Types of DFM Tools
DFM tools can be broadly categorized into the following types:
- DFM Guidelines and Checklists
- DFM Software
- DFM Analysis Tools
- DFM Collaboration Platforms
Let’s dive into each category and discuss the specific tools available.
1. DFM Guidelines and Checklists
DFM guidelines and checklists are the most basic form of DFM tools. These are usually document-based resources that provide a set of best practices and design rules for specific manufacturing processes. They help designers ensure that their designs comply with the limitations and requirements of the chosen manufacturing method.
Some examples of DFM guidelines and checklists include:
- Injection Molding Design Guidelines
- Sheet Metal Fabrication Design Guidelines
- CNC Machining Design Guidelines
- PCB design guidelines
- Casting Design Guidelines
These guidelines cover aspects such as recommended wall thicknesses, draft angles, hole sizes, fillets, and radii specific to each manufacturing process. By following these guidelines, designers can avoid common manufacturing issues and ensure that their designs are optimized for production.
2. DFM Software
DFM software tools are more advanced solutions that integrate with CAD systems to provide real-time feedback and analysis of designs from a manufacturing perspective. These tools assess the manufacturability of designs and provide recommendations for improvement.
Some popular DFM software tools include:
- SolidWorks DFMXpress
- Autodesk Fusion 360
- PTC Creo DFM Advisor
- Siemens NX DFM
- CATIA DFM
These software tools typically work by analyzing the CAD model and identifying potential manufacturing issues such as undercuts, thin walls, small features, and complex geometries. They provide visual feedback by highlighting problematic areas and suggesting design modifications to improve manufacturability.
For example, SolidWorks DFMXpress is a built-in tool that checks designs against a set of predefined rules for injection molding, machining, and sheet metal fabrication. It generates a report with detailed feedback on the manufacturability of the design and provides recommendations for improvement.
3. DFM Analysis Tools
DFM analysis tools are specialized software solutions that focus on specific aspects of manufacturability, such as moldability analysis for injection molding or formability analysis for sheet metal forming. These tools provide in-depth analysis and simulation capabilities to predict and optimize the manufacturing process.
Some examples of DFM analysis tools include:
- Moldflow (for injection molding)
- AutoForm (for sheet metal forming)
- Deform (for forging and stamping)
- Magmasoft (for casting)
- Simufact (for welding and heat treatment)
These tools use advanced simulation algorithms to analyze the behavior of materials and predict potential manufacturing defects. They help engineers optimize process parameters, such as injection points, gate locations, and forming sequences, to improve product quality and reduce manufacturing costs.
For instance, Moldflow is a widely used tool for simulating the injection molding process. It analyzes the flow of plastic material inside the mold cavity, predicts filling patterns, and identifies potential issues such as short shots, weld lines, and warpage. By using Moldflow, designers can optimize the part geometry, gate locations, and processing conditions to ensure a successful injection molding process.
4. DFM Collaboration Platforms
DFM collaboration platforms are web-based tools that facilitate communication and collaboration between design and manufacturing teams. These platforms provide a centralized environment for sharing design data, manufacturing knowledge, and feedback.
Some examples of DFM collaboration platforms include:
- aPriori
- 3DX
- Xometry
- Fictiv
- Protolabs
These platforms often include features such as instant quoting, design for manufacturability analysis, and supplier sourcing. They enable designers to get real-time feedback on the manufacturability and cost of their designs from a network of manufacturing partners.
For example, aPriori is a cloud-based platform that provides real-time cost estimation and manufacturability analysis for various manufacturing processes, including machining, casting, and injection molding. It allows designers to collaborate with suppliers and get instant feedback on design changes and their impact on manufacturing costs.
Applications of DFM Tools in Product Development
DFM tools are used throughout the product development process to ensure that designs are optimized for manufacturing. Let’s look at some specific applications of DFM tools in each stage of product development.
1. Concept Design
During the concept design stage, DFM guidelines and checklists are used to ensure that initial design concepts are feasible from a manufacturing perspective. Designers refer to these guidelines to make informed decisions about material selection, part geometry, and assembly methods.
For example, when designing a plastic enclosure for an electronic device, designers would consult injection molding design guidelines to ensure that the part geometry is suitable for molding. They would consider factors such as wall thickness, draft angles, and undercuts to create a design that can be easily molded without defects.
2. Detailed Design
In the detailed design stage, DFM software tools are used to analyze and optimize the CAD model for manufacturability. These tools provide real-time feedback on potential manufacturing issues and suggest design improvements.
For instance, when designing a sheet metal bracket, designers would use a DFM software tool like SolidWorks DFMXpress to check the design against sheet metal fabrication guidelines. The tool would analyze the bend radii, flanges, and hole sizes to ensure that the part can be easily fabricated without issues.
3. Manufacturing Process Planning
DFM analysis tools are used in the manufacturing process planning stage to optimize the manufacturing process and predict potential issues. These tools simulate the behavior of materials and processes to identify optimal process parameters and minimize defects.
For example, when planning the injection molding process for a plastic part, engineers would use a tool like Moldflow to simulate the filling and cooling of the mold cavity. They would analyze the results to optimize gate locations, injection points, and cooling channels to ensure a consistent and efficient molding process.
4. Supplier Collaboration
DFM collaboration platforms are used to facilitate communication and collaboration between design and manufacturing teams, particularly when working with external suppliers. These platforms provide a centralized environment for sharing design data, manufacturing requirements, and feedback.
For instance, when outsourcing the production of a machined component, designers would use a platform like aPriori to collaborate with potential suppliers. They would upload the CAD model and specify the manufacturing requirements, such as tolerances and surface finishes. Suppliers would then provide instant quotes and feedback on the manufacturability of the design, allowing for iterative improvements and cost optimization.
Benefits of Using DFM Tools
Implementing DFM tools in the product development process offers several benefits:
-
Reduced Manufacturing Costs: DFM tools help identify and eliminate potential manufacturing issues early in the design process, reducing the need for costly design changes and rework later on. By optimizing designs for manufacturability, companies can minimize material waste, reduce cycle times, and improve production efficiency, leading to lower manufacturing costs.
-
Improved Product Quality: DFM tools ensure that designs are optimized for the chosen manufacturing process, reducing the risk of defects and quality issues. By simulating and analyzing the manufacturing process, engineers can identify potential problems and make necessary adjustments to improve product quality.
-
Faster Time-to-Market: By integrating DFM considerations into the design process from the early stages, companies can avoid delays caused by manufacturing issues discovered late in the development cycle. DFM tools enable concurrent engineering, where design and manufacturing teams work collaboratively to optimize designs for production, reducing iteration cycles and accelerating time-to-market.
-
Enhanced Collaboration: DFM collaboration platforms facilitate seamless communication and data sharing between design and manufacturing teams, even when working with external suppliers. This collaborative approach ensures that all stakeholders have access to the latest design information and can provide timely feedback, reducing miscommunication and errors.
-
Increased Design Flexibility: DFM tools provide designers with the knowledge and insights necessary to create designs that are optimized for manufacturing without sacrificing creativity and innovation. By understanding the capabilities and limitations of different manufacturing processes, designers can explore alternative design solutions that meet both functional and manufacturing requirements.
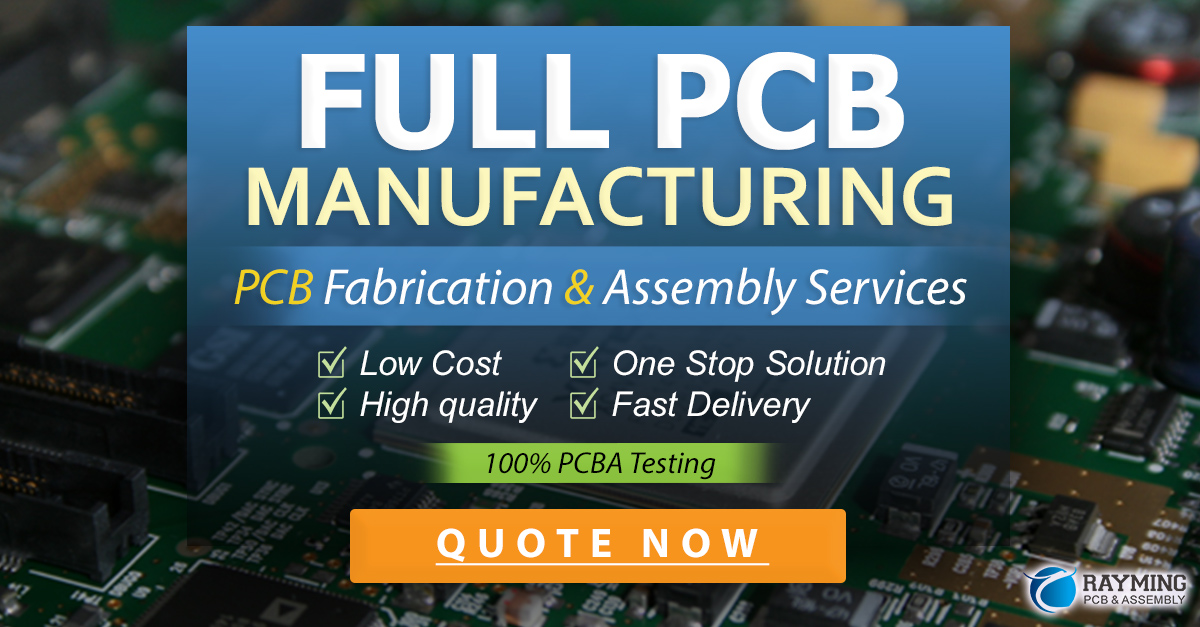
Challenges and Limitations of DFM Tools
While DFM tools offer significant benefits, there are also some challenges and limitations to consider:
-
Initial Investment: Implementing advanced DFM software and analysis tools can require a significant upfront investment in terms of licensing costs, hardware, and training. Small and medium-sized enterprises may find it challenging to justify the initial expenditure, especially if they have limited resources.
-
Learning Curve: Using DFM tools effectively requires a certain level of expertise and knowledge about manufacturing processes. Designers and engineers need to be trained on how to interpret and apply the feedback provided by these tools. There may be a learning curve associated with adopting new DFM tools and integrating them into existing design workflows.
-
Data Management: DFM tools generate a significant amount of data, including CAD models, simulation results, and manufacturing requirements. Managing and maintaining this data can be challenging, particularly when collaborating with multiple teams and suppliers. Effective data management strategies and version control systems are necessary to ensure data integrity and accessibility.
-
Limited Scope: While DFM tools cover a wide range of manufacturing processes, they may not encompass every possible scenario or constraint. Unique or highly specialized manufacturing processes may require additional expertise and custom analysis beyond the capabilities of standard DFM tools.
-
Overdependence: There is a risk of designers becoming overly reliant on DFM tools and neglecting their own manufacturing knowledge and experience. While these tools provide valuable insights, they should be used as a supplement to, rather than a replacement for, human expertise. Designers should still have a strong understanding of manufacturing processes and be able to make informed decisions based on their own knowledge.
Future Trends in DFM Tools
As manufacturing technologies continue to evolve, so do the DFM tools that support them. Here are some emerging trends in the development and application of DFM tools:
-
Integration with Additive Manufacturing: With the growing adoption of additive manufacturing (AM) technologies, DFM tools are being adapted to address the unique design considerations of AM processes. These tools help designers optimize part geometries for printability, minimize support structures, and predict potential issues such as warping and dimensional accuracy.
-
Artificial Intelligence and Machine Learning: AI and ML algorithms are being integrated into DFM tools to enhance their predictive capabilities and automate design optimization. These technologies can analyze vast amounts of manufacturing data to identify patterns, predict potential issues, and suggest design improvements based on historical performance.
-
Cloud-Based Collaboration: The trend towards cloud-based collaboration platforms is expected to continue, enabling seamless data sharing and communication between geographically dispersed teams. Cloud-based DFM tools allow for real-time collaboration, version control, and access to shared libraries of manufacturing knowledge.
-
Integration with Product Lifecycle Management (PLM): DFM tools are being integrated with PLM systems to provide a holistic view of the product development process. This integration allows for the seamless transfer of design data, manufacturing requirements, and feedback between different stages of the product lifecycle, from concept to production and beyond.
-
Expansion to New Manufacturing Processes: As new manufacturing technologies emerge, such as hybrid manufacturing and micro-manufacturing, DFM tools will need to adapt to address the specific design considerations of these processes. This expansion will require the development of new guidelines, simulation capabilities, and analysis tools tailored to these emerging technologies.
Frequently Asked Questions (FAQ)
-
What is Design for Manufacturing (DFM)?
Design for Manufacturing (DFM) is a methodology that involves designing products with manufacturing considerations in mind from the early stages of product development. It aims to optimize designs for efficient and cost-effective manufacturing by considering factors such as material selection, part geometry, tolerances, and assembly processes. -
Why is DFM important in product development?
DFM is important in product development because it helps ensure that designs are optimized for manufacturing, reducing the risk of costly design changes, production delays, and quality issues later in the development cycle. By integrating DFM considerations early on, companies can minimize manufacturing costs, improve product quality, and accelerate time-to-market. -
What are the different types of DFM tools available?
There are several types of DFM tools available, including: - DFM guidelines and checklists: Document-based resources that provide best practices and design rules for specific manufacturing processes.
- DFM software: CAD-integrated tools that provide real-time feedback and analysis of designs from a manufacturing perspective.
- DFM analysis tools: Specialized software solutions that focus on specific aspects of manufacturability, such as moldability analysis or formability analysis.
-
DFM collaboration platforms: Web-based tools that facilitate communication and collaboration between design and manufacturing teams.
-
How do DFM tools help reduce manufacturing costs?
DFM tools help reduce manufacturing costs by identifying and eliminating potential manufacturing issues early in the design process. By optimizing designs for manufacturability, these tools help minimize material waste, reduce cycle times, and improve production efficiency. This leads to lower manufacturing costs by reducing the need for costly design changes and rework later in the development cycle. -
What are some challenges and limitations of implementing DFM tools?
Some challenges and limitations of implementing DFM tools include: - Initial investment: Advanced DFM software and analysis tools can require a significant upfront investment in licensing, hardware, and training.
- Learning curve: Using DFM tools effectively requires expertise and knowledge about manufacturing processes, and there may be a learning curve associated with adopting new tools.
- Data management: Managing and maintaining the large amount of data generated by DFM tools can be challenging, particularly when collaborating with multiple teams and suppliers.
- Limited scope: While DFM tools cover a wide range of manufacturing processes, they may not encompass every possible scenario or constraint.
- Overdependence: There is a risk of designers becoming overly reliant on DFM tools and neglecting their own manufacturing knowledge and experience.
Conclusion
DFM tools play a crucial role in modern product development by helping designers and engineers create products that are optimized for manufacturing. From basic guidelines and checklists to advanced software solutions and collaboration platforms, there is a wide range of DFM tools available to support different aspects of the design and manufacturing process.
By implementing DFM tools, companies can reduce manufacturing costs, improve product quality, accelerate time-to-market, enhance collaboration, and increase design flexibility. However, it is important to consider the challenges and limitations associated with adopting these tools, such as the initial investment, learning curve, and data management requirements.
As manufacturing technologies continue to evolve, so will the DFM tools that support them. Emerging trends such as integration with additive manufacturing, AI and machine learning, cloud-based collaboration, and expansion to new manufacturing processes will shape the future of DFM tools.
Ultimately, the success of DFM implementation relies on a combination of the right tools, expertise, and a collaborative approach between design and manufacturing teams. By leveraging DFM tools effectively and continuously improving their application, companies can drive innovation, optimize their manufacturing processes, and deliver high-quality products to their customers.
Leave a Reply