What is Manual Assembly?
Manual assembly is a process where human workers use their hands, sometimes with the aid of simple tools, to put together components or sub-assemblies to create a final product. This method has been the traditional approach to assembly for centuries and is still widely used in various industries today.
Advantages of Manual Assembly
-
Flexibility: Manual assembly allows for greater flexibility in terms of product design changes and customization. Human workers can easily adapt to modifications in the assembly process, making it suitable for low-volume or high-mix production.
-
Lower initial investment: Setting up a manual assembly line requires less capital investment compared to an automated system. It does not involve expensive machinery, robots, or complex programming.
-
Skilled workforce: Manual assembly relies on the skills and expertise of human workers. This can be advantageous in industries where craftsmanship and attention to detail are highly valued, such as in the production of luxury goods or artisanal products.
Disadvantages of Manual Assembly
-
Lower productivity: Manual assembly is generally slower than automated assembly, as human workers have physical limitations and are prone to fatigue. This can result in lower output rates and longer production times.
-
Inconsistent quality: The quality of manually assembled products can vary depending on the skill level and consistency of the workers. Human error is more likely to occur, leading to potential quality issues and higher rejection rates.
-
Higher labor costs: Manual assembly is labor-intensive, requiring a larger workforce. This can result in higher labor costs, especially in regions with high wage rates or labor shortages.
What is Automated Assembly?
Automated assembly is a process where machines, robots, and other automated equipment are used to assemble components or sub-assemblies into a final product. This method has gained popularity in recent decades due to advancements in technology and the need for faster, more efficient production.
Advantages of Automated Assembly
-
Higher productivity: Automated assembly systems can operate at much higher speeds and with greater consistency than human workers. They can run continuously, with minimal downtime, resulting in higher output rates and shorter production times.
-
Consistent quality: Automated systems can maintain a high level of precision and repeatability, ensuring consistent product quality. This reduces the likelihood of human error and results in lower rejection rates.
-
Reduced labor costs: While the initial investment in automated systems may be higher, they can significantly reduce labor costs in the long run. Fewer workers are required to operate and maintain the equipment, leading to lower overall labor expenses.
Disadvantages of Automated Assembly
-
High initial investment: Setting up an automated assembly line requires a significant capital investment in machinery, robots, and programming. This can be a barrier for smaller companies or those with limited financial resources.
-
Limited flexibility: Automated systems are designed for specific tasks and products. Making changes to the product design or assembly process can be costly and time-consuming, as it may require reprogramming or retooling the equipment.
-
Skilled maintenance: Automated systems require skilled technicians for maintenance, troubleshooting, and repairs. This can lead to additional training costs and the need for specialized support staff.
Factors to Consider When Choosing Between Manual and Automated Assembly
When deciding between manual and automated assembly for your manufacturing needs, consider the following factors:
-
Production volume: Automated assembly is generally more suitable for high-volume production, where the cost of automation can be justified by the increased output. Manual assembly may be more cost-effective for low-volume or custom production.
-
Product complexity: Complex products with many components or intricate assembly steps may be better suited for automated assembly, as machines can handle these tasks with greater precision and consistency. Simpler products or those requiring more flexibility may be better suited for manual assembly.
-
Labor costs: Consider the labor costs in your region and the availability of skilled workers. In areas with high wage rates or labor shortages, automated assembly may be more economically viable.
-
Capital investment: Evaluate your financial resources and the long-term return on investment. While automated assembly requires a higher initial investment, it can lead to cost savings in the long run through increased productivity and reduced labor costs.
-
Flexibility and customization: If your products require frequent design changes or customization, manual assembly may be more suitable due to its greater flexibility. Automated systems are better suited for stable, high-volume production.
-
Quality requirements: Consider the quality standards and tolerances required for your products. Automated assembly can provide more consistent quality, especially for products with tight tolerances or critical dimensions.
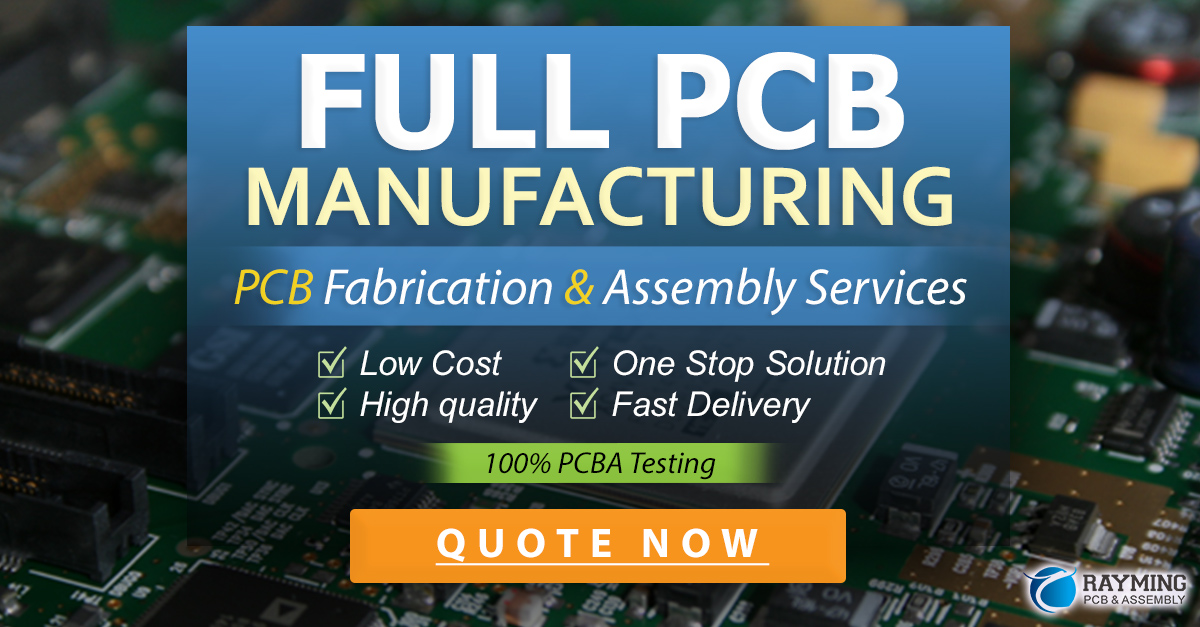
Applications of Manual and Automated Assembly
Both manual and automated assembly have their place in various industries and applications. Here are some examples:
Industry | Manual Assembly Applications | Automated Assembly Applications |
---|---|---|
Automotive | Final assembly of complex components, customization | High-volume production of standard parts, body welding |
Electronics | Prototyping, low-volume production, final assembly | SMT (Surface Mount Technology), PCB assembly, testing |
Medical Devices | Assembly of small, intricate components, clean room assembly | High-volume production of disposable items, packaging |
Aerospace | Assembly of complex, low-volume components, final assembly | Production of standard parts, fasteners, and connectors |
Consumer Goods | Customized or artisanal products, final assembly | High-volume production of standard items, packaging |
Frequently Asked Questions (FAQ)
-
Q: Can manual and automated assembly be combined in a single production line?
A: Yes, it is possible to have a hybrid assembly line that incorporates both manual and automated processes. This approach can leverage the strengths of both methods, with automated systems handling repetitive, high-volume tasks and manual assembly focusing on more complex or customized steps. -
Q: How can I determine the return on investment (ROI) for an automated assembly system?
A: To calculate the ROI for an automated assembly system, consider factors such as the initial investment cost, the expected increase in productivity, the reduction in labor costs, and the overall impact on product quality and customer satisfaction. Compare these benefits to the ongoing costs of operating and maintaining the automated system over its lifespan. -
Q: Are there any safety considerations when implementing automated assembly?
A: Yes, safety is a critical factor in automated assembly. Proper safeguards, such as physical barriers, light curtains, and emergency stop systems, must be in place to protect workers from potential hazards. Operators should also receive adequate training on the safe operation and maintenance of the automated equipment. -
Q: Can automated assembly systems be reprogrammed to accommodate product changes?
A: Yes, most modern automated assembly systems are designed with flexibility in mind. They can be reprogrammed to accommodate changes in product design or assembly processes. However, the extent of the changes and the complexity of the reprogramming required will determine the time and cost involved. -
Q: How does the skill level of the workforce affect the choice between manual and automated assembly?
A: The skill level of the available workforce can influence the decision between manual and automated assembly. If there is a shortage of skilled workers or if the required skills are difficult to find, automated assembly may be more attractive. On the other hand, if there is a readily available skilled workforce and the products require a high level of craftsmanship, manual assembly may be the preferred choice.
Conclusion
Choosing between manual and automated assembly requires careful consideration of various factors, including production volume, product complexity, labor costs, capital investment, flexibility, and quality requirements. While manual assembly offers greater flexibility and lower initial costs, automated assembly provides higher productivity, consistent quality, and potential long-term cost savings.
Ultimately, the decision depends on the specific needs and resources of your manufacturing operation. By weighing the advantages and disadvantages of each approach and considering the factors outlined in this article, you can make an informed decision on whether manual or automated assembly, or a combination of both, is right for you.
Leave a Reply