Advantages of BGA Packages
Before diving into BGA design guidelines, it’s important to understand the key benefits BGAs offer compared to other IC package types:
- High I/O density (up to 1000+ pins)
- Reduced package size
- Shorter lead lengths for better electrical performance
- Lower profile and weight
- More efficient heat dissipation
- Compatibility with SMT Assembly
These advantages make BGAs an attractive choice for applications requiring high pin counts and performance in a small form factor, such as processors, FPGAs, ASICs, and memory devices.
BGA Design Considerations
Designing a robust and manufacturable BGA requires balancing several interdependent factors:
1. Ball Pitch and Size
The ball pitch (distance between ball centers) and ball size are critical parameters affecting BGA design. Smaller pitches enable higher density but increase manufacturing complexity and cost. Common BGA pitches range from 0.5mm to 1.27mm, with 0.8mm and 1.0mm being most prevalent.
Pitch (mm) | Ball Diameter (mm) | Package Density | Manufacturing Complexity |
---|---|---|---|
1.27 | 0.75 | Low | Lowest |
1.0 | 0.6 | Medium | Low |
0.8 | 0.5 | High | Moderate |
0.5 | 0.3 | Very High | High |
In general, it’s recommended to use the largest acceptable pitch for your application to facilitate manufacturing. Smaller pitches (<0.8mm) may require more advanced PCB Fabrication and assembly capabilities, increasing cost.
2. PCB Layout
The PCB layout is a crucial aspect of BGA design. Proper PCB layout techniques help ensure signal integrity, minimize crosstalk, and improve manufacturability. Some key BGA PCB layout guidelines include:
- Fan-out BGA pads to larger SMD pads for easier soldering
- Provide adequate spacing between pads and traces
- Avoid acute angles in traces
- Use ground planes for shielding and heat dissipation
- Follow controlled impedance routing rules
- Keep traces as short as possible
Failing to adhere to good PCB layout practices can lead to issues like unintended RF coupling, excessive noise, and manufacturing defects that compromise reliability.
3. Thermal Management
BGAs concentrate a high number of hot components in a small area, making thermal management a key concern. Overheating can degrade device performance, reduce reliability, and even cause premature failure.
Effective BGA thermal management techniques include:
- Using thermally enhanced BGA substrates (e.g. metal cores)
- Providing adequate thermal vias and planes
- Integrating heat spreaders or heat sinks
- Optimizing airflow in enclosure design
- Selecting lower power components when possible
Careful thermal simulation and characterization during the design phase is recommended to validate the thermal solution.
4. Interconnect Selection
The choice of interconnect technology within the BGA itself impacts performance and manufacturability. The most common BGA substrate materials are:
Material | Advantages | Disadvantages |
---|---|---|
Laminate | Lower cost, wide availability | Higher impedance, limited layer count |
Polyimide | Thin dielectric, flexible | Moderate cost, potential CTE mismatch |
Ceramic | Excellent high frequency performance, reliability | High cost, fragility, difficult rework |
Within each category, there are additional options that trade off layer counts, via density, impedance control, and cost. Work closely with your BGA package vendor to select the optimal technology for your specific design needs.
5. Design for Test (DFT)
Designing BGAs for testability is essential for detecting manufacturing defects and ensuring long-term reliability. Some standard BGA DFT techniques are:
- Providing accessible test points
- Minimizing the number of non-testable nets
- Following JTAG boundary scan design rules
- Avoiding components that block test access to BGA balls
- Using built-in self test (BIST) features when available
Considering DFT upfront in the design process minimizes test development effort and maximizes coverage, ultimately reducing manufacturing costs.
BGA Manufacturing Process Optimization
Achieving high yields and reliability with BGA manufacturing requires a robust and well-characterized assembly process. Key process variables to optimize include:
- Solder paste: Selection of solder alloy, sphere size, and flux chemistry
- Stencil design: Aperture size/shape, thickness, and nanocoating
- Reflow profile: Ramp rates, soak time, peak temperature, and cooling rate
- Inspection: Post-reflow automated optical/x-ray inspection criteria
Each of these variables should be experimented with and fine-tuned based on the specific BGA package and PCB design. Investing in process characterization upfront can significantly improve manufacturing metrics.
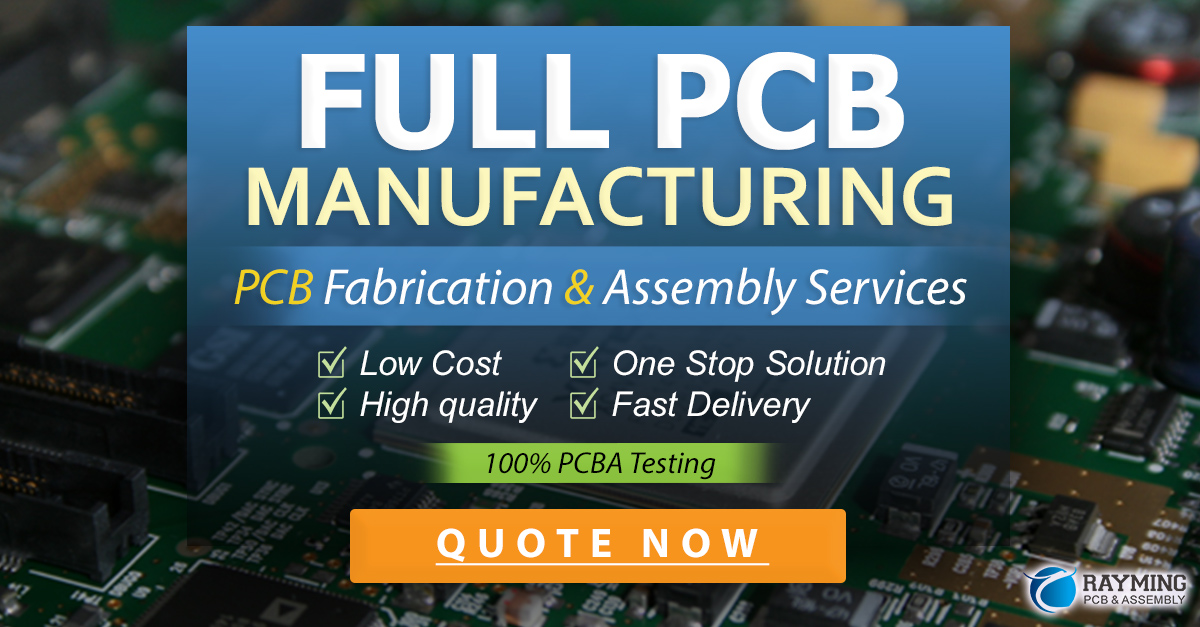
BGA Rework and Repair
Despite the best design and process controls, BGA manufacturing defects can still occur. Having a well-defined BGA rework and repair strategy is essential for minimizing scrap and maximizing yields.
Common BGA defects that may require rework include:
- Shorts between balls
- Opens due to insufficient solder
- Misalignment/tombstoning
- Voids in solder joints
BGA rework typically involves localized heating to remove the defective component, cleaning and preparing the site, and installing a new component. This process requires specialized equipment and skilled technicians to execute reliably.
To facilitate BGA rework, consider the following design guidelines:
- Provide rework access to BGA site (avoid tall adjacent components)
- Use BGA substrates compatible with multiple rework heating methods
- Minimize use of underfill/overmold that hinder component removal
- Ensure compatibility of all BGA materials (package, solder, PCB)
While BGA rework is sometimes necessary, it is still a time-consuming and costly process. Aim to minimize rework through robust design and process control.
Cost Reduction Strategies
Ultimately, most BGA design decisions must balance performance and reliability against cost. Some effective ways to reduce BGA costs include:
- Standardizing on common package footprints, pitch, and ball count
- Minimizing use of blind/buried vias in substrates
- Designing for standard PCB design rules and process capabilities
- Using chip array BGA (CABGA) vs tape/laminate substrates when possible
- Negotiating volume pricing for substrates, assembly, and test services
Look for opportunities to reduce cost throughout the design phase while still meeting performance and reliability objectives. Over-designing BGAs leads to unnecessary expense.
Frequently Asked Questions
How does BGA pitch affect manufacturing cost?
A: Smaller BGA pitches (<0.8mm) require more precise and expensive PCB fabrication and assembly processes, such as high-resolution solder paste printing, placement, and inspection. In general, a larger pitch will be more cost effective.
Are QFNs a lower-cost alternative to BGAs?
A: For lower pin counts (<100), Quad Flat No-lead (QFN) packages can be a cheaper option than BGAs due to their simpler construction and assembly process. However, QFNs have worse thermal dissipation and are not suitable for very high I/O devices.
What is the most critical BGA manufacturing process variable?
A: Solder paste print quality is arguably the most important factor for BGA manufacturing yields. Printing the optimal paste volume, shape, and alignment is key to forming robust solder joints and avoiding defects. Stencil design, paste characteristics, and print parameters must be carefully optimized.
How much does BGA rework cost?
A: BGA rework costs vary based on many factors such as device size, construction, and quantity. As a general estimate, reworking a single BGA component can cost $50-$100 in materials and labor, assuming a mature rework process. Rework of more complex BGAs with higher layer counts or dense pitches can exceed $200 per component.
Are there any low-cost BGA substrate options?
A: CABGA substrates, which use a simple pad-to-pad PCB array design, are the lowest cost BGA option for low I/O devices. CABGA substrates leverage standard PCB materials and processes for lower cost than tape, polyimide, and ceramic. However, CABGAs are typically limited to 2-4 layers and pitches over 0.8mm.
Conclusion
BGAs are a powerful packaging technology for achieving high performance and functionality in a small footprint. However, realizing these benefits requires carefully balancing electrical, thermal, and mechanical requirements with manufacturing and cost realities.
By understanding the key design variables and tradeoffs, it’s possible to create BGA designs that are high-yielding, reliable, and cost effective in volume production. Adhering to proven manufacturability guidelines, leveraging industry standards where possible, and partnering with experienced suppliers enables designers to unlock the full potential of BGAs.
Leave a Reply