What is PCB Impedance?
PCB impedance refers to the opposition to the flow of electrical current in a printed circuit board (PCB). It is a critical factor in high-speed digital designs, as it affects signal integrity, timing, and overall system performance. Proper impedance control ensures that signals propagate through the PCB with minimal distortion, reflections, and crosstalk.
Factors Affecting PCB Impedance
Several factors influence PCB impedance, including:
- Trace geometry (width, thickness, and spacing)
- Dielectric material properties (dielectric constant and loss tangent)
- Copper thickness and roughness
- Frequency of the signal
- Proximity to other traces and planes
Why is PCB Impedance Control Important?
Impedance control is crucial in high-speed digital designs for several reasons:
Signal Integrity
Proper impedance control minimizes signal reflections and distortions, ensuring that the signal reaches its destination with the intended shape and timing. Reflections occur when there is an impedance mismatch between the signal source, transmission line (PCB trace), and load. These reflections can cause signal distortion, overshoot, undershoot, and ringing, leading to data corruption and system malfunctions.
Timing
Impedance control helps maintain consistent signal propagation delays across the PCB. This is particularly important in synchronous designs, where signals must arrive at their destinations within a specific time window. Inconsistent delays can cause setup and hold time violations, resulting in data errors and system failures.
Electromagnetic Compatibility (EMC)
Proper impedance control reduces electromagnetic interference (EMI) and crosstalk between adjacent traces. By minimizing signal reflections and distortions, impedance control helps contain electromagnetic emissions and prevents interference with other devices or systems.
Types of PCB Impedance
There are two main types of PCB impedance:
Characteristic Impedance
Characteristic impedance is the impedance of a transmission line (PCB trace) when it is infinitely long or perfectly terminated. It depends on the trace geometry, dielectric material properties, and frequency. The most common characteristic impedances in digital designs are 50 ohms for single-ended signals and 100 ohms for differential pairs.
Differential Impedance
Differential impedance is the impedance between two traces in a differential pair. It is determined by the geometry of the traces, their spacing, and the dielectric material properties. Differential signaling is often used in high-speed designs to improve signal integrity and reduce electromagnetic interference.
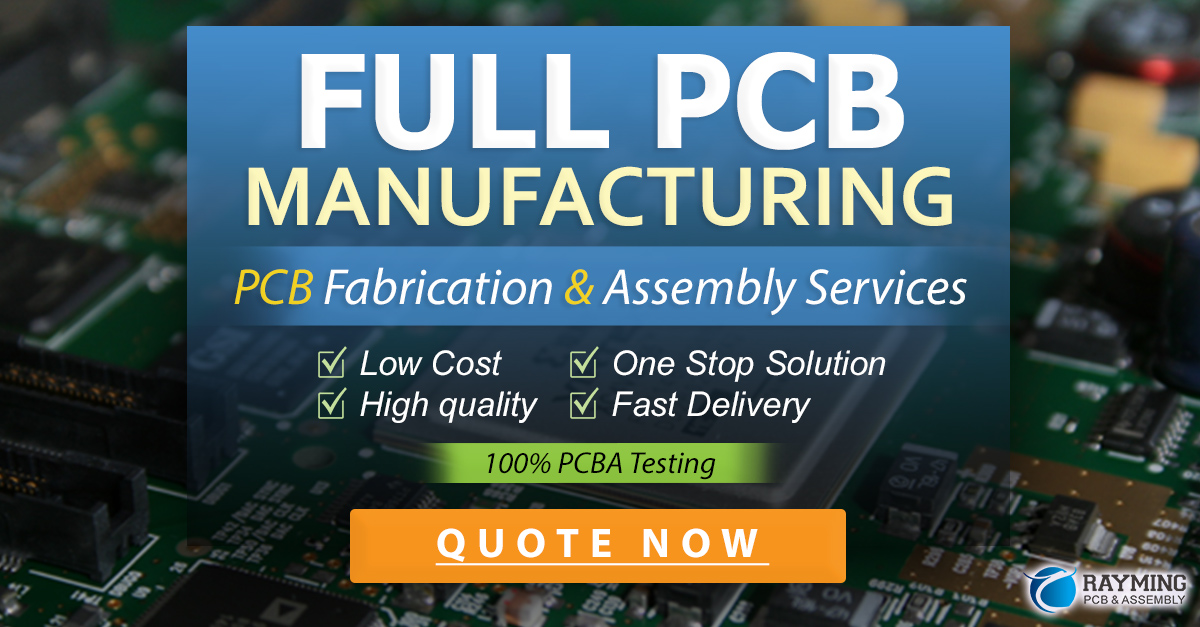
Designing for PCB Impedance Control
To achieve proper impedance control in PCB designs, consider the following guidelines:
Material Selection
Choose PCB materials with consistent dielectric properties, such as FR-4 or Rogers laminates. The dielectric constant (Dk) and loss tangent (Df) of the material should be well-defined and stable across the operating frequency range.
Stackup Design
Design the PCB stackup to provide consistent impedance across signal layers. This involves selecting the appropriate dielectric thickness, copper weight, and layer arrangement. Use dedicated signal layers and ground planes to create controlled impedance environments.
Trace Geometry
Calculate the required trace width and spacing to achieve the target impedance. Use impedance calculators or simulation tools to determine the optimal trace geometry based on the dielectric material properties and desired impedance.
Terminations
Use proper termination techniques to match the impedance of the signal source and load to the characteristic impedance of the transmission line. Common termination methods include:
- Series termination
- Parallel termination
- AC termination
- Differential termination
Routing Considerations
Follow best practices for high-speed routing, such as:
- Route signals on dedicated layers
- Avoid sharp bends and discontinuities
- Maintain consistent trace width and spacing
- Use ground planes for shielding and return paths
- Minimize the use of vias
- Route differential pairs with controlled spacing and symmetry
PCB Impedance Testing and Validation
After designing and manufacturing the PCB, it is essential to test and validate the impedance control. Common methods for impedance testing include:
Time Domain Reflectometry (TDR)
TDR measures the impedance of a transmission line by sending a fast-rising pulse and analyzing the reflections. It provides a graphical representation of the impedance profile along the trace, allowing designers to identify impedance discontinuities and mismatches.
Frequency Domain Reflectometry (FDR)
FDR measures the impedance of a transmission line by sweeping a range of frequencies and analyzing the reflections. It provides information about the impedance characteristics across the frequency spectrum.
Vector Network Analyzer (VNA)
A VNA measures the scattering parameters (S-parameters) of a transmission line, providing information about the impedance, insertion loss, and return loss. It is a more comprehensive method for characterizing the high-frequency behavior of PCB traces.
FAQ
1. What is the difference between characteristic impedance and differential impedance?
Characteristic impedance is the impedance of a single transmission line when it is infinitely long or perfectly terminated. Differential impedance is the impedance between two traces in a differential pair.
2. How do I calculate the required trace width for a given impedance?
To calculate the required trace width, you need to know the dielectric material properties (Dk and Df), the desired impedance, and the trace thickness. Use impedance calculators or simulation tools to determine the optimal trace width based on these parameters.
3. What is the purpose of termination in impedance control?
Termination is used to match the impedance of the signal source and load to the characteristic impedance of the transmission line. It minimizes signal reflections and ensures proper signal integrity.
4. How does the dielectric material affect PCB impedance?
The dielectric constant (Dk) and loss tangent (Df) of the PCB material directly influence the impedance of the traces. Materials with higher Dk values result in lower impedance for a given trace geometry. The loss tangent affects the signal attenuation and dispersion.
5. What are the best practices for routing high-speed signals on a PCB?
Best practices for high-speed routing include using dedicated signal layers, maintaining consistent trace width and spacing, minimizing sharp bends and discontinuities, using ground planes for shielding and return paths, minimizing the use of vias, and routing differential pairs with controlled spacing and symmetry.
Parameter | Effect on Impedance |
---|---|
Trace Width | Wider traces have lower impedance |
Dielectric Thickness | Thicker dielectrics increase impedance |
Dielectric Constant (Dk) | Higher Dk values decrease impedance |
Copper Thickness | Thicker copper decreases impedance |
Trace Spacing | Larger spacing increases impedance |
In conclusion, PCB impedance control is a critical aspect of high-speed digital design. By understanding the factors affecting impedance, designing for consistent impedance, and validating the impedance through testing, designers can ensure signal integrity, timing accuracy, and electromagnetic compatibility in their PCB designs.
Leave a Reply