Introduction to PCB Thickness
Printed Circuit Board (PCB) thickness is a crucial factor in the design and manufacturing of electronic devices. It plays a significant role in determining the mechanical strength, electrical performance, and thermal management of the board. In this comprehensive article, we will delve into the complex story of PCB thickness, exploring its various aspects, considerations, and best practices.
Understanding PCB Thickness Measurements
PCB thickness is typically measured in mils (thousandths of an inch) or millimeters (mm). The most common PCB thicknesses range from 0.8mm to 1.6mm, with 1.6mm being the standard thickness for many applications. However, the choice of PCB thickness depends on several factors, including the specific requirements of the project, the components used, and the manufacturing constraints.
Common PCB Thickness Measurements
PCB Thickness (mils) | PCB Thickness (mm) |
---|---|
31.5 | 0.8 |
39.4 | 1.0 |
47.2 | 1.2 |
62.9 | 1.6 |
Factors Influencing PCB Thickness Selection
When selecting the appropriATE PCB thickness for your project, there are several key factors to consider:
1. Mechanical Strength and Durability
The thickness of a PCB directly impacts its mechanical strength and durability. Thicker boards are generally more robust and can withstand greater physical stress, such as vibrations, shocks, and handling. If your application involves harsh environments or requires high reliability, opting for a thicker PCB is often recommended.
2. Electrical Performance
PCB thickness also influences the electrical performance of the board. Thinner boards have shorter signal paths, which can be advantageous for high-speed designs and applications requiring low signal distortion. However, thinner boards also have higher impedance and may be more susceptible to signal integrity issues, such as crosstalk and electromagnetic interference (EMI).
3. Thermal Management
The thickness of a PCB affects its thermal management capabilities. Thicker boards have better heat dissipation properties, as they provide more surface area for heat transfer. This is particularly important for high-power applications or designs with components that generate significant heat. Adequate thermal management helps ensure the reliability and longevity of the electronic components.
4. Manufacturing Constraints
PCB thickness selection is also influenced by manufacturing constraints. Thinner boards may pose challenges during the fabrication process, especially when it comes to drilling holes and maintaining the required tolerances. Thicker boards, on the other hand, may require specialized equipment and longer processing times, which can impact production costs and lead times.
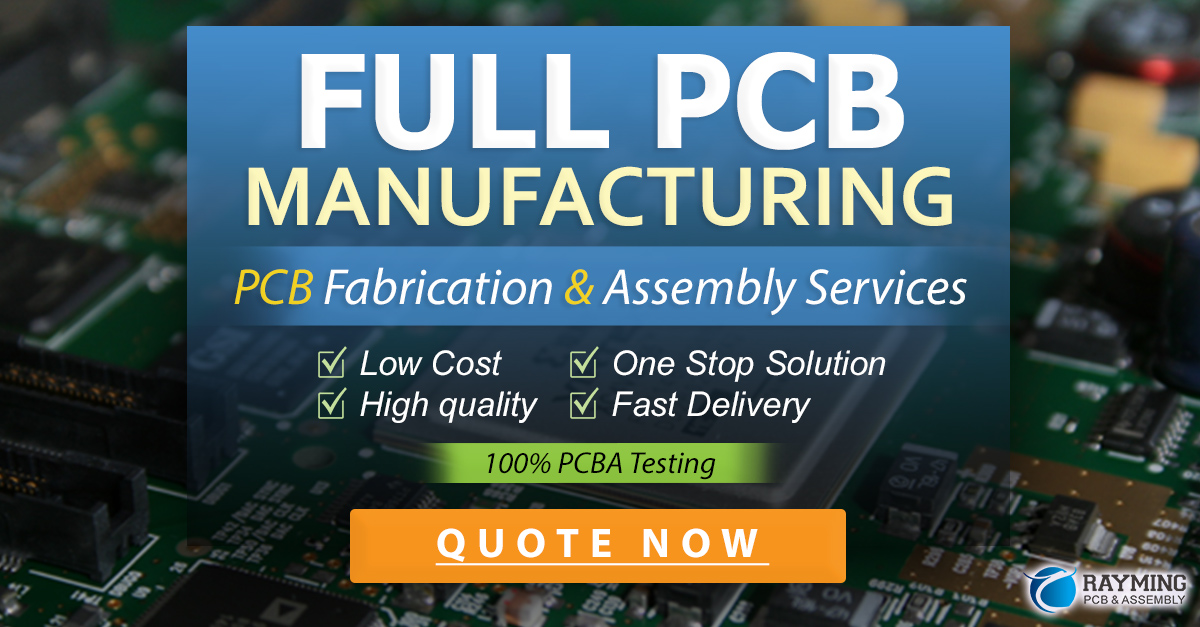
PCB Thickness and Layer Count
The number of layers in a PCB is closely related to its thickness. As the layer count increases, the overall thickness of the board also increases. The relationship between PCB thickness and layer count is governed by the thickness of the individual layers and the number of layers stacked together.
Standard PCB Layer Thicknesses
Layer Type | Thickness (mils) |
---|---|
Copper | 1.4 – 2.8 |
Prepreg | 3.6 – 7.2 |
Core | 4.7 – 9.4 |
Solder Mask | 0.8 – 1.6 |
Silkscreen | 0.4 – 0.8 |
Calculating PCB Thickness based on Layer Count
To calculate the approximate thickness of a PCB based on the layer count, you can use the following formula:
PCB Thickness = (Number of Layers – 1) × (Prepreg Thickness + Copper Thickness) + Core Thickness + Solder Mask Thickness + Silkscreen Thickness
For example, a 4-layer PCB with standard layer thicknesses would have an approximate thickness of:
PCB Thickness = (4 – 1) × (5.4 + 1.4) + 6.3 + 1.2 + 0.6 = 28.5 mils (0.72 mm)
PCB Thickness and Impedance Control
Impedance control is a critical aspect of PCB design, particularly in high-speed and high-frequency applications. PCB thickness plays a significant role in achieving the desired impedance characteristics of the board.
Factors Affecting Impedance
The impedance of a PCB Trace is influenced by several factors, including:
- Trace width and thickness
- Dielectric constant of the PCB material
- Thickness of the dielectric layer
- Proximity to ground or power planes
Impedance Calculation
To calculate the impedance of a PCB trace, you can use the following formula:
Impedance = 87 / √(εr) × ln(5.98 × H / (0.8 × W + T))
Where:
– εr is the dielectric constant of the PCB material
– H is the thickness of the dielectric layer
– W is the width of the trace
– T is the thickness of the trace
Impedance Control Techniques
To achieve the desired impedance in a PCB design, designers employ various techniques, such as:
- Adjusting the trace width and thickness
- Selecting appropriate dielectric materials
- Controlling the thickness of the dielectric layers
- Using ground planes and power planes for shielding and reference
Best Practices for PCB Thickness Selection
When selecting the appropriate PCB thickness for your project, consider the following best practices:
-
Understand the specific requirements and constraints of your application, including mechanical, electrical, and thermal considerations.
-
Consult with your PCB manufacturer early in the design process to discuss the feasibility and cost implications of different thickness options.
-
Consider the layer count and impedance control requirements when determining the PCB thickness.
-
Use standard PCB thicknesses whenever possible to minimize manufacturing complexities and costs.
-
Conduct thorough testing and validation to ensure the selected PCB thickness meets the desired performance and reliability standards.
Frequently Asked Questions (FAQ)
1. What is the standard PCB thickness for most applications?
The standard PCB thickness for most applications is 1.6mm (62.9 mils). This thickness provides a good balance between mechanical strength, electrical performance, and manufacturing feasibility.
2. Can I use a thinner PCB to save space in my design?
Yes, you can use a thinner PCB to save space in your design. However, keep in mind that thinner boards may have reduced mechanical strength and may be more susceptible to signal integrity issues. It’s essential to carefully consider the trade-offs and consult with your PCB manufacturer.
3. How does PCB thickness affect the cost of manufacturing?
PCB thickness can impact the cost of manufacturing in several ways. Thinner boards may require specialized equipment and handling, which can increase production costs. Thicker boards may require longer processing times and more materials, also affecting the overall cost. It’s best to discuss the cost implications with your PCB manufacturer.
4. What is the relationship between PCB thickness and impedance control?
PCB thickness is one of the factors that influence impedance control. The thickness of the dielectric layers and the proximity of traces to ground or power planes can affect the impedance characteristics of the board. Designers must carefully consider PCB thickness when achieving the desired impedance for high-speed and high-frequency applications.
5. How do I select the appropriate PCB thickness for my project?
To select the appropriate PCB thickness for your project, consider the following factors:
– Mechanical strength and durability requirements
– Electrical performance and signal integrity needs
– Thermal management considerations
– Manufacturing constraints and cost implications
– Layer count and impedance control requirements
Consult with your PCB manufacturer and discuss your specific project requirements to determine the optimal PCB thickness for your application.
Conclusion
PCB thickness is a complex and multifaceted topic that requires careful consideration in the design and manufacturing of electronic devices. Understanding the factors influencing PCB thickness selection, such as mechanical strength, electrical performance, thermal management, and manufacturing constraints, is crucial for making informed decisions.
By exploring the relationship between PCB thickness and layer count, as well as the impact of thickness on impedance control, designers can optimize their PCB designs for specific applications. Following best practices and collaborating with PCB Manufacturers throughout the design process helps ensure the successful realization of reliable and high-performance electronic products.
As technology continues to advance and the demand for compact, high-density electronics grows, the story of PCB thickness remains an essential chapter in the ever-evolving world of electronic design and manufacturing.
Leave a Reply