What is PCB Thickness Tolerance?
PCB thickness tolerance refers to the acceptable variation in the thickness of a printed circuit board (PCB) from its specified nominal value. It is an essential aspect of PCB manufacturing, as it directly impacts the board’s mechanical and electrical properties, as well as its compatibility with other components in an Electronic Assembly.
The thickness of a PCB is determined by the combined thickness of the copper layers, prepreg layers, and core materials used in its construction. The nominal thickness is the intended thickness of the board, while the tolerance specifies the allowable deviation from this value.
Factors Affecting PCB Thickness Tolerance
Several factors can influence the thickness tolerance of a PCB:
-
Material properties: The type and quality of the materials used, such as the copper foil, prepreg, and core materials, can affect the consistency of the board’s thickness.
-
Manufacturing process: The lamination process, which involves pressing the layers together under high temperature and pressure, can introduce variations in thickness if not properly controlled.
-
Number of layers: As the number of layers in a PCB increases, maintaining a tight thickness tolerance becomes more challenging due to the increased number of materials and processing steps involved.
-
Board size: Larger PCBs may exhibit greater thickness variations compared to smaller ones, as it is more difficult to maintain consistent pressure and temperature across a larger surface area during lamination.
Industry Standards for PCB Thickness Tolerance
Several industry standards provide guidelines for PCB thickness tolerances, ensuring consistency and reliability across manufacturers and applications. Two widely recognized standards are IPC-6012 and IPC-600.
IPC-6012
IPC-6012, “Qualification and Performance Specification for Rigid Printed Boards,” is a standard that defines the requirements for rigid PCBs, including thickness tolerances. It specifies three classes of PCBs based on their intended application and performance requirements:
- Class 1: General Electronic Products
- Class 2: Dedicated Service Electronic Products
- Class 3: High Reliability Electronic Products
The thickness tolerance requirements for each class are as follows:
Class | Nominal Thickness (mm) | Tolerance (mm) |
---|---|---|
1 | ≤ 1.57 | ± 0.17 |
> 1.57 | ± 10% | |
2 | ≤ 2.36 | ± 0.14 |
> 2.36 | ± 6% | |
3 | ≤ 2.36 | ± 0.09 |
> 2.36 | ± 4% |
IPC-600
IPC-600, “Acceptability of Printed Boards,” is another standard that provides acceptance criteria for PCBs, including thickness requirements. It defines three classes of PCBs similar to IPC-6012, with the following thickness tolerances:
Class | Nominal Thickness (mm) | Tolerance (mm) |
---|---|---|
1 | All | ± 10% |
2 | All | ± 10% |
3 | All | ± 5% |
Impact of PCB Thickness Tolerance on Design and Performance
PCB thickness tolerance can have a significant impact on the design and performance of electronic assemblies. Some of the key areas affected include:
Mechanical Compatibility
The thickness of a PCB must be compatible with the components and connectors used in the assembly. If the board is too thick or too thin, it may not fit properly into the designated space or may cause issues with the attachment of components.
Impedance Control
In high-speed digital circuits, the thickness of the dielectric layers in a PCB plays a crucial role in determining the Characteristic Impedance of the signal traces. Variations in thickness can lead to impedance mismatches, which can cause signal integrity issues such as reflections, crosstalk, and attenuation.
Thermal Management
The thickness of a PCB can affect its ability to dissipate heat generated by the components mounted on it. Thicker boards generally have better thermal conductivity, allowing for more efficient heat transfer. However, if the board is too thick, it may not fit within the available space or may add unnecessary weight to the assembly.
Manufacturability
Maintaining a consistent PCB thickness is essential for reliable manufacturing processes. Thickness variations can lead to issues during lamination, drilling, and plating, resulting in defects such as delamination, poor hole quality, or inconsistent copper distribution.
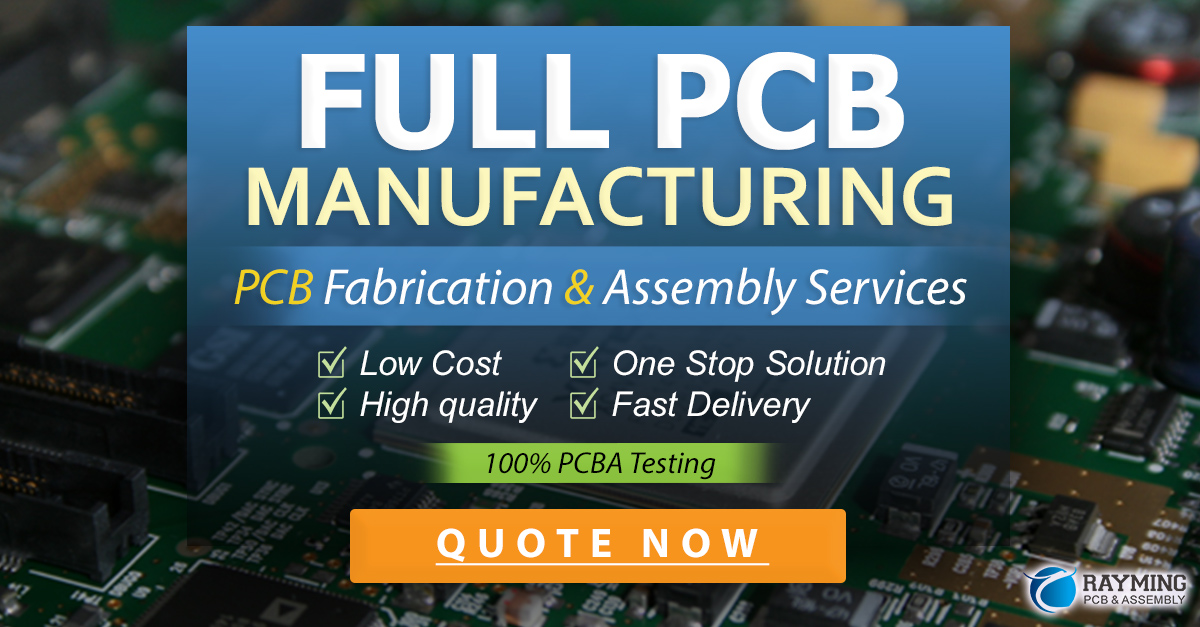
Designing for PCB Thickness Tolerance
To ensure the best possible performance and manufacturability of a PCB, designers should consider the following guidelines when specifying thickness and tolerance:
-
Choose appropriate materials: Select materials with consistent properties and work with reputable suppliers to minimize variations in thickness.
-
Consider the number of layers: Be aware that increasing the number of layers in a PCB can make it more challenging to maintain tight thickness tolerances. Design with this in mind and allow for appropriate tolerances based on the complexity of the board.
-
Specify realistic tolerances: While tighter tolerances may be desirable for certain applications, it is essential to specify tolerances that are achievable by the manufacturer. Overly stringent requirements can increase costs and lead to production delays.
-
Communicate with the manufacturer: Engage in open communication with the PCB manufacturer to ensure that they understand your requirements and can meet the specified tolerances. Discuss any potential issues or limitations early in the design process to avoid costly redesigns later.
Measuring and Verifying PCB Thickness
To ensure that a PCB meets the specified thickness tolerance, manufacturers employ various methods for measuring and verifying the board’s thickness. Some common techniques include:
Micrometer Measurement
A micrometer is a precise mechanical measuring tool that can be used to measure the thickness of a PCB at multiple points across its surface. This method is simple and reliable but requires manual operation and may not be suitable for high-volume production.
X-Ray Thickness Measurement
X-ray thickness gauges use X-ray technology to measure the thickness of a PCB non-destructively. This method is highly accurate and can measure the thickness of individual layers within the board. However, it requires specialized equipment and trained operators.
Laser Thickness Measurement
Laser thickness gauges use optical techniques to measure the thickness of a PCB. They offer high accuracy and can be integrated into automated production lines for in-line thickness monitoring. However, the accuracy of laser measurements can be affected by surface conditions and may require periodic calibration.
Frequently Asked Questions (FAQ)
- What is the difference between nominal thickness and thickness tolerance?
-
Nominal thickness is the intended or specified thickness of a PCB, while thickness tolerance is the allowable deviation from the nominal value.
-
How does the number of layers in a PCB affect its thickness tolerance?
-
As the number of layers in a PCB increases, maintaining a tight thickness tolerance becomes more challenging due to the increased number of materials and processing steps involved.
-
What are the most common industry standards for PCB thickness tolerance?
-
IPC-6012 and IPC-600 are two widely recognized industry standards that provide guidelines for PCB thickness tolerances.
-
How can PCB thickness tolerance impact the performance of an electronic assembly?
-
PCB thickness tolerance can affect the mechanical compatibility, impedance control, thermal management, and manufacturability of an electronic assembly.
-
What methods are used to measure and verify PCB thickness in manufacturing?
- Common methods for measuring and verifying PCB thickness include micrometer measurement, X-ray thickness measurement, and laser thickness measurement.
In conclusion, understanding and controlling PCB thickness tolerance is crucial for ensuring the quality, reliability, and performance of electronic assemblies. By following industry standards, designing with tolerance in mind, and working closely with PCB Manufacturers, designers can minimize the impact of thickness variations and achieve the best possible results for their projects.
Leave a Reply