Ceramic printed circuit boards provide high thermal conductivity and thermal management capabilities exceeding traditional FR4 PCBs. However, the thermal conductivity varies based on the specific ceramic material used in the PCB substrate.
This article discusses the thermal conductivity ranges observed in various ceramic PCB materials and their implications on PCB thermal design.
Importance of Thermal Conductivity in PCBs
A PCB’s thermal conductivity indicates its ability to conduct heat. It is a key property impacting the PCB’s thermal performance.
Higher thermal conduction allows efficient spreading and dissipation of heat from embedded components and conductors carrying high electrical currents. This prevents localized heating and hot spots.
Managing the thermal conductivity difference between the PCB substrate and components is crucial for circuit stability, longevity and reliability.
Thermal Conductivity of Common Ceramic PCB Materials
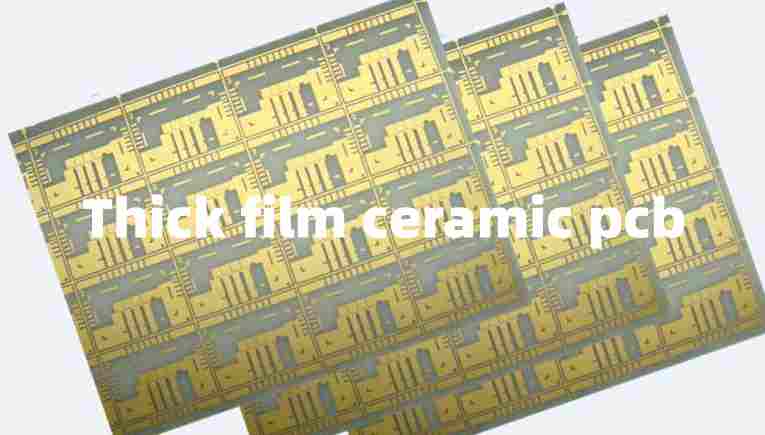
Some typical thermal conductivity values of ceramic materials used in PCB substrates are:
- Alumina (Al2O3) – 30 W/mK
- Aluminum Nitride (AlN) – 170 W/mK
- Beryllium Oxide (BeO) – 250 W/mK
- Silicon Nitride (SiN) – 100 W/mK
This compares with only 0.25 W/mK thermal conductivity offered by standard FR4 material.
So ceramic PCBs provide a thermal conductivity boost of over 100X compared to FR4 PCBs. But the magnitude varies substantially based on material choice.
Factors Affecting Thermal Conductivity
Some factors that influence the thermal conductivity of ceramic PCBs are:
Ceramic Composition
Purity levels and sintering aids added to the ceramic affect thermal conduction. Higher purities improve conductivity.
Grain Structure
Finer, uniform microstructures provide lower thermal resistance across grain boundaries.
Porosity
Pores and voids act as insulating regions that impede heat flow. Full densification during sintering is critical.
Temperature
Thermal conductivity reduces at higher temperatures as phonon scattering increases.
Direct Copper Bonding
Bonding a pure copper layer directly to the ceramic improves lateral heat spreading.
Thermal Design Considerations
The thermal conductivity impacts PCB thermal design in multiple ways:
Heat Sinking
Higher conductivity ceramics like AlN allow the PCB itself to function as a heat sink.
Copper Area Provision
Sufficient copper heat spreading planes and thermal vias should be allocated.
Power Plane Layout
Strategic placement of power and ground planes aids heat transfer to ambient.
Layer Stacking Sequence
Heat generating components are ideally placed on layers interfacing with the ceramic substrate.
Thermal Via Distribution
Adequate thermal vias help conduct heat between layers and to the board edges.
Thermal Interface Materials (TIM)
TIMs between the PCB and enclosure or heat sink reduce contact resistance.
Cooling Provisions
Heatsinks, fans and liquid cooling channels can supplement the PCB’s heat dissipation.
Comparison of Ceramic PCB and FR4 Thermal Conductivity
Typical thermal conductivity values are:
- Alumina PCB: 30 W/mK
- Aluminum Nitride PCB: 170 W/mK
- FR4 PCB: 0.25 W/mK
So even the lowest conducting alumina PCB provides over 100 times higher thermal conductivity compared to standard FR4 material. This significant improvement allows ceramic PCBs to manage substantial heat loads.
Thermal Conductivity Testing Methods
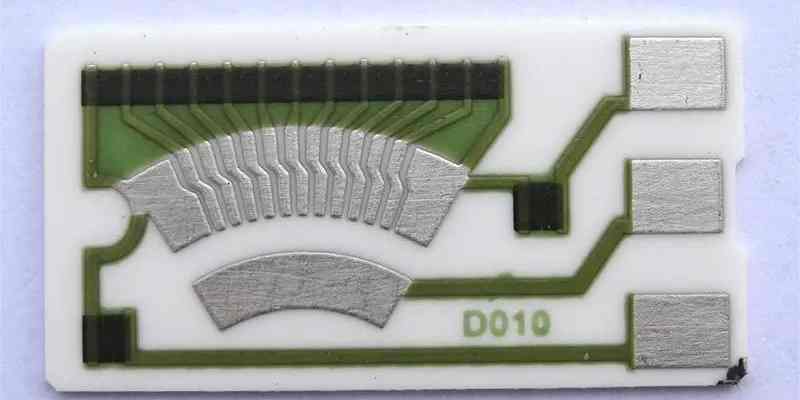
Some methods used to measure PCB thermal conductivity are:
- Laser Flash Analysis: Transient heating and cooling analysis to determine thermal diffusivity and conductivity.
- Hot Plate Method: Measuring temperature response to heat flow across sample between hot and cold plates.
- Infrared Thermography: Using IR cameras to assess temperature gradients and heat spreading.
- Thermal Impedance Probing: Applying heat stimulus and measuring temperature rise to calculate impedance.
- Microwave Resonator: Measuring shift in resonant frequency corresponding to thermal conductivity.
Improving Thermal Conductivity
Some ways to enhance thermal conduction in ceramic PCBs are:
- Using higher purity ceramic formulation
- Incorporating more thermally conductive filler particles
- Reducing ceramic porosity via optimized sintering
- Using direct copper bonding to ceramic
- Incorporating thicker copper heat spreaders
- Adding insulating metal layers like aluminum or Kovar
- Using thermally conductive adhesives for attaching components
Ceramic PCB Thermal Management Examples
- Alumina PCBs used in LED driver boards to dissipate heat from high power LEDs.
- Aluminum nitride PCBs used in power electronics modules to spread heat from power devices.
- Thick beryllium oxide PCBs used in downhole drilling tools to withstand high temperatures.
- LTCC alumina boards used in RF power amplifiers to prevent signal distortion at high temperatures.
- Alumina substrates with direct bonded copper used in automotive ignition modules requiring extreme temperature swings.
FAQs
Which ceramic material has the highest thermal conductivity?
Beryllium oxide has the highest thermal conductivity among ceramic PCB substrate materials, rated around 250-300 W/mK. However, toxicity concerns of beryllium limit its usage.
Does ceramic PCB thermal conductivity vary with temperature?
Yes, the thermal conductivity reduces slightly at higher temperatures as phonon scattering increases. This must be considered in thermal simulations.
Can you drill holes in ceramic PCBs?
Yes, holes can be drilled through ceramic PCBs using diamond coated carbide bits. Non-circular shaping is possible but challenging.
Does ceramic PCB thermal conductivity depend on thickness?
Thermal conductivity is an intrinsic material property independent of PCB thickness. Only the thermal resistance varies with thickness.
Is alumina a good thermal conductor?
Though not as high as metals, alumina has relatively good thermal conductivity for an electrical insulator. This makes alumina ceramic well-suited for thermal management PCB substrates.
In summary, ceramic PCBs offer thermal conductivity exceeding 100X that of FR4 boards. But the magnitude spans a wide range based on the specific ceramic material and its composition. Proper thermal design is key to leverage the improved heat dissipation capabilities.
Leave a Reply