Understanding the Basics of Shielding
Before diving into the specifics of Custom Shielding, it is crucial to understand the fundamentals of shielding itself. Shielding is the process of creating a barrier that prevents electromagnetic waves from passing through, thus protecting sensitive electronic components and devices from interference. This interference can come from various sources, such as:
- Other electronic devices
- Power lines and electrical equipment
- Wireless communication signals
- Natural phenomena (e.g., lightning, solar flares)
Effective shielding requires the use of materials that can absorb, reflect, or redirect electromagnetic waves. The choice of material depends on factors such as the frequency range of the interference, the desired level of attenuation, and the physical properties of the shielded device or component.
Common Shielding Materials
There are several materials commonly used in shielding applications, each with its own advantages and limitations. Some of the most popular shielding materials include:
Metals
Metals are the most widely used materials for shielding due to their excellent conductivity and ability to reflect electromagnetic waves. Some common metals used in shielding include:
- Aluminum
- Copper
- Steel
- Nickel
- Silver
These metals can be used in various forms, such as sheets, foils, meshes, and coatings, depending on the specific application and design requirements.
Conductive Polymers
Conductive polymers are increasingly being used in shielding applications due to their lightweight, flexible, and moldable properties. These materials are created by incorporating conductive fillers, such as carbon nanotubes or metal particles, into a polymer matrix. Some examples of conductive polymers used in shielding include:
- Polyaniline (PANI)
- Polypyrrole (PPy)
- Poly(3,4-ethylenedioxythiophene) (PEDOT)
Conductive polymers offer a cost-effective alternative to metals in certain applications, particularly where weight and flexibility are important factors.
Composite Materials
Composite materials combine two or more materials to achieve desired properties, such as enhanced shielding effectiveness, mechanical strength, or thermal conductivity. Some examples of composite materials used in shielding include:
- Carbon fiber reinforced polymers (CFRP)
- Glass fiber reinforced polymers (GFRP)
- Metal matrix composites (MMC)
Composite materials can be tailored to meet specific shielding requirements while maintaining other desirable properties, such as lightweight and high strength-to-weight ratios.
Shielding Effectiveness
Shielding effectiveness (SE) is a measure of how well a shielding material or design attenuates electromagnetic waves. It is typically expressed in decibels (dB) and can be calculated using the following equation:
SE (dB) = 10 log₁₀ (Pi / Pt)
Where:
– Pi is the incident power of the electromagnetic wave
– Pt is the transmitted power through the shield
The higher the SE value, the better the shielding performance. The required SE for a given application depends on factors such as the sensitivity of the protected components, the intensity of the interference, and the regulatory requirements for the specific industry.
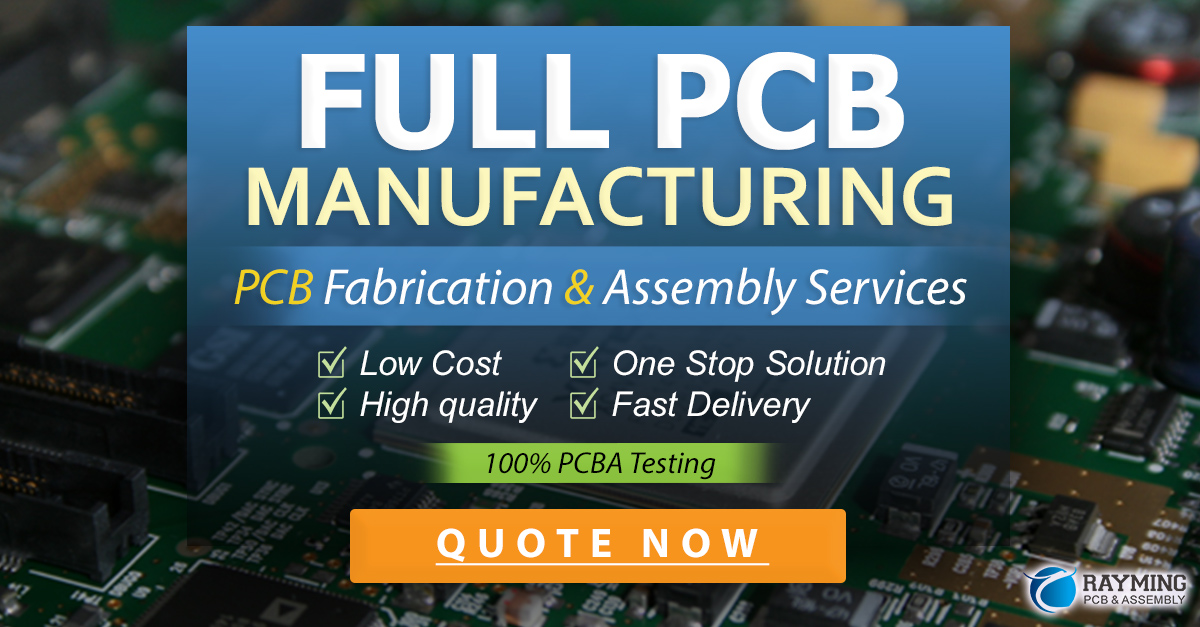
Factors Affecting Shielding Effectiveness
Several factors can influence the shielding effectiveness of a material or design. These include:
Frequency
The shielding effectiveness of a material varies with the frequency of the electromagnetic waves. Generally, higher frequencies are easier to shield against than lower frequencies, as the wavelengths are shorter and can be more easily absorbed or reflected by the shielding material.
Material Properties
The electrical conductivity, magnetic permeability, and Dielectric Constant of a material all contribute to its shielding effectiveness. Materials with higher conductivity and permeability tend to provide better shielding performance.
Thickness
Increasing the thickness of a shielding material generally improves its shielding effectiveness. However, there is a point of diminishing returns, beyond which increasing thickness provides minimal additional benefits.
Apertures and Seams
Any openings, gaps, or seams in a shielding enclosure can allow electromagnetic waves to leak through, reducing the overall shielding effectiveness. Careful design and proper sealing techniques are essential to minimize these leakages.
Grounding
Proper grounding is crucial for effective shielding. A well-designed grounding system ensures that any induced currents on the shield are safely directed to the ground, preventing them from interfering with the protected components.
Design Considerations for Custom Shielding
When designing custom shielding solutions, several key factors must be taken into account to ensure optimal performance and cost-effectiveness.
Application Requirements
The first step in designing custom shielding is to clearly define the application requirements. This includes identifying the frequency range of the interference, the desired level of attenuation, the physical constraints of the device or component being shielded, and any environmental factors (e.g., temperature, humidity, vibration) that may impact the shielding performance.
Material Selection
Based on the application requirements, the appropriate shielding material or combination of materials can be selected. Factors to consider include shielding effectiveness, weight, cost, manufacturability, and compatibility with other materials in the device or system.
Enclosure Design
The design of the shielding enclosure is critical to its overall effectiveness. Key considerations include:
- Minimizing apertures and seams
- Ensuring proper sealing and gasketing
- Providing adequate grounding points
- Accommodating any necessary cable entries or connectors
- Optimizing the shape and size of the enclosure for the specific application
Simulation and Testing
Before finalizing a custom shielding design, it is essential to perform simulations and testing to validate its performance. Electromagnetic simulation software can be used to model the shielding effectiveness of the design and identify potential weaknesses or areas for improvement. Physical testing, such as in an anechoic chamber or with specialized equipment, can provide real-world verification of the shielding performance.
Manufacturing Processes for Custom Shielding
Once a custom shielding design has been finalized, it must be manufactured using appropriate processes to ensure consistent quality and performance. Some common manufacturing processes for custom shielding include:
Stamping and Forming
Metal shielding components can be produced using stamping and forming techniques, which involve cutting, bending, and shaping metal sheets or foils into the desired geometry. This process is well-suited for high-volume production and can achieve tight tolerances and complex shapes.
Casting and Molding
For shielding components made from conductive polymers or composites, casting and molding processes are often used. These techniques involve injecting the material into a mold cavity under pressure and allowing it to cure or solidify into the final shape. Casting and molding offer the ability to create intricate geometries and integrate features such as mounting points or cable entries directly into the shielding component.
Machining
Machining processes, such as milling, turning, and drilling, can be used to create custom shielding components from solid blocks of metal or composite materials. This approach offers high precision and the ability to produce complex shapes, but it is generally more time-consuming and expensive than stamping or molding.
Coating and Plating
In some cases, shielding effectiveness can be enhanced by applying conductive coatings or plating to non-conductive substrates. Common coating and plating materials include nickel, copper, silver, and zinc. These processes can be used to create thin, lightweight shielding layers on plastic or composite components, improving their shielding performance without significantly increasing their weight or size.
Best Practices for Implementing Custom Shielding
To ensure the successful implementation of custom shielding in a device or system, consider the following best practices:
Early Collaboration
Engage with shielding experts and manufacturers early in the design process to identify potential challenges and optimize the shielding design for manufacturability and cost-effectiveness.
Iterative Design Process
Use an iterative design approach, incorporating simulation and testing feedback to refine the shielding design until the desired performance is achieved.
Proper Installation
Ensure that the custom shielding components are installed correctly, with proper sealing, grounding, and fastening techniques to maintain the intended shielding effectiveness.
Regular Maintenance
Establish a regular maintenance schedule to inspect and repair any damage or degradation to the shielding components, ensuring long-term performance and reliability.
Continuous Improvement
Monitor the performance of the custom shielding solution in the field and seek opportunities for continuous improvement, incorporating user feedback and advances in materials and manufacturing technologies.
FAQ
-
What is the difference between EMI and RFI shielding?
EMI (electromagnetic interference) and RFI (radio frequency interference) are both types of electromagnetic interference, but they refer to different frequency ranges. EMI typically covers a broader frequency range, from low frequencies up to several GHz, while RFI specifically refers to interference in the radio frequency spectrum, generally from 20 kHz to 300 GHz. Shielding solutions for EMI and RFI are often similar, but the specific materials and design approaches may vary depending on the frequency range of concern. -
Can custom shielding be retrofitted to existing devices?
Yes, in many cases, custom shielding solutions can be designed and manufactured to retrofit existing devices or systems. This may involve creating shielding enclosures that can be installed around the device or modifying the device itself to incorporate shielding components. However, retrofitting shielding can be more challenging than integrating it from the initial design stage, as space constraints and compatibility issues may need to be addressed. -
How do I determine the required shielding effectiveness for my application?
Determining the required shielding effectiveness for a specific application involves considering factors such as the sensitivity of the protected components, the intensity and frequency range of the expected interference, and any relevant regulatory requirements or industry standards. It is often helpful to consult with shielding experts or perform electromagnetic simulations to estimate the required shielding performance. In some cases, testing the device or system in its intended operating environment may be necessary to validate the shielding effectiveness. -
What are the most common challenges in designing custom shielding solutions?
Some of the most common challenges in designing custom shielding solutions include: - Balancing shielding effectiveness with other design requirements, such as weight, size, and cost
- Ensuring proper sealing and grounding to maintain shielding integrity
- Accommodating necessary openings or penetrations in the shielding enclosure for cables, connectors, or user interfaces
- Selecting materials that provide adequate shielding performance while also meeting other criteria, such as mechanical strength, thermal conductivity, or environmental resistance
-
Optimizing the shielding design for manufacturability and ease of assembly
-
How can I ensure the long-term reliability of my custom shielding solution?
To ensure the long-term reliability of a custom shielding solution, consider the following: - Select materials that are durable and resistant to environmental factors such as corrosion, temperature fluctuations, and mechanical stress
- Use robust sealing and fastening methods to maintain shielding integrity over time
- Implement a regular maintenance and inspection schedule to identify and address any degradation or damage to the shielding components
- Monitor the shielding performance periodically to ensure it continues to meet the application requirements
- Work with experienced shielding manufacturers and suppliers who can provide quality assurance and support throughout the product lifecycle
Conclusion
Custom shielding is a critical aspect of many electronic and electromagnetic applications, providing essential protection against interference and ensuring the reliable operation of sensitive components and devices. By understanding the principles of shielding, selecting appropriate materials, and following best practices for design, manufacturing, and implementation, engineers and product developers can create custom shielding solutions that meet the specific needs of their applications while balancing performance, cost, and reliability.
As technology continues to advance and the electromagnetic environment becomes increasingly complex, the demand for effective custom shielding solutions will only grow. By staying informed about the latest developments in materials, design tools, and manufacturing processes, and by collaborating with experienced shielding experts and suppliers, companies can position themselves to meet this demand and deliver products that are well-protected against electromagnetic interference.
Leave a Reply