What is a 94V 0 PCB?
A 94V 0 PCB, also known as a flame-retardant PCB, is a type of printed circuit board that has been treated with a special flame-retardant material to meet the UL 94V-0 flammability standard. This standard, set by Underwriters Laboratories (UL), ensures that the PCB has a high level of resistance to ignition and the spread of flames.
The “94” in 94V 0 refers to the UL 94 standard, while the “V” stands for vertical burning test, and the “0” indicates the highest level of flame retardancy. To achieve this rating, the PCB must self-extinguish within 10 seconds of being exposed to a flame, and the total burn time for five samples must not exceed 50 seconds.
Composition of 94V 0 PCBs
94V 0 PCBs are typically made from a combination of flame-retardant materials, such as:
- Brominated epoxy resin
- Phosphorus compounds
- Inorganic fillers (e.g., aluminum hydroxide, magnesium hydroxide)
These materials work together to inhibit the ignition and spread of flames, making the PCB safer for use in various applications.
Advantages of 94V 0 PCBs
Using 94V 0 PCBs offers several benefits, including:
- Enhanced safety: The flame-retardant properties of 94V 0 PCBs reduce the risk of fire, making them safer for use in various applications.
- Compliance with industry standards: Many industries, such as aerospace, automotive, and medical, require the use of flame-retardant PCBs to ensure product safety and reliability.
- Improved durability: 94V 0 PCBs are often more durable than non-flame-retardant PCBs, as the added materials can improve the board’s overall strength and resistance to environmental factors.
Applications of 94V 0 PCBs
94V 0 PCBs are used in a wide range of applications where fire safety is a critical concern. Some common applications include:
1. Aerospace and Aviation
In the aerospace and aviation industry, 94V 0 PCBs are used in various systems, such as:
- Avionics
- In-flight entertainment systems
- Lighting control systems
- Power distribution systems
These PCBs must withstand harsh environmental conditions, including extreme temperatures, vibrations, and humidity, while maintaining their flame-retardant properties.
2. Automotive Industry
The automotive industry relies on 94V 0 PCBs for various electronic systems, such as:
- Engine control units (ECUs)
- Infotainment systems
- Advanced driver assistance systems (ADAS)
- Lighting control systems
As vehicles become more reliant on electronic systems, the use of flame-retardant PCBs is essential to ensure passenger safety and prevent electrical fires.
3. Medical Devices
Medical devices, such as:
- Patient monitoring systems
- Diagnostic equipment
- Surgical instruments
- Implantable devices
These often require the use of 94V 0 PCBs to ensure patient safety and prevent fires in sensitive healthcare environments.
4. Industrial Control Systems
Industrial control systems, including:
- Programmable logic controllers (PLCs)
- Human-machine interfaces (HMIs)
- Supervisory control and data acquisition (SCADA) systems
These systems often use 94V 0 PCBs to ensure reliable operation in harsh industrial environments where the risk of fire is high.
5. Consumer Electronics
While not all consumer electronics require 94V 0 PCBs, some products, such as:
- High-end audio equipment
- Gaming systems
- Smart home devices
These products may use flame-retardant PCBs to enhance safety and comply with industry standards.
Manufacturing Process for 94V 0 PCBs
The manufacturing process for 94V 0 PCBs is similar to that of standard PCBs, with the addition of flame-retardant materials. The general steps involved in the process are:
- Design: The PCB layout is designed using computer-aided design (CAD) software, taking into account the specific requirements of the 94V 0 standard.
- Material selection: The appropriate flame-retardant materials, such as brominated epoxy resin and inorganic fillers, are selected based on the desired properties and performance of the PCB.
- Lamination: The flame-retardant materials are combined with the PCB substrate (typically FR-4) and copper foil to create a laminated stack.
- Drilling: Holes are drilled into the laminated stack to accommodate component leads and vias.
- Plating: The drilled holes are plated with copper to establish electrical connections between layers.
- Etching: Unwanted copper is removed from the PCB surface using a chemical etching process, leaving behind the desired circuit pattern.
- Solder mask application: A protective solder mask is applied to the PCB surface to prevent short circuits and improve the board’s durability.
- Silkscreen printing: Text, logos, and component outlines are printed onto the PCB surface using a silkscreen process.
- Surface finish: A surface finish, such as HASL (Hot Air Solder Leveling) or ENIG (Electroless Nickel Immersion Gold), is applied to the exposed copper to protect it from oxidation and improve solderability.
- Testing and inspection: The completed 94V 0 PCB undergoes various tests and inspections to ensure it meets the required specifications and performance criteria.
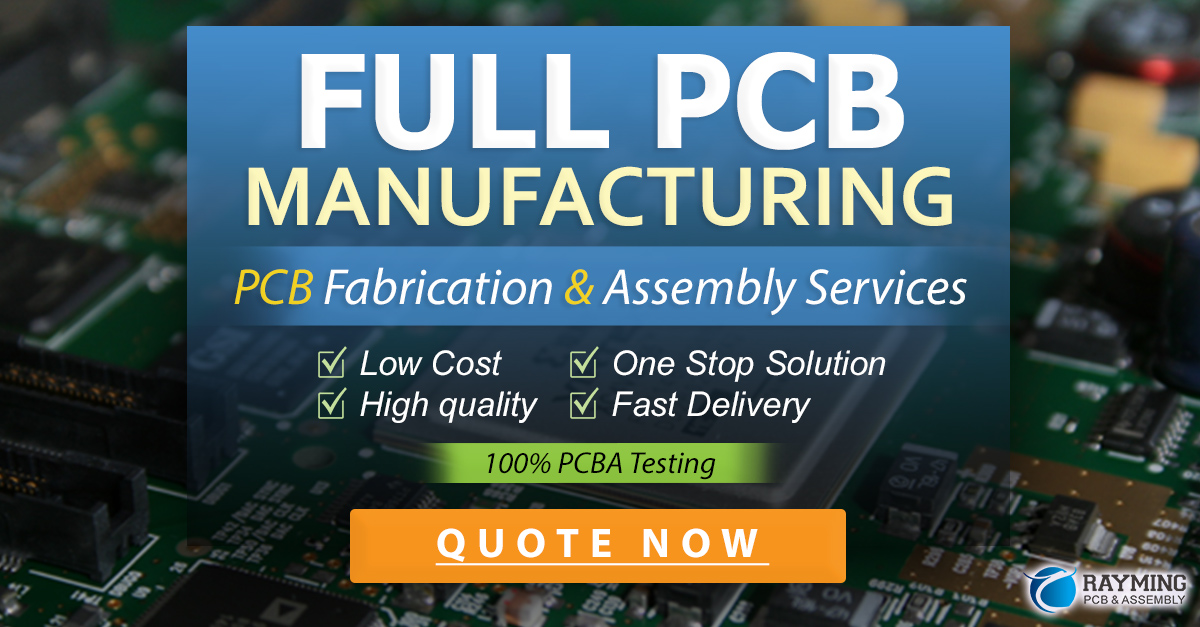
Choosing the Right 94V 0 PCB Manufacturer
When selecting a manufacturer for your 94V 0 PCB project, consider the following factors:
- Experience: Look for a manufacturer with extensive experience in producing flame-retardant PCBs, as they will have the knowledge and expertise to ensure your boards meet the necessary standards.
- Certifications: Ensure the manufacturer holds relevant certifications, such as ISO 9001, ISO 14001, and UL 94, to demonstrate their commitment to quality and compliance with industry standards.
- Capabilities: Consider the manufacturer’s capabilities, including their ability to handle complex designs, quick turnaround times, and competitive pricing.
- Quality control: Inquire about the manufacturer’s quality control processes, such as in-house testing, inspections, and traceability, to ensure the consistency and reliability of your 94V 0 PCBs.
- Customer support: Choose a manufacturer that offers excellent customer support, including responsive communication, technical assistance, and after-sales service.
By selecting a reputable 94V 0 PCB manufacturer, you can ensure that your PCBs meet the necessary flame-retardant standards and perform reliably in your intended application.
Frequently Asked Questions (FAQ)
1. What is the difference between 94V 0 and 94V 2 PCBs?
94V 0 and 94V 2 are both flame-retardant PCB ratings under the UL 94 standard. The main difference is that 94V 0 represents the highest level of flame retardancy, while 94V 2 is a lower level. 94V 0 PCBs must self-extinguish within 10 seconds of being exposed to a flame, while 94V 2 PCBs have a slightly longer allowable burn time.
2. Can 94V 0 PCBs be used in all applications?
While 94V 0 PCBs offer excellent flame-retardant properties, they may not be necessary or suitable for all applications. Some factors to consider include the specific requirements of your application, the associated costs, and any potential trade-offs in terms of PCB performance or manufacturability.
3. Are 94V 0 PCBs more expensive than non-flame-retardant PCBs?
Yes, 94V 0 PCBs are generally more expensive than non-flame-retardant PCBs due to the added cost of the flame-retardant materials and the specialized manufacturing processes required. However, the increased safety and compliance with industry standards often justify the higher cost in applications where fire safety is a critical concern.
4. Can 94V 0 PCBs be recycled?
The presence of flame-retardant materials in 94V 0 PCBs can make them more challenging to recycle compared to non-flame-retardant PCBs. However, many PCB Recycling facilities have developed specialized processes to handle flame-retardant PCBs safely and efficiently. It is essential to work with a reputable recycling facility to ensure proper disposal and minimize environmental impact.
5. Are there any health concerns associated with 94V 0 PCBs?
Some flame-retardant materials used in 94V 0 PCBs, such as brominated compounds, have been associated with potential health concerns. However, when properly manufactured and handled, the risks are minimal. It is essential to work with reputable manufacturers who adhere to strict safety and environmental standards and to follow proper handling and disposal procedures to minimize any potential health risks.
Conclusion
94V 0 PCBs play a crucial role in ensuring fire safety and reliability in various applications, from aerospace and automotive to medical devices and industrial control systems. By incorporating specialized flame-retardant materials, these PCBs meet the stringent UL 94V-0 flammability standard, providing enhanced protection against ignition and the spread of flames.
When selecting a 94V 0 PCB for your application, it is essential to consider factors such as the specific requirements of your industry, the associated costs, and the potential trade-offs in terms of performance and manufacturability. By working with a reputable PCB manufacturer and following proper handling and disposal procedures, you can ensure that your 94V 0 PCBs meet the necessary safety standards and perform reliably in your intended application.
As technology continues to advance and the demand for fire-safe electronics grows, the importance of 94V 0 PCBs will only continue to increase. By understanding the properties, applications, and manufacturing processes associated with these specialized PCBs, you can make informed decisions and ensure the safety and reliability of your electronic products.
Leave a Reply