What is PCB customization?
PCB customization refers to the process of designing and manufacturing circuit boards tailored to specific needs and requirements. Unlike standard PCBs, which are mass-produced and have predetermined layouts and features, Custom PCBs are designed from scratch to fit the unique specifications of a particular project or application.
Benefits of PCB Customization
- Optimal Performance: Custom PCBs are designed to meet the exact requirements of a specific application, ensuring optimal performance and functionality.
- Cost-Effective: While the initial cost of custom PCBs may be higher than off-the-shelf solutions, they can be more cost-effective in the long run, especially for large-scale production runs.
- Compact and Efficient: Custom PCBs can be designed to minimize the overall size and maximize the efficiency of the electronic system, making them ideal for space-constrained applications.
The PCB Customization Process
The process of customizing a PCB involves several key steps, each of which plays a crucial role in the final product’s quality and functionality.
Step 1: Design and Schematic Creation
The first step in PCB customization is to create a schematic diagram that represents the electronic circuit’s components and their interconnections. This schematic serves as a blueprint for the PCB layout and is created using electronic design automation (EDA) software.
Step 2: PCB Layout Design
Once the schematic is complete, the next step is to design the physical layout of the PCB. This involves placing components and routing the connections between them while considering factors such as signal integrity, power distribution, and manufacturability. The layout design is also created using EDA software and follows a set of design rules to ensure the PCB’s functionality and reliability.
Step 3: Prototyping and Testing
After the PCB layout is finalized, a prototype is manufactured to test its functionality and performance. This prototype is subjected to various tests to identify any issues or areas for improvement. If necessary, the design is modified based on the test results, and a new prototype is created.
Step 4: Manufacturing
Once the prototype has been thoroughly tested and meets all the requirements, the custom PCB is ready for mass production. The manufacturing process involves several steps, including:
- PCB Fabrication: The PCB design files are sent to a PCB manufacturer, who creates the physical board using a combination of etching, drilling, and plating processes.
- Component Placement: The components are placed on the PCB using automated pick-and-place machines or manual assembly, depending on the complexity and quantity of the boards.
- Soldering: The components are soldered onto the PCB using various techniques, such as wave soldering, reflow soldering, or hand soldering.
- Quality Control: The manufactured PCBs undergo a series of quality control checks to ensure they meet the required specifications and are free from defects.
PCB Customization Options
When customizing a PCB, there are several options to consider, depending on the specific requirements of the application.
Number of Layers
PCBs can be designed with varying numbers of layers, ranging from single-layer to multi-layer boards. The number of layers affects the PCB’s complexity, cost, and ability to accommodate high-density designs.
Layers | Complexity | Cost | Density |
---|---|---|---|
Single | Low | Low | Low |
Double | Medium | Medium | Medium |
Multi | High | High | High |
Material Selection
The choice of PCB material depends on factors such as the operating environment, temperature range, and required electrical properties. Common PCB materials include:
- FR-4: A glass-reinforced epoxy laminate, widely used for general-purpose applications.
- High-Frequency Materials: Specialized materials designed for high-frequency applications, such as RF and microwave circuits.
- Flexible PCBs: Made from flexible materials like polyimide, these PCBs can be bent and folded to fit into tight spaces or conform to specific shapes.
Surface Finish
The surface finish of a PCB plays a crucial role in its solderability, corrosion resistance, and overall reliability. Some common surface finishes include:
- HASL (Hot Air Solder Leveling): A tin-lead alloy is applied to the PCB surface, providing good solderability and low cost.
- ENIG (Electroless Nickel Immersion Gold): A layer of nickel is deposited on the PCB, followed by a thin layer of gold, offering excellent corrosion resistance and solderability.
- OSP (Organic Solderability Preservative): A thin, organic coating is applied to the PCB to prevent oxidation and maintain solderability.
Trace Width and Spacing
The width and spacing of the traces on a PCB affect its current-carrying capacity, signal integrity, and manufacturability. Narrower traces and smaller spaces between them allow for higher-density designs but can also increase the manufacturing cost and complexity.
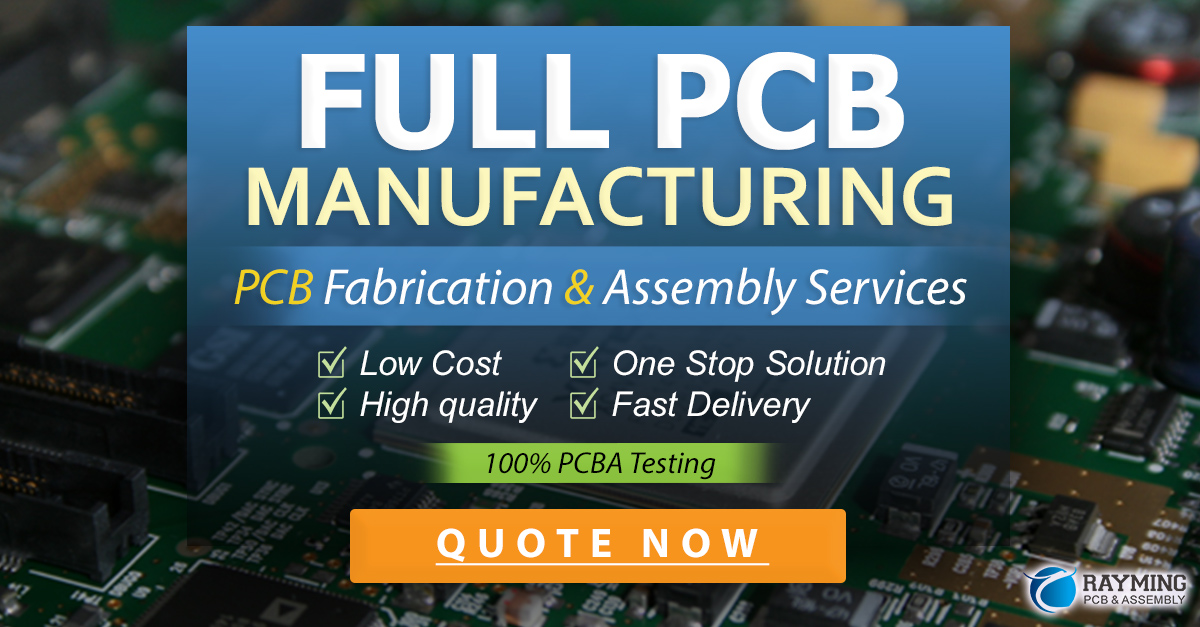
PCB Customization Services
For those who lack the expertise or resources to design and manufacture custom PCBs in-house, there are several PCB customization services available.
Turnkey PCB Services
Turnkey PCB services offer a complete solution, from design to manufacturing. Customers provide the specifications and requirements, and the service provider handles the entire process, delivering the finished PCBs.
PCB Design Services
For those who have the manufacturing capabilities but lack the design expertise, PCB design services can help create the schematic and layout files based on the provided specifications.
PCB Fabrication Services
PCB fabrication services focus on the manufacturing aspect of PCB customization. Customers provide the design files, and the service provider manufactures the PCBs according to the specifications.
Frequently Asked Questions (FAQ)
-
What are the advantages of using custom PCBs over off-the-shelf solutions?
Custom PCBs offer several advantages, including optimal performance, cost-effectiveness for large-scale production, and the ability to create compact and efficient designs tailored to specific applications. -
How long does the PCB customization process typically take?
The duration of the PCB customization process depends on factors such as the complexity of the design, the number of revisions required, and the manufacturing lead time. On average, the process can take anywhere from a few days to several weeks. -
What is the minimum order quantity (MOQ) for custom PCBs?
The MOQ for custom PCBs varies depending on the manufacturer and the complexity of the design. Some PCB fabrication services offer low MOQs, even for prototype runs, while others may require higher quantities for cost-effectiveness. -
Can I customize a PCB for high-frequency applications?
Yes, PCBs can be customized for high-frequency applications by using specialized materials and design techniques to ensure optimal signal integrity and performance. -
What should I consider when choosing a surface finish for my custom PCB?
When selecting a surface finish for your custom PCB, consider factors such as the operating environment, solderability requirements, cost, and the compatibility with the components being used.
Conclusion
PCB customization offers a powerful solution for creating circuit boards tailored to specific applications and requirements. By understanding the customization process, options, and available services, engineers and designers can harness the full potential of custom PCBs to develop high-performance, cost-effective, and compact electronic systems. As technology continues to advance, the demand for custom PCBs is likely to grow, driving innovation and enabling the development of cutting-edge electronic devices across various industries.
Leave a Reply