Receiving Inspection
The first step in effective component storage is conducting a thorough receiving inspection when parts and materials arrive at the facility. This process helps verify that the received items match the purchase order specifications, meet quality requirements, and are free from damage or defects. Here are some essential elements of a receiving inspection:
Visual Examination
Upon receipt, components should be visually examined for any signs of damage, such as:
– Dents, cracks, or deformations
– Scratches, abrasions, or surface defects
– Corrosion, contamination, or discoloration
– Broken or missing parts
– Improper packaging or labeling
Any discrepancies or anomalies should be documented and reported to the supplier for corrective action.
Dimensional Verification
Key dimensions and tolerances of the received components should be measured and compared against the drawing or specification requirements. This can be done using various measuring instruments, such as:
– Calipers
– Micrometers
– Gauges
– Coordinate measuring machines (CMMs)
– Optical comparators
A sampling plan based on the lot size and criticality of the components can be used to determine the appropriate inspection level.
Material Certification
For critical components or materials, suppliers may be required to provide material certifications, test reports, or certificates of conformance (COCs). These documents should be reviewed to ensure that the materials meet the specified chemical composition, mechanical properties, and performance characteristics. Some common certifications include:
Certification | Description |
---|---|
Mill Test Report (MTR) | Verifies the chemical composition and mechanical properties of raw materials, such as metals and alloys. |
Certificate of Analysis (COA) | Provides the results of chemical, physical, or microbiological tests performed on materials, such as polymers, elastomers, or chemicals. |
Certificate of Compliance (COC) | Attests that the supplied components or materials meet the specified requirements, standards, or regulations. |
Functional Testing
Depending on the nature and criticality of the components, functional testing may be performed to verify their performance and reliability. This can involve:
– Electrical testing (e.g., continuity, insulation resistance, dielectric strength)
– Mechanical testing (e.g., tensile strength, hardness, impact resistance)
– Environmental testing (e.g., temperature, humidity, vibration, shock)
– Optical testing (e.g., reflectance, transmittance, color)
The test methods and acceptance criteria should be based on the relevant industry standards, customer requirements, or internal specifications.
Storage Conditions
Once the received components have passed the inspection process, they must be stored in appropriate conditions to maintain their quality and integrity. The storage environment should be designed to protect the components from various factors that can cause deterioration or damage, such as:
- Temperature extremes
- Humidity
- Dust, dirt, and debris
- Electrostatic discharge (ESD)
- Ultraviolet (UV) radiation
- Chemical exposure
- Physical impact or vibration
The specific storage requirements may vary depending on the type of components and their sensitivity to environmental factors. Here are some general guidelines for storing different categories of components:
Component Category | Storage Conditions |
---|---|
Electronic components | – Temperature: 15°C to 30°C – Humidity: 30% to 70% RH – ESD protection: Grounded workstations, conductive packaging – Moisture-sensitive devices (MSDs): Dry cabinet or nitrogen storage |
Mechanical components | – Temperature: 10°C to 30°C – Humidity: 30% to 60% RH – Corrosion protection: Rust preventives, desiccants, or vacuum packaging – Segregation by material type (e.g., metals, plastics, elastomers) |
Chemicals and adhesives | – Temperature: As per manufacturer’s recommendations – Humidity: As per manufacturer’s recommendations – Ventilation: Adequate exhaust and air circulation – Safety: Proper labeling, segregation of incompatible materials, spill containment |
Printed circuit boards (PCBs) | – Temperature: 15°C to 30°C – Humidity: 30% to 50% RH – ESD protection: Grounded workstations, conductive packaging – Stacking: Vertical or horizontal, with appropriate support and separator materials |
Inventory Control
Effective inventory control is essential for optimizing component storage, minimizing waste, and ensuring the availability of parts and materials when needed. Some key elements of inventory control include:
Stock Rotation
Components should be stored and used on a first-in, first-out (FIFO) basis to minimize the risk of obsolescence or expiration. This can be achieved by:
– Labeling components with receipt dates or lot numbers
– Organizing storage locations by date or sequence of receipt
– Regularly reviewing and updating inventory records
– Monitoring shelf life and expiration dates of perishable materials
Minimum/Maximum Levels
Establishing minimum and maximum stock levels for each component helps maintain an optimal balance between availability and inventory carrying costs. This involves:
– Analyzing historical usage data and demand forecasts
– Determining safety stock levels to buffer against supply disruptions or demand fluctuations
– Setting reorder points and quantities based on lead times and economic order quantities (EOQs)
– Regularly reviewing and adjusting stock levels based on changes in demand or supply conditions
Cycle Counting
Periodic physical counts of components in storage help verify the accuracy of inventory records and identify any discrepancies or anomalies. Cycle counting can be performed on a rotating basis, focusing on different categories or locations of components each time. The frequency and scope of cycle counts may depend on factors such as:
– Component value or criticality
– Transaction volume or frequency
– Historical accuracy of inventory records
– Regulatory or customer requirements
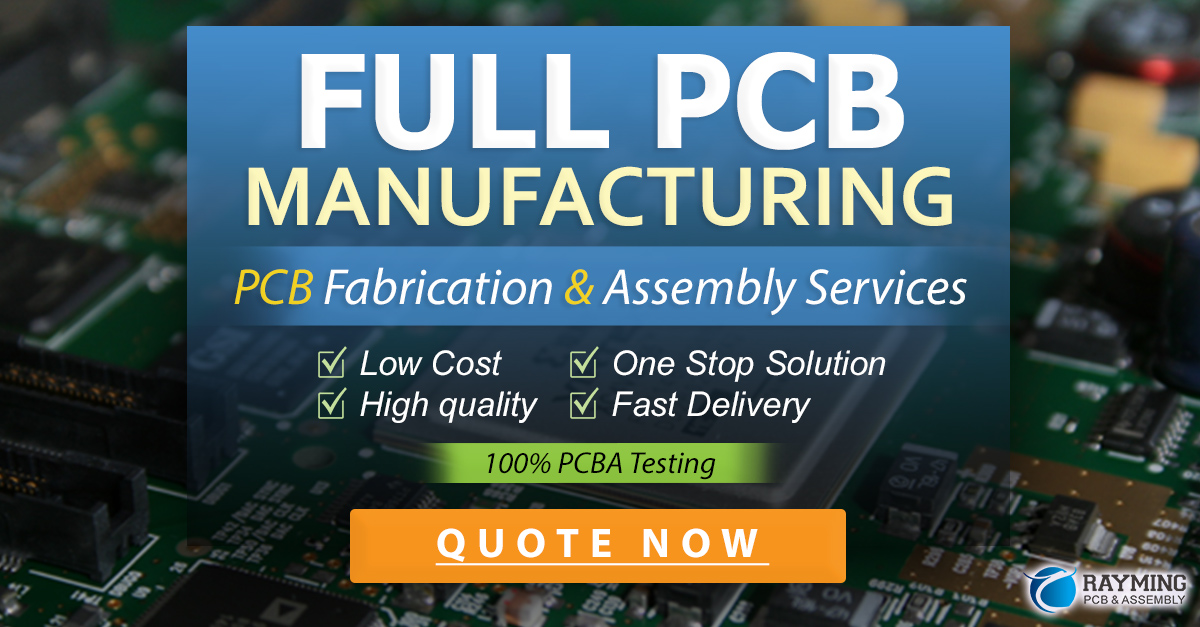
Documentation
Proper documentation is crucial for maintaining traceability, accountability, and compliance in component storage. Some essential documents and records include:
Receiving Reports
Receiving reports document the receipt of components, including information such as:
– Purchase order number
– Supplier name and contact details
– Part number, description, and quantity received
– Date and time of receipt
– Receiving inspector’s name and signature
– Any discrepancies or nonconformances noted during the inspection
Material Certifications
As mentioned earlier, material certifications provide evidence of the quality and compliance of the received components. These documents should be collected, reviewed, and filed along with the receiving reports for future reference.
Inventory Records
Inventory records keep track of the stock levels, transactions, and locations of components in storage. These records can be maintained using manual or electronic systems, such as:
– Spreadsheets
– Databases
– Enterprise resource planning (ERP) software
– Warehouse management systems (WMS)
The inventory records should include information such as:
– Part number and description
– Quantity on hand, on order, and allocated
– Storage location and bin number
– Unit of measure and cost
– Reorder point and quantity
– Supplier and lead time
Traceability Records
Traceability records help link the components used in production to their original source and receiving information. This can be achieved by assigning unique lot numbers or serial numbers to the components and recording them in the production or assembly documents, such as:
– Work orders
– Travelers
– Bills of materials (BOMs)
– Quality control records
Traceability records are particularly important for regulated industries, such as aerospace, automotive, or medical devices, where the ability to recall or investigate nonconforming products is essential.
Frequently Asked Questions (FAQ)
-
Q: What is the purpose of conducting a receiving inspection for components?
A: The purpose of conducting a receiving inspection is to verify that the received components meet the specified requirements in terms of quantity, quality, and condition. It helps identify any discrepancies or nonconformances before the components are accepted into storage or used in production. -
Q: How can electronic components be protected from electrostatic discharge (ESD) during storage?
A: Electronic components can be protected from ESD by using ESD-safe storage containers, such as conductive or dissipative bins, bags, or racks. The storage area should also have grounded workstations and flooring to minimize the buildup of static charges. Personnel handling the components should wear ESD-protective gear, such as wrist straps or heel grounders. -
Q: What is the difference between FIFO and LIFO in inventory management?
A: FIFO (first-in, first-out) and LIFO (last-in, first-out) are two methods of inventory valuation and rotation. In FIFO, the oldest components are used or sold first, while in LIFO, the newest components are used or sold first. FIFO is generally preferred for component storage to minimize the risk of obsolescence or expiration, while LIFO may be used for accounting purposes in some cases. -
Q: How can the shelf life of components be monitored and managed?
A: The shelf life of components can be monitored and managed by: - Recording the receipt date or expiration date of each lot or batch
- Labeling the components or storage locations with the shelf life information
- Regularly reviewing the inventory records to identify components nearing expiration
- Using FIFO rotation to ensure that older components are used first
-
Disposing of expired or deteriorated components according to appropriate procedures
-
Q: What are some common challenges in managing component storage and how can they be addressed?
A: Some common challenges in managing component storage include: - Limited storage space: Optimize storage layouts, use vertical space, and implement lean inventory practices
- Obsolescence: Regularly review and update inventory based on demand forecasts, engineering changes, and product lifecycles
- Damage or deterioration: Ensure proper storage conditions, handling procedures, and packaging materials
- Inaccurate inventory records: Perform regular cycle counts, use barcoding or RFID technology, and integrate inventory systems with other business processes
- Traceability: Assign unique identifiers to components, maintain detailed receiving and production records, and use inventory management software with traceability features
By addressing these challenges through a combination of best practices, technology solutions, and continuous improvement initiatives, companies can effectively manage their component storage and ensure the quality, availability, and efficiency of their production processes.
Leave a Reply