the etching process closely and remove the PCB as soon as all the unwanted copper has been removed. Over-etching can lead to damaged or disconnected traces.
-
Incomplete etching: If the etchant solution is too weak or the etching time is insufficient, some unwanted copper may remain on the PCB. Increase the etching time or replace the etchant solution if necessary.
-
Poor design transfer: Make sure that the design is properly transferred onto the copper-clad board before etching. Check for any gaps or inconsistencies in the etch-resistant material.
Frequently Asked Questions (FAQ)
-
What is the best etchant solution for PCB etching?
The two most common etchant solutions for PCB etching are ferric chloride and ammonium persulfate. Ferric chloride is more readily available and easier to use, while ammonium persulfate is faster and produces less waste. -
Can I reuse the etchant solution?
Etchant solutions can be reused multiple times, but they will become less effective over time as the copper content increases. Monitor the etching speed and replace the solution when it becomes too slow or ineffective. -
How long does the etching process take?
The etching time depends on various factors, such as the strength of the etchant solution, the amount of copper to be removed, and the level of agitation. On average, the process can take anywhere from 10 minutes to an hour. -
What should I do with the used etchant solution?
Used etchant solution should be disposed of properly according to local regulations. Some communities have hazardous waste disposal facilities that accept used etchant solutions. Never pour the solution down the drain or into the environment. -
Can I use a PCB etcher for other materials besides copper-clad boards?
PCB etchers are specifically designed for etching copper from printed circuit boards. While some etchant solutions may work on other metals, it is not recommended to use a PCB etcher for materials other than copper-clad boards.
Conclusion
A PCB etcher is an invaluable tool for anyone looking to create their own printed circuit boards. By following the steps outlined in this guide, you can build your own chemical PCB etcher and start producing Custom PCBs for your projects. Remember to prioritize safety, monitor the etching process closely, and troubleshoot any issues that may arise. With practice and patience, you’ll be creating professional-quality PCBs in no time.
Etcher Type | Advantages | Disadvantages |
---|---|---|
Chemical | – Readily available materials – Simple setup – Cost-effective |
– Slower etching process – Requires disposal of hazardous waste |
Spray | – Faster etching process – Even etching across the PCB |
– Requires specialized equipment – Higher setup costs |
Bubble | – Faster etching process – Even etching across the PCB |
– Requires additional equipment (air pump and air stone) |
Laser | – High precision – Efficient etching process |
– Expensive equipment – Requires specialized knowledge |
Leave a Reply