Types of PCB Raw Materials
Substrate Materials
The substrate is the foundation of a PCB, providing a stable base for the copper traces and other components. The most common substrate materials used in PCB production are:
FR-4
FR-4 is a glass-reinforced epoxy laminate, widely used in the electronics industry due to its excellent mechanical, electrical, and thermal properties. It is composed of woven fiberglass cloth impregnated with an epoxy resin binder. FR-4 is known for its high strength, good insulation properties, and resistance to moisture and chemicals.
CEM-1 and CEM-3
CEM (Composite Epoxy Material) is a cost-effective alternative to FR-4. CEM-1 consists of a layer of woven fiberglass cloth combined with a layer of non-woven fiberglass mat, while CEM-3 uses only non-woven fiberglass mat. These materials offer lower cost and improved machinability compared to FR-4, but with slightly reduced mechanical and thermal properties.
Polyimide
Polyimide is a high-performance substrate material known for its exceptional thermal stability and chemical resistance. It is often used in applications that require operation at high temperatures or exposure to harsh environments, such as aerospace and military electronics.
Aluminum
Aluminum PCBs, also known as metal core PCBs (MCPCBs), use an aluminum substrate to provide excellent thermal dissipation. They are commonly used in high-power applications, such as LED lighting and power electronics, where efficient heat transfer is crucial.
Copper Foil
Copper foil is the conductive material used to create the traces, pads, and planes on a PCB. It is typically laminated onto the substrate using heat and pressure. The thickness of the copper foil is measured in ounces per square foot (oz/ft²), with common thicknesses ranging from 0.5 oz/ft² to 4 oz/ft².
Copper foil is available in two main types:
-
Electrodeposited (ED) copper: ED copper is formed by electroplating copper onto a rotating drum, resulting in a smooth, shiny surface. It is the most commonly used type of copper foil in PCB production.
-
Rolled annealed (RA) copper: RA copper is produced by rolling and annealing high-purity copper. It has a matte surface and offers better mechanical properties and thermal stability compared to ED copper.
Solder Mask
Solder mask is a protective coating applied to the copper traces on a PCB to prevent short circuits and improve the solderability of the exposed pads. It is typically green in color but can also be found in other colors such as blue, red, and black. Solder mask is usually made from a photoimageable epoxy or acrylic material that is applied as a liquid and then cured using UV light.
Silkscreen
Silkscreen is a layer of ink printed on the surface of a PCB to provide information such as component designators, polarity markers, and logos. It is typically white but can also be found in other colors. Silkscreen is usually made from a UV-curable ink that is applied using a screen printing process.
PCB Fabrication Process
The PCB fabrication process involves several steps, each utilizing different raw materials and processes. A brief overview of the main steps is as follows:
-
Substrate preparation: The substrate material is cut to size, and any necessary holes are drilled.
-
Copper lamination: Copper foil is laminated onto the substrate using heat and pressure.
-
Patterning: The desired circuit pattern is transferred onto the copper layer using a photolithographic process.
-
Etching: Unwanted copper is removed using a chemical etching process, leaving only the desired traces and pads.
-
Solder mask application: Solder mask is applied to the PCB and cured using UV light.
-
Silkscreen printing: The silkscreen layer is printed onto the PCB using a screen printing process.
-
Surface finish: A surface finish, such as HASL (Hot Air Solder Leveling) or ENIG (Electroless Nickel Immersion Gold), is applied to the exposed copper to improve solderability and protect against oxidation.
Properties of PCB Raw Materials
When selecting PCB raw materials, several key properties must be considered to ensure the finished product meets the desired performance and reliability requirements. These properties include:
Thermal Properties
- Glass Transition Temperature (Tg): The temperature at which the substrate material transitions from a rigid, glassy state to a softer, rubbery state. A higher Tg indicates better thermal stability.
- Thermal Conductivity: The ability of a material to conduct heat. Higher thermal conductivity allows for better heat dissipation, which is important for high-power applications.
- Coefficient of Thermal Expansion (CTE): The degree to which a material expands or contracts with changes in temperature. A lower CTE is desirable to minimize stress on components and solder joints.
Electrical Properties
- Dielectric Constant (Dk): The ability of a material to store electrical energy. A lower Dk is preferred for high-frequency applications to minimize signal loss and distortion.
- Dissipation Factor (Df): The measure of a material’s ability to dissipate electrical energy as heat. A lower Df is desirable to minimize signal loss.
- Insulation Resistance: The resistance of a material to the flow of electrical current. Higher insulation resistance is necessary to prevent short circuits and leakage currents.
Mechanical Properties
- Tensile Strength: The maximum stress a material can withstand before breaking. Higher tensile strength is important for maintaining the integrity of the PCB during handling and use.
- Flexural Strength: The ability of a material to resist bending. Higher flexural strength is necessary for applications where the PCB may be subjected to physical stress.
- Elongation: The degree to which a material can stretch before breaking. Higher elongation allows for better flexibility and resistance to cracking.
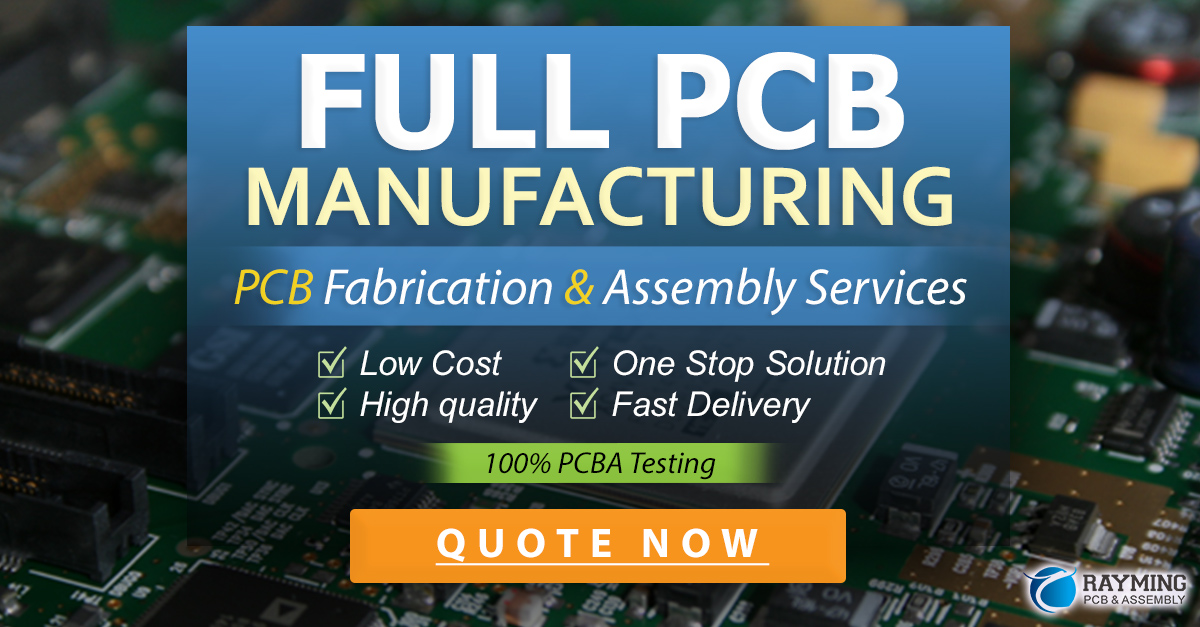
Applications of PCB Raw Materials
The selection of PCB raw materials depends on the specific requirements of the application. Some common applications and their typical material choices include:
- Consumer Electronics: FR-4 substrate, 1 oz/ft² copper, green solder mask, white silkscreen
- Automotive Electronics: FR-4 or polyimide substrate, 1-2 oz/ft² copper, green or black solder mask, white silkscreen
- High-Frequency Applications: Low-Dk substrates (e.g., Rogers materials), 0.5-1 oz/ft² copper, green solder mask, white silkscreen
- High-Power Applications: Aluminum or ceramic substrates, 2-4 oz/ft² copper, green or black solder mask, white silkscreen
- Flexible Electronics: Polyimide substrate, 0.5-1 oz/ft² copper, coverlay or soldermask, silkscreen optional
Frequently Asked Questions (FAQ)
- What is the most common substrate material used in PCB production?
-
FR-4, a glass-reinforced epoxy laminate, is the most widely used substrate material in the electronics industry due to its excellent balance of mechanical, electrical, and thermal properties.
-
What is the purpose of solder mask on a PCB?
-
Solder mask is a protective coating applied to the copper traces on a PCB to prevent short circuits and improve the solderability of the exposed pads. It also provides insulation and protection against environmental factors.
-
How is the thickness of copper foil measured in PCBs?
-
The thickness of copper foil in PCBs is measured in ounces per square foot (oz/ft²). Common thicknesses range from 0.5 oz/ft² to 4 oz/ft², with 1 oz/ft² being the most widely used.
-
What are the advantages of using aluminum substrates in PCBs?
-
Aluminum substrates, also known as metal core PCBs (MCPCBs), offer excellent thermal dissipation properties. They are commonly used in high-power applications, such as LED lighting and power electronics, where efficient heat transfer is crucial for maintaining the performance and reliability of the components.
-
What factors should be considered when selecting PCB raw materials for a specific application?
- When selecting PCB raw materials, several factors should be considered, including the desired electrical, thermal, and mechanical properties, the operating environment, the cost, and the manufacturability. The specific requirements of the application will dictate the most suitable combination of substrate material, copper thickness, solder mask, and surface finish.
Conclusion
Understanding the basic knowledge of PCB raw materials is essential for anyone involved in the design, manufacture, or use of electronic devices. By familiarizing yourself with the various substrate materials, copper foils, solder masks, and silkscreens used in PCB production, as well as their properties and applications, you can make informed decisions when selecting materials for your specific needs. This knowledge will help you optimize the performance, reliability, and cost-effectiveness of your PCB designs.
Leave a Reply