Alumina (aluminum oxide – Al2O3) ceramic is a popular substrate material used in electronics manufacturing. Alumina substrates offer various benefits that make them well-suited for demanding applications.
This article discusses the key advantages and typical uses of alumina substrates.
What is Alumina Substrate?
Alumina substrate consists of a base plate or sheet made from aluminum oxide ceramic, which serves as the foundation to build electronic circuits and components.
Alumina provides an insulating yet thermally conductive foundation for the fabrication of printed circuit boards (PCB), lead frames, thermal boards, high power modules and other electronics.
The substrate properties can be tailored by varying the alumina purity levels. High purity alumina (99.5-99.9%) offers superior performance.
Benefits of Alumina Ceramic Substrate
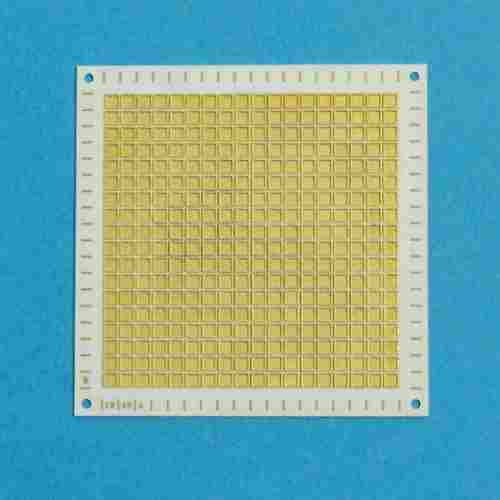
Some of the major advantages of using alumina substrate include:
Electrical Insulation
Alumina is an excellent electrical insulator, with high volume resistivity exceeding 10^14 ohm-cm even at elevated temperatures. This enables alumina substrates to isolate circuits and prevent current leakage.
Thermal Conductivity
Alumina exhibits high thermal conductivity, ranging from 10 W/mK for 85% alumina to 30 W/mK for 99.6% pure alumina. This allows alumina substrates to dissipate heat efficiently from power devices.
Low Thermal Expansion
The thermal expansion coefficient of alumina is around 7 ppm/K. This is significantly lower than that of polymers and closer to silicon. Thermal stresses between silicon devices and alumina substrates is minimized.
High Temperature Stability
Alumina retains its properties like strength, insulation and corrosion resistance at elevated temperatures. It has continuous operating temperature capability exceeding 1000°C.
Wear and Abrasion Resistance
Alumina ceramics offer excellent resistance to surface wear and abrasion. The hardness helps resist scratches and dents during handling and use.
Chemical Inertness
Alumina exhibits high chemical stability and inertness to acids, organic solvents and alkaline solutions. Harsh process chemicals do not degrade alumina substrates.
Compatibility with Metallization
Alumina readily bonds with metallization layers like tungsten, copper and gold. This allows fabrication of conductors directly on the alumina surface.
Hermetic Sealing
Being an oxide, alumina permits air-tight bonding with solders and brazes to seal components mounted on its surface. This hermetic sealing protects against external contaminants.
Dielectric Strength
Alumina has dielectric strength exceeding 15kV/mm. This allows alumina substrates to be used in high voltage and power electronics applications.
Lightweight
Alumina has a lower density around 3.9 g/cm<sup>3</sup> compared to most other ceramics. This results in lighter weight substrate solutions.
Applications of Alumina Substrates
Some of the major applications of alumina ceramic substrates include:
Power Electronics
High thermal conductivity, electrical insulation and high temperature stability make alumina ideal for power module substrates used in converters, inverters, regulators etc.
Automotive Electronics
Alumina backboards provide low thermal expansion and thermal management for automotive electronics operating under hood where temperatures can reach 150°C.
Aerospace and Military
Ruggedness, insulation and heat dissipation abilities of alumina substrates allow them to meet the stringent requirements of aerospace and defense systems.
RF Wireless Devices
Alumina is used as substrate for high frequency wireless communication circuits and antenna modules.
LED Lighting
LEDs run hot requiring low thermal expansion and thermally conductive substrates, which alumina fulfills.
Consumer Electronics
Tablets, cameras and wearables with constrained space rely on alumina substrates to pack higher density electronics.
Medical Implants
Biocompatible alumina substrates house circuitry for implants like cochlear and pacemakers where reliability is paramount.
Sensors
Alumina substrate’s electrical insulation and chemical resistance supports sensitive sensor components and interconnects.
Alumina PCB Substrates
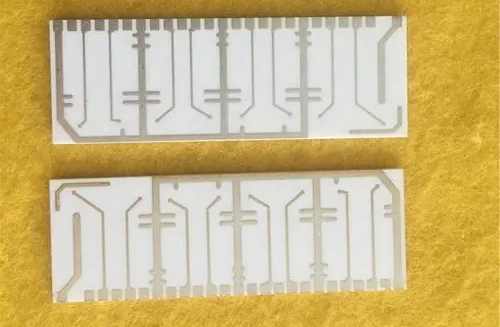
Alumina PCBs utilize alumina ceramic as the substrate material in place of conventional FR4 laminates. This enables fabrication of circuit boards with:
- Excellent thermal conductivity for heat dissipation
- High temperature capability exceeding 250°C
- Resistance to harsh chemicals for industrial environments
- Insulation up to 1000V for high voltage needs
- Hermetic sealing of mounted components
Alumina PCBs meet size, layout and density needs comparable to conventional PCBs. They provide a robust and miniaturized solution for industrial controls, aerospace systems and automotive electronics.
Alumina Substrate vs. Aluminum Nitride
Aluminum nitride (AlN) is another advanced ceramic substrate option competing with alumina, offering some pros and cons:
Advantages of AlN:
- Higher thermal conductivity up to 180 W/mK
- Lower coefficient of thermal expansion at 4.5 ppm/K
- Matches silicon CTE better than alumina
Disadvantages of AlN:
- More expensive material than alumina
- Lower electrical insulation capability
- Susceptible to cracking from tensile stresses
- Difficult to fully densify during sintering
So for ultimate thermal performance, AlN may be chosen but alumina offers a more well-rounded substrate solution considering cost, mechanical and electrical factors.
Direct Bonded Copper (DBC) Substrates
DBC substrates involve an alumina or AlN plate direct bonded with a thin copper layer for circuit fabrication. DBC substrates provide:
- Ideal flatness for mounting bare ICs and dies
- Direct heat sinking of components into copper
- Excellent thermal spreading and conductivity
DBC alumina substrates are commonly used for power modules and automotive electronics operating under high heat and power cycling conditions.
Metallized Alumina
To allow conductor traces to be patterned directly on the alumina surface, metallization is applied which bonds strongly with alumina.
Common alumina substrate metallizations include:
- Tungsten (W): Provides the best adhesion to alumina but has higher resistivity.
- Molybednum-Manganese (MoMn): Offers reasonable adhesion and intermediate resistivity.
- Copper-Tungsten (CuW): Gives better electrical conductivity than W or MoMn.
The metallized alumina is then ready for further metal and dielectric layer buildup, etching, component assembly and other PCB fabrication processes.
Alumina Substrate Manufacturers
Some of the major alumina substrate manufacturers include:
- Kyocera
- Maruwa
- Tong Hsing
- Holy Stone
- ICP Technology
- Mitsubishi Materials Corporation (MMC)
- CoorsTek
These companies offer a wide range of alumina substrate products and can fabricate custom alumina boards and ceramic assemblies.
FAQs
Is alumina hydrophilic or hydrophobic?
Alumina possesses a hydrophilic surface which tends to absorb water and moisture. This requires hermetic sealing of alumina packages to prevent moisture ingress.
Does alumina thermally expand?
Yes, alumina does undergo thermal expansion when heated and contracts when cooled like most materials. But its low expansion coefficient minimizes thermal stresses between alumina and contacting materials.
Can alumina substrate be soldered?
Yes, alumina permits wetting and soldering using high temperature solders. Active brazing alloys that chemically bond with alumina oxides produce the strongest joints.
What causes cracks in alumina?
Alumina is vulnerable to cracking from excessive tensile stresses, thermal shocks, grinding damage, component overloading and improper handling. Cracks degrade its insulating and mechanical properties.
Is alumina toxic?
No, alumina is considered non-toxic and biologically inert. Its biocompatibility allows the use of alumina ceramics for joint replacements and dental implants within the human body.
In summary, alumina substrates provide an optimal combination of electrical insulation, thermal conductivity, mechanical rigidity, chemical resilience and high temperature operability. These well-rounded properties make alumina a versatile and high-performance substrate material for electronics.
Leave a Reply