Introduction to PCB Layers
Printed Circuit Boards (PCBs) are the backbone of modern electronics. They provide a platform for mounting and interconnecting electronic components, enabling the creation of complex circuits in a compact and efficient manner. PCBs consist of multiple layers, each serving a specific purpose in the overall functionality of the board. In this article, we will explore the seven working layers commonly found in PCBs and their roles in ensuring reliable and high-performance electronic devices.
What are the 7 layers in a PCB?
The seven working layers in a typical PCB are:
- Top Layer (Signal Layer)
- Ground Plane
- Power Plane
- Inner Signal Layer 1
- Inner Signal Layer 2
- Bottom Layer (Signal Layer)
- Solder Mask and Silkscreen
Each layer plays a crucial role in the PCB’s functionality and contributes to the overall performance of the electronic device.
Top Layer (Signal Layer)
The top layer, also known as the component side or the signal layer, is the uppermost layer of the PCB. This layer is where the majority of the electronic components are mounted and soldered. The top layer contains the copper traces that connect the components to form the desired circuit.
Functions of the Top Layer
- Component placement: The top layer provides a surface for placing and soldering electronic components such as resistors, capacitors, ICs, and connectors.
- Signal routing: Copper traces on the top layer route signals between components, allowing for the flow of electrical currents and enabling the circuit to function as intended.
- Solder pads: The top layer features solder pads, which are exposed areas of copper that facilitate the soldering of components to the board.
Design Considerations for the Top Layer
When designing the top layer of a PCB, several factors must be considered:
- Component placement: Components should be placed in a logical and efficient manner, taking into account factors such as signal integrity, thermal management, and manufacturability.
- Trace width and spacing: The width and spacing of copper traces should be carefully designed to ensure proper signal integrity and to minimize crosstalk and electromagnetic interference (EMI).
- Solder mask: A solder mask is applied over the top layer to protect the copper traces and prevent accidental short circuits during the soldering process.
Ground Plane
The ground plane is a continuous layer of copper that serves as a reference point for the electrical signals in the PCB. It is typically located directly beneath the top layer and is connected to the ground points of the electronic components.
Functions of the Ground Plane
- Provides a low-impedance return path for electrical currents, minimizing noise and ensuring stable signal transmission.
- Acts as a shield against electromagnetic interference (EMI) and radio frequency interference (RFI), reducing the impact of external noise on the circuit.
- Helps dissipate heat generated by the electronic components, improving thermal management and overall reliability.
Design Considerations for the Ground Plane
When incorporating a ground plane in a PCB design, the following factors should be considered:
- Continuity: The ground plane should be as continuous as possible, with minimal interruptions to ensure a low-impedance return path for electrical currents.
- Stitching vias: Stitching vias are used to connect the ground plane to the ground points of components on the top and bottom layers, providing a reliable electrical connection.
- Clearance: Adequate clearance should be maintained between the ground plane and other copper features to prevent short circuits and ensure proper insulation.
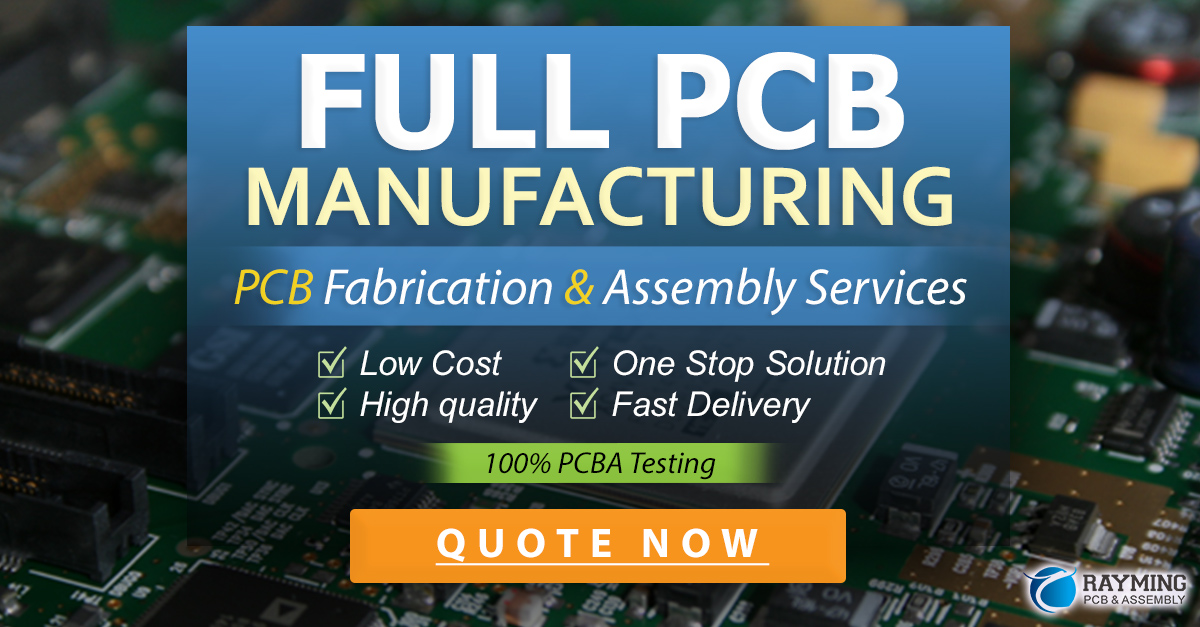
Power Plane
The power plane is a layer dedicated to distributing power to the electronic components on the PCB. It is typically located below the ground plane and is connected to the power pins of the components.
Functions of the Power Plane
- Provides a low-impedance path for distributing power to the electronic components, ensuring stable and reliable power delivery.
- Minimizes voltage drop across the board, maintaining consistent voltage levels for all components.
- Reduces noise and voltage fluctuations, contributing to the overall stability and performance of the circuit.
Design Considerations for the Power Plane
When designing the power plane, the following factors should be taken into account:
- Power requirements: The power plane should be designed to meet the power requirements of all the components on the board, taking into account factors such as current demand and voltage levels.
- Decoupling capacitors: Decoupling capacitors should be placed near the power pins of components to minimize noise and voltage fluctuations.
- Copper thickness: The thickness of the copper in the power plane should be sufficient to handle the required current without excessive voltage drop or heat generation.
Inner Signal Layers
Inner signal layers are additional layers sandwiched between the top and bottom layers of the PCB. These layers are used for routing signals and can significantly increase the routing density and complexity of the board.
Functions of Inner Signal Layers
- Provide additional space for routing signals, allowing for more complex and dense circuit designs.
- Enable the separation of sensitive signals from potential sources of interference, improving signal integrity.
- Allow for the creation of controlled impedance traces, which are essential for high-speed and high-frequency applications.
Design Considerations for Inner Signal Layers
When incorporating inner signal layers in a PCB design, the following factors should be considered:
- Layer stackup: The arrangement of the inner signal layers should be carefully planned to optimize signal routing and minimize crosstalk and EMI.
- Via placement: Vias are used to connect traces on different layers, and their placement should be optimized to minimize signal degradation and ensure manufacturability.
- Impedance control: Controlled impedance traces on inner signal layers require precise design and manufacturing techniques to maintain the desired impedance and ensure reliable signal transmission.
Bottom Layer (Signal Layer)
The bottom layer, also known as the solder side, is the lowermost layer of the PCB. It serves a similar purpose to the top layer, providing a surface for mounting and soldering components and routing signals.
Functions of the Bottom Layer
- Provides additional space for component placement and signal routing, allowing for more complex and compact circuit designs.
- Enables the use of surface-mount technology (SMT) components on both sides of the board, increasing component density and reducing overall board size.
- Facilitates the connection of the PCB to external devices or systems through connectors or mounting holes.
Design Considerations for the Bottom Layer
When designing the bottom layer of a PCB, the following factors should be considered:
- Component placement: Components on the bottom layer should be placed in a manner that optimizes signal routing and minimizes interference.
- Trace routing: Traces on the bottom layer should be routed in a way that ensures signal integrity and minimizes crosstalk and EMI.
- Solder mask and silkscreen: A solder mask and silkscreen should be applied to the bottom layer to protect the copper traces and provide labeling and orientation information for assembly and troubleshooting.
Solder Mask and Silkscreen
The solder mask and silkscreen are additional layers applied to the top and bottom layers of the PCB. While not directly involved in the electrical functionality of the board, they serve important protective and informational purposes.
Functions of the Solder Mask
- Protects the copper traces and pads from oxidation and corrosion, improving the longevity and reliability of the PCB.
- Prevents accidental short circuits during the soldering process by covering the copper areas that should not be soldered.
- Provides electrical insulation between adjacent traces and pads, reducing the risk of short circuits and signal crosstalk.
Functions of the Silkscreen
- Provides labeling and orientation information for components, making assembly and troubleshooting easier.
- Identifies the function and purpose of different parts of the PCB, such as connectors, test points, and mounting holes.
- Enhances the aesthetic appeal of the PCB and provides a professional appearance.
Design Considerations for Solder Mask and Silkscreen
When incorporating solder mask and silkscreen in a PCB design, the following factors should be considered:
- Solder mask color: The color of the solder mask can be chosen based on aesthetic preferences or to improve the visibility of the silkscreen and components.
- Silkscreen legibility: The silkscreen should be clearly legible and easily distinguishable from the solder mask background. Font size, color, and placement should be carefully considered.
- Clearance: Adequate clearance should be maintained between the solder mask openings and the copper features to ensure proper insulation and prevent solder bridges.
Interconnections between Layers
To create a functional PCB, the various layers must be interconnected to allow for the flow of electrical signals and power between components. This is achieved through the use of vias and through-hole components.
Vias
Vias are small holes drilled through the PCB layers and plated with conductive material, typically copper. They provide electrical connections between the different layers of the board.
- Through vias: These vias extend through all layers of the PCB, connecting the top and bottom layers and any inner layers in between.
- Blind vias: These vias connect an outer layer (top or bottom) to an inner layer, but do not extend through the entire board.
- Buried vias: These vias connect two or more inner layers without extending to the outer layers.
Through-hole Components
Through-hole components, such as connectors and some types of capacitors and resistors, have leads that are inserted into holes drilled through the PCB. These holes are plated with conductive material, allowing the leads to be soldered to the board and creating electrical connections between the layers.
PCB Layer Stackup
The arrangement of the various layers in a PCB is known as the layer stackup. The stackup determines the order in which the layers are laminated together and affects the overall performance and manufacturability of the board.
Common Layer Stackups
- Four-layer stackup: This is a common stackup for medium-complexity PCBs, consisting of a top signal layer, ground plane, power plane, and bottom signal layer.
- Six-layer stackup: This stackup adds two additional inner signal layers to the four-layer stackup, providing more routing space for complex designs.
- Eight-layer stackup: This stackup further increases the number of inner signal layers, allowing for even more complex routing and higher component density.
Design Considerations for Layer Stackup
When designing the layer stackup for a PCB, the following factors should be considered:
- Signal integrity: The stackup should be designed to minimize crosstalk and EMI, ensuring reliable signal transmission throughout the board.
- Impedance control: The stackup should be optimized for controlled impedance traces, particularly in high-speed and high-frequency applications.
- Manufacturing constraints: The stackup should be designed with manufacturing capabilities and limitations in mind, ensuring that the board can be reliably and cost-effectively produced.
PCB Layer Thickness and Copper Weight
The thickness of the PCB layers and the amount of copper used in each layer are important factors that affect the performance and manufacturability of the board.
Layer Thickness
The thickness of the PCB layers is typically measured in mils (thousandths of an inch) or microns. Common layer thicknesses include:
- 1.6mm (0.063″): This is a standard thickness for many PCB applications, offering a good balance between durability and ease of manufacturing.
- 0.8mm (0.031″): This thinner material is often used for high-density designs or applications where space is limited.
- 2.4mm (0.094″): This thicker material provides increased durability and is often used in heavy-duty or high-reliability applications.
Copper Weight
The amount of copper used in each layer of the PCB is referred to as the copper weight and is typically measured in ounces per square foot (oz/ft²). Common copper weights include:
- 1 oz/ft²: This is a standard copper weight for many PCB applications, providing a good balance between conductivity and ease of manufacturing.
- 2 oz/ft²: This heavier copper weight offers increased current-carrying capacity and is often used in power-intensive applications or for high-current traces.
- 0.5 oz/ft²: This lighter copper weight is used in high-density designs or applications where signal integrity is a primary concern.
Frequently Asked Questions (FAQ)
1. What is the purpose of having multiple layers in a PCB?
Multiple layers in a PCB allow for more complex routing and higher component density, enabling the creation of more advanced and compact electronic devices. The additional layers also provide benefits such as improved signal integrity, better power distribution, and enhanced EMI shielding.
2. Can a PCB have more than seven layers?
Yes, PCBs can have more than seven layers depending on the complexity and requirements of the design. Some advanced PCBs may have 12, 16, or even more layers to accommodate highly complex circuits and high-density component placement.
3. What is the difference between a blind via and a buried via?
A blind via connects an outer layer (top or bottom) to an inner layer, but does not extend through the entire board. In contrast, a buried via connects two or more inner layers without extending to the outer layers.
4. How does the choice of solder mask color affect the functionality of a PCB?
The choice of solder mask color does not directly affect the functionality of a PCB. However, certain colors may be chosen for aesthetic reasons or to improve the visibility of the silkscreen and components, making assembly and troubleshooting easier.
5. What factors determine the appropriate layer thickness and copper weight for a PCB?
The choice of layer thickness and copper weight depends on several factors, including the specific application, current-carrying requirements, signal integrity needs, and manufacturing constraints. Thicker layers and heavier copper weights are often used in power-intensive or high-reliability applications, while thinner layers and lighter copper weights are suitable for high-density designs or applications where signal integrity is a primary concern.
Conclusion
The seven working layers in a printed circuit board – top layer, ground plane, power plane, inner signal layers, bottom layer, solder mask, and silkscreen – work together to create a functional and reliable platform for electronic components. Each layer serves a specific purpose, from providing a surface for component placement and signal routing to offering protection and information for assembly and troubleshooting.
When designing a PCB, careful consideration must be given to factors such as component placement, trace routing, via placement, layer stackup, and material selection. By understanding the roles and design considerations for each layer, engineers and designers can create PCBs that meet the specific requirements of their applications while ensuring optimal performance and manufacturability.
As electronic devices continue to advance in complexity and functionality, the importance of well-designed and efficiently manufactured PCBs will only continue to grow. By mastering the intricacies of PCB layer design, engineers and manufacturers can stay at the forefront of this ever-evolving field and create innovative solutions that push the boundaries of what is possible in the world of electronics.
Leave a Reply