Understanding PWM Basics
Before we dive into the design process, let’s first understand the fundamentals of PWM. PWM is a method of encoding analog signal levels into a digital signal by modulating the width of the pulse. The duty cycle, which is the ratio of the pulse width to the period of the signal, determines the average voltage or power delivered to the load.
The basic principle of PWM can be summarized as follows:
– A square wave signal is generated with a fixed frequency but variable pulse width.
– The pulse width is modulated based on the desired analog signal level.
– The average voltage or power delivered to the load is proportional to the duty cycle of the PWM signal.
PWM offers several advantages over analog control methods, such as:
– Efficiency: PWM allows for efficient power delivery to the load, as the switching losses are minimized.
– Precision: By varying the duty cycle, PWM enables precise control over the average voltage or power.
– Simplicity: PWM Circuits can be easily implemented using digital controllers or dedicated PWM ICs.
Determining PWM Requirements
To design a PWM circuit that meets your specific needs, you must first determine the requirements of your application. Consider the following factors:
1. Frequency
The PWM frequency is a crucial parameter that affects the performance of your circuit. It determines how frequently the pulse width is modulated and impacts factors such as switching losses, electromagnetic interference (EMI), and the response time of the load.
Typically, PWM frequencies range from a few hundred hertz to several megahertz, depending on the application. For example:
– Motor control: PWM frequencies of a few kilohertz are commonly used to minimize switching losses and ensure smooth motor operation.
– LED dimming: Higher PWM frequencies, often in the range of a few hundred kilohertz, are preferred to avoid visible flicker.
– Power conversion: The PWM frequency is chosen based on the desired switching frequency of the power converter, considering factors such as efficiency and component size.
2. Duty Cycle Range
The duty cycle range specifies the minimum and maximum pulse widths that your PWM circuit should be capable of generating. It determines the range of control over the average voltage or power delivered to the load.
Consider the following examples:
– Motor control: A duty cycle range of 0% to 100% allows for full control over the motor speed, from zero to maximum.
– LED dimming: A duty cycle range of 0% to 100% enables complete dimming control, from fully off to fully on.
– Power conversion: The duty cycle range is determined by the desired output voltage range and the input voltage of the power converter.
3. Resolution
The resolution of the PWM signal refers to the smallest incremental change in the duty cycle that your circuit can achieve. Higher resolution allows for finer control over the output voltage or power.
The required resolution depends on the specific application and the level of control precision needed. For example:
– Motor control: A resolution of 8 bits (256 steps) is often sufficient for smooth motor speed control.
– LED dimming: Higher resolutions, such as 12 bits (4096 steps) or 16 bits (65536 steps), provide smoother dimming transitions and eliminate visible brightness steps.
– Power conversion: The resolution is determined by the desired output voltage resolution and the accuracy requirements of the power converter.
4. Load Characteristics
The characteristics of the load that the PWM circuit will be driving play a significant role in the design process. Consider the following load parameters:
- Voltage and current ratings: Ensure that the PWM circuit can handle the maximum voltage and current requirements of the load.
- Impedance: The load impedance affects the current drawn by the load and the power dissipation in the PWM circuit.
- Inductive or capacitive nature: Inductive loads, such as motors, require special considerations for flyback protection and voltage spikes, while capacitive loads may require current limiting.
Selecting PWM Generation Method
Once you have determined the PWM requirements for your application, the next step is to select the appropriate method for generating the PWM signal. There are several options available, each with its own advantages and limitations.
1. Microcontroller or Processor
One of the most common methods for generating PWM signals is using a microcontroller or processor with built-in PWM functionality. Many modern microcontrollers, such as Arduino, PIC, or STM32, have dedicated PWM peripherals that can generate PWM signals with configurable frequency, duty cycle, and resolution.
Advantages:
– Flexibility: Microcontrollers allow for easy modification of PWM parameters through software.
– Integration: PWM generation can be seamlessly integrated with other control and monitoring functions within the microcontroller.
– Cost-effective: Microcontrollers are readily available and offer a cost-effective solution for PWM generation.
Limitations:
– Limited number of PWM channels: Microcontrollers typically have a fixed number of PWM channels, which may be insufficient for applications requiring multiple PWM signals.
– Processor overhead: Generating PWM signals using a microcontroller consumes processor resources, which may impact other tasks running on the same microcontroller.
2. Dedicated PWM IC
Another option is to use a dedicated PWM integrated circuit (IC) specifically designed for generating PWM signals. These ICs offer a range of features and capabilities, such as multiple PWM channels, programmable frequency and duty cycle, and high resolution.
Advantages:
– Multiple PWM channels: Dedicated PWM ICs often provide multiple independent PWM channels, allowing for control of multiple loads simultaneously.
– High resolution: PWM ICs can offer higher resolution compared to microcontrollers, enabling finer control over the duty cycle.
– Offloading processor: Using a dedicated PWM IC frees up the microcontroller or processor from the task of PWM generation, allowing it to focus on other control and monitoring functions.
Limitations:
– Additional component: Incorporating a dedicated PWM IC adds an extra component to the circuit, increasing cost and board space.
– Configuration complexity: Configuring a PWM IC may require additional software or register settings, which can be more complex compared to using a microcontroller’s built-in PWM functionality.
3. Analog Circuit
In some cases, an analog circuit can be used to generate PWM signals. This approach involves comparing a reference voltage with a sawtooth or triangle waveform to generate the PWM signal.
Advantages:
– Simplicity: Analog PWM Circuits can be relatively simple to design and implement.
– No processor required: Analog PWM generation does not rely on a microcontroller or processor, making it suitable for standalone applications.
Limitations:
– Limited flexibility: Modifying PWM parameters in an analog circuit may require hardware changes, such as adjusting resistor or capacitor values.
– Susceptibility to noise: Analog PWM circuits are more susceptible to noise and interference compared to digital methods.
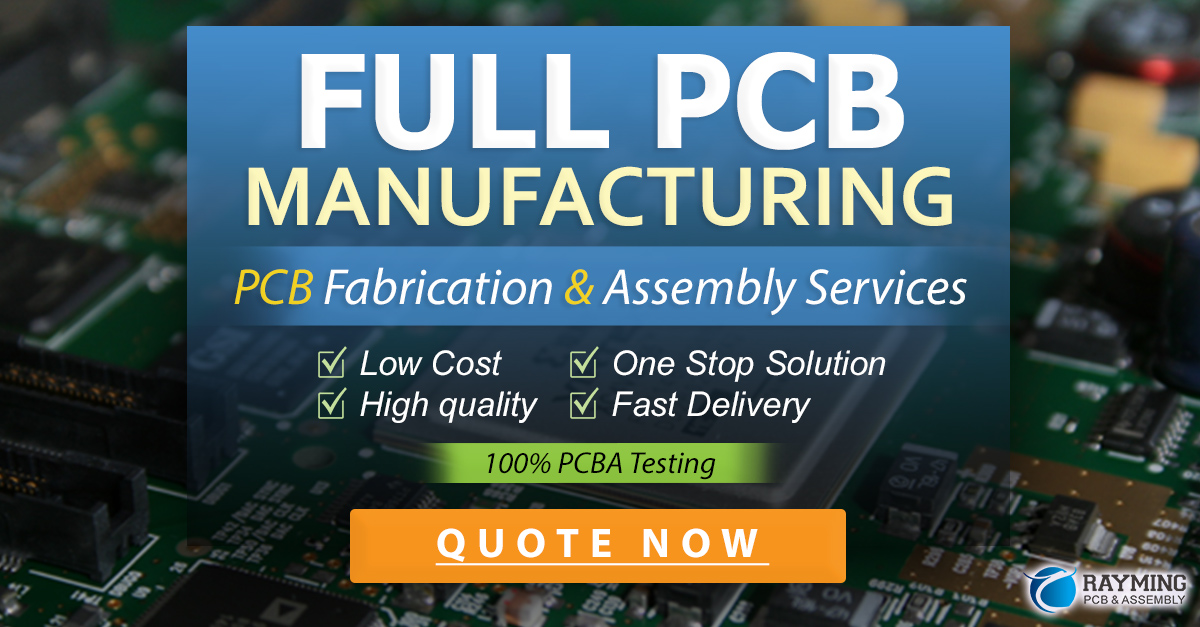
Designing the PWM Circuit
Once you have selected the appropriate PWM generation method, it’s time to design the actual PWM circuit. The design process involves several key considerations:
1. Power Stage
The power stage of the PWM circuit is responsible for driving the load based on the PWM signal. It typically consists of power transistors, such as MOSFETs or IGBTs, that switch on and off according to the PWM signal.
Consider the following factors when designing the power stage:
– Voltage and current ratings: Select power transistors that can handle the maximum voltage and current requirements of the load.
– Switching speed: Choose transistors with suitable switching speeds to minimize switching losses and ensure efficient operation.
– Heat dissipation: Proper heat sinking and thermal management are essential to prevent overheating of the power transistors.
2. Gate Drive Circuit
The gate drive circuit is responsible for providing the necessary drive current to turn the power transistors on and off quickly and efficiently. It interfaces between the PWM signal and the power stage.
Key considerations for the gate drive circuit include:
– Gate drive voltage: Ensure that the gate drive voltage is sufficient to fully turn on the power transistors while considering the maximum allowable gate-source voltage.
– Drive current: Provide adequate drive current to charge and discharge the gate capacitance of the power transistors quickly, minimizing switching losses.
– Isolation: In some cases, galvanic isolation may be required between the PWM signal and the power stage, which can be achieved using optocouplers or isolated gate drivers.
3. Feedback and Control
Depending on your application, you may need to incorporate feedback and control mechanisms into your PWM circuit. Feedback allows for closed-loop control, ensuring that the output voltage or current remains stable and responds to variations in load or input conditions.
Consider the following aspects of feedback and control:
– Sensing: Use appropriate sensors, such as voltage dividers or current shunts, to measure the output voltage or current.
– Feedback loop: Design a stable feedback loop that compares the sensed output with a reference value and adjusts the PWM duty cycle accordingly.
– Compensation: Implement appropriate compensation techniques, such as proportional-integral-derivative (PID) control or lead-lag compensation, to ensure stable and responsive control.
4. Protection Circuitry
To ensure the reliability and longevity of your PWM circuit, it is essential to incorporate protection circuitry. Protection features safeguard the circuit and the load from potential faults or abnormal conditions.
Consider including the following protection mechanisms:
– Over-current protection: Implement current sensing and limiting circuitry to protect the power stage and the load from excessive current.
– Over-voltage protection: Use voltage clamping or crowbar circuits to prevent voltage spikes from damaging the circuit components.
– Thermal shutdown: Include temperature sensing and shutdown mechanisms to protect the power transistors from overheating.
PWM Circuit Example
To illustrate the design process, let’s consider a simple example of a PWM circuit for controlling the brightness of an LED.
Requirements
- Frequency: 1 kHz
- Duty cycle range: 0% to 100%
- Resolution: 8 bits (256 steps)
- Load: Single LED with a forward voltage of 3.3V and a maximum current of 20mA
PWM Generation
For this example, we’ll use an Arduino microcontroller to generate the PWM signal. The Arduino has built-in PWM functionality and provides an easy-to-use platform for prototyping.
Power Stage
Since the load is a single LED with a low current requirement, we can use a simple transistor-based power stage. A small-signal NPN transistor, such as the 2N2222, can be used to switch the LED on and off based on the PWM signal.
Circuit Diagram
Here’s a simplified circuit diagram for the LED PWM control:
Arduino PWM Pin
|
|
|
|/
|-| 2N2222
| >-|
|-| |
| |
| /
| \ 330Ω
| /
| |
| |
| >|--- LED
| |
| |
| /
| \ 220Ω
| /
|
|
GND
Code
The Arduino code for generating the PWM signal and controlling the LED brightness can be as simple as:
const int pwmPin = 9; // PWM output pin
void setup() {
pinMode(pwmPin, OUTPUT);
}
void loop() {
// Gradually increase the brightness from 0 to 255
for (int brightness = 0; brightness <= 255; brightness++) {
analogWrite(pwmPin, brightness);
delay(10);
}
// Gradually decrease the brightness from 255 to 0
for (int brightness = 255; brightness >= 0; brightness--) {
analogWrite(pwmPin, brightness);
delay(10);
}
}
In this code, the analogWrite()
function is used to set the PWM duty cycle on the specified pin. The duty cycle value ranges from 0 (0% duty cycle) to 255 (100% duty cycle), providing an 8-bit resolution.
Frequently Asked Questions (FAQ)
-
What is PWM, and how does it work?
PWM stands for Pulse Width Modulation. It is a technique used to encode analog signal levels into a digital signal by modulating the width of the pulses. The duty cycle of the PWM signal determines the average voltage or power delivered to the load. By varying the duty cycle, PWM allows for precise control over the output voltage or power. -
What are the advantages of using PWM?
PWM offers several advantages, including: - Efficiency: PWM enables efficient power delivery to the load by minimizing switching losses.
- Precision: PWM provides precise control over the average voltage or power by varying the duty cycle.
- Simplicity: PWM circuits can be easily implemented using digital controllers or dedicated PWM ICs.
-
Flexibility: PWM parameters, such as frequency and duty cycle, can be easily modified through software or configuration registers.
-
What factors should I consider when selecting the PWM frequency?
When selecting the PWM frequency, consider the following factors: - Application requirements: Different applications have different frequency requirements. For example, motor control typically uses lower frequencies (a few kilohertz) to minimize switching losses, while LED dimming may require higher frequencies (hundreds of kilohertz) to avoid visible flicker.
- Switching losses: Higher PWM frequencies result in increased switching losses in the power stage. Consider the trade-off between frequency and efficiency.
- Electromagnetic interference (EMI): High PWM frequencies can generate EMI, which may require additional filtering or shielding measures.
-
Response time: The PWM frequency affects the response time of the load. Higher frequencies allow for faster response times.
-
How do I select the appropriate power transistors for the PWM power stage?
When selecting power transistors for the PWM power stage, consider the following factors: - Voltage rating: Choose transistors with a voltage rating higher than the maximum voltage the circuit will be exposed to.
- Current rating: Select transistors that can handle the maximum current required by the load.
- Switching speed: Faster Switching Transistors minimize switching losses and improve efficiency.
-
Package and thermal considerations: Consider the package type and thermal requirements of the transistors based on the power dissipation and operating conditions.
-
What protection features should I include in my PWM circuit?
To ensure the reliability and safety of your PWM circuit, consider including the following protection features: - Over-current protection: Implement current sensing and limiting circuitry to protect the power stage and the load from excessive current.
- Over-voltage protection: Use voltage clamping or crowbar circuits to prevent voltage spikes from damaging the circuit components.
- Thermal shutdown: Include temperature sensing and shutdown mechanisms to protect the power transistors from overheating.
- Fault detection and indication: Incorporate fault detection circuitry and provide visual or audible indications of fault conditions.
Conclusion
Designing a PWM circuit tailored to your specific needs involves understanding the PWM basics, determining the requirements of your application, selecting the appropriate PWM generation method, and considering key design aspects such as the power stage, gate drive circuit, feedback and control, and protection circuitry.
By following the guidelines and considerations outlined in this article, you can design a robust and efficient PWM circuit that meets your desired specifications. Remember to carefully evaluate your requirements, select suitable components, and test and validate your design to ensure optimal performance and reliability.
PWM is a versatile technique with a wide range of applications, from motor control and LED dimming to power conversion and beyond. By mastering the art of PWM circuit design, you can unlock the potential of precise power control and create innovative solutions for your projects.
Leave a Reply