Ceramic PCBs leave other types behind due to their remarkable features. From thermal conductivity to a durable nature, these PCBs are outstanding in their performance. Ceramic PCBs are also useful when it comes to relying on them instead of other types because these can serve better than them.
There is no doubt that multilayer ceramic PCBs include different industrial raw materials for their production. These materials come together that render different attributes to these PCBs on the whole. Another good part of these PCBs is that they are eco-friendly, meaning they do not produce harmful toxic emissions into the environment during functioning.
We are going to decipher these PCBs for you in this post for better understanding. Let’s get started!
Multilayer Ceramic PCB
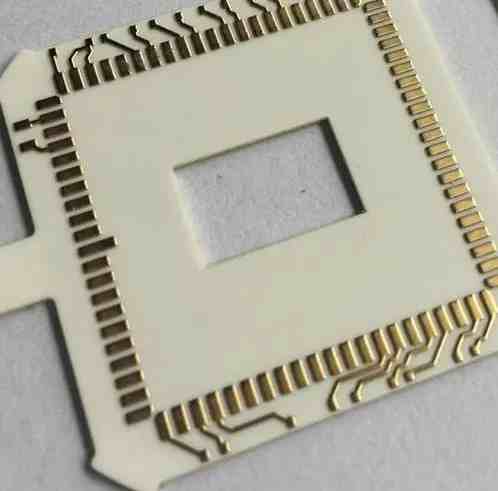
There is nothing hard to understand about multilayer ceramic PCBs. These are ceramic PCBs with more than one layer. Now the addition of these layers is also a contributing factor that sets them apart from the rest. We use different types of special materials like beryllium oxide, aluminum nitride, and alumina to make it seamlessly conduct heat. The heat due to these materials does not interact with hotspots of PCBs, and therefore, the damage is next to impossible. Organic binders and ceramic powder come together to develop these PCBs if we talk about intricacies. Special LAM technology is reliable for the development of such PCBs, and many producers are using it for this purpose today.
Methods of Fabrication for Multilayer Ceramic PCB
· Thick Film Ceramic Board
It is important to heat these PCBs to a fixed temperature and combine the gold and dielectric paste on the ceramic layer. We mostly use copper and gold because these are much beneficial in the fabrication process. Nitrogen is also important because it reduces the chances of oxidation which can negatively impact the quality and sustainability of ceramic PCBs.
· LTCC PCB
These PCBs generally have good traces because nothing can compare to gold for impressive thermal conductivity. An optimum temperature of 900 degrees Celsius is enough for heating LTCC PCBs. The process also involves the combustion of glass, non-glass particles, and crystals that we call “co-firing.”
· PCB HTCC
PCB HTCC is almost similar to LTCC PCBs, but there are some differences. We can use plasticizers, adhesives, aluminum oxides, and lubricants for these PCBs. These contain traces of tungsten and molybdenum as per their nature of work. These traces are heat resistant because we use these PCBs for heat-sensitive electronics. These are smaller in size as compared to others and perform exceptionally well for the devices.
Challenges in Manufacturing of Multilayer Ceramic PCB
· Material & Compatibility
It is important to know that the development of multilayer ceramic PCBs is not an easy job. Due to this reason, the producers need to be aware of the materials suitable to use for the production of these PCBs for effective performance. So we at Rogers Co make sure to rely on such materials that improve the performance of ceramic PCBs for the users and their electronics.
It is important to note that different materials have different features, and due to his fact, their applications are variable. We cannot use a single PCB for every application. When it comes to multilayer PCBs, it is obvious that the incorporation of these raw materials into each layer enhances the overall features of these PCBs. It is also beneficial for the strong bonding and impeccable lamination of the PCBs. Besides, they become more resilient to working under pressure. Sometimes, challenges occur in the production of these PCBs. The common are:
- Developing strong bonds between ceramic layers.
- Maintaining the dimensional sustainability of the PCBs.
- Fluctuations in the thermal coefficient.
- Resisting the thermal coefficient from ruining the reliability.
- More chances of delamination and warpage in the middle of thermal cycling.
· Precision
This is obvious that multilayer PCBs are critical, and therefore, these demand precision during production. Undivided attention to these PCBs is important. Other than this, these cannot perform accurately under unfavorable conditions.
Several complex and intricate parts are present in them. Due to this reason, without precision techniques, we cannot refine their performance for longer terms. When we need to go for drilling and milling, it is important to handle these with care. Or else reckless drilling can compromise the boards on the whole.
· Metallization
Sometimes issues during metallization can also arise. Therefore PCB manufacturers also need to take care of this step of production. We cannot ensure fine electrical performance without combing the materials with the ceramic base. This is a critical phase, and therefore, Rogers Co uses some industrial-grade materials and follows some viable procedures to make this happen seamlessly. We execute the process of metallization under stringent supervision to avoid all kinds of complications.
Benefits of Multilayer Ceramic PCB
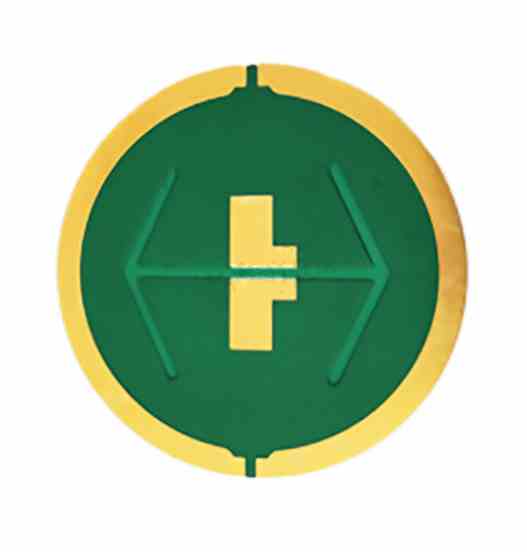
· Thermal Conductivity
You already know that ceramic PCBs are exceptional in terms of thermal conductivity. The range of thermal conductivity for these PCBs is different when we use different materials. Don’t be surprised to know this even FR4 PCBs cannot compare their range of thermal conductivity. The reason lies in their feature of heat dissipation which is eventually good for protection against heat.
· Low (CTE)
Such a strong thermal expansion coefficient comes in handy when we incorporate PCBs in heat-sensitive devices. Due to this reason, these can endure extremely hot temperatures quite easily. All of this does not even impact these PCBs in terms of their performance as well.
· Superior Thermal Insulation
Ceramics are also good at insulating, and due to this reason, we can use them for such applications that need insulation for heat all the time. Plus, this feature protects the circuit itself from undergoing sudden heat damage as well.
· Inorganic
The inclusion of inorganic materials in these PCBs is also interesting. These inorganic substances are highly important for their chemical resistance and protect the structure of the PCBs from damage as well.
· High Frequency
Such PCBs are also good at thermal stability, and therefore, high-frequency applications can make much use of them. The best part about this attribute is that it does not complicate the functioning of devices; instead, it enhances the efficiency of such devices for seamless data transmission and data transfers.
· Cost Effectiveness
It is hard to get affordable ceramic PCBs, but their features are worth their investment. However, you can still find a huge range of varieties among these PCBs and find them in different price ranges in multiple markets.
Drawbacks of Multilayer Ceramic PCB
· Cost
One downside of these PCBs is that they are expensive. Therefore many users are reluctant to buy these on the whole. The reason behind their high price is the inclusion of several complex and rare components, ceramics, and other elements that increase their price greatly.
· Handling
We cannot handle ceramic PCBs recklessly. It is because these are fragile and sensitive at the same time. Negligence towards them can break the boards, compromise the components, and can damage the ceramic base as well.
· Availability
Keep in mind that these boards are not always available. Users have to struggle a lot to get their hands on such PCBs. Producers cannot always meet the market demand, and therefore, they always need to keep up with the market through consistent production of ceramic PCBs.
Conclusion
A multilayer ceramic PCB can benefit electronic devices in different ways. Their features are attractive for the users for the well-being of their electronics. With time, ceramic PCBs can prove to be more efficient for the fine performance of future electronics as well.
Leave a Reply