Understanding Thermal Conductivity
Thermal conductivity is a material property that quantifies the ability of a substance to conduct heat. It is measured in watts per meter-kelvin (W/mK) and represents the rate at which heat is transferred through a material when a temperature gradient is present. Materials with high thermal conductivity allow heat to flow easily, while materials with low thermal conductivity act as thermal insulators.
Aluminum is a popular choice for PCB substrates and layers due to its excellent thermal conductivity. Pure aluminum has a thermal conductivity of approximately 237 W/mK at room temperature, making it an effective heat dissipator. However, the actual thermal conductivity of aluminum in PCBs can vary depending on several factors.
Factors Affecting PCB Aluminum Thermal Conductivity
1. Aluminum Alloy Composition
One of the primary factors influencing the thermal conductivity of aluminum in PCBs is the specific alloy composition. Aluminum alloys are created by combining pure aluminum with other elements to enhance desired properties such as strength, formability, and corrosion resistance. However, the addition of alloying elements can also impact the thermal conductivity of the resulting alloy.
Common aluminum alloys used in PCBs include:
Alloy | Composition | Thermal Conductivity (W/mK) |
---|---|---|
1100 | 99.0% Al | 222 |
6061 | Al-Mg-Si | 167 |
5052 | Al-Mg | 138 |
As evident from the table, different aluminum alloys exhibit varying thermal conductivities. Pure aluminum (1100 alloy) has the highest thermal conductivity, while alloys with added elements like magnesium and silicon have lower thermal conductivities. The choice of aluminum alloy for a PCB depends on the specific requirements of the application, considering factors such as mechanical properties, cost, and manufacturing feasibility.
2. Aluminum Thickness
The thickness of the aluminum layer or substrate in a PCB also influences its thermal conductivity. Thicker aluminum layers provide a larger cross-sectional area for heat conduction, allowing for more efficient heat dissipation. However, increasing the aluminum thickness also affects the overall thickness and weight of the PCB, which may be a consideration in certain applications.
Typical aluminum thicknesses used in PCBs range from 0.5mm to 3.0mm. The selection of aluminum thickness depends on factors such as the power dissipation requirements of the components, the available space within the device, and the manufacturing constraints.
3. Surface Finish and Roughness
The surface finish and roughness of the aluminum layer in a PCB can impact its thermal conductivity. A smooth and uniform surface finish promotes better contact between the aluminum and the adjacent layers, reducing thermal resistance and enhancing heat transfer. Rough or uneven surfaces, on the other hand, can create air gaps or voids that impede heat flow.
Various surface finishing techniques are employed to improve the surface quality of aluminum in PCBs, such as:
- Chemical etching: Removes surface impurities and creates a uniform surface.
- Anodizing: Forms a protective oxide layer on the aluminum surface, enhancing corrosion resistance and adhesion.
- Mechanical polishing: Smoothens the surface by removing irregularities and improving flatness.
The choice of surface finishing technique depends on the specific requirements of the PCB, considering factors such as electrical insulation, adhesion, and manufacturing compatibility.
4. Thermal Interface Materials
Thermal interface materials (TIMs) are used to fill the gaps and improve thermal contact between the aluminum layer and other components or heatsinks in a PCB. TIMs help to reduce thermal resistance and enhance heat transfer by minimizing air gaps and providing a conductive path for heat flow.
Common types of TIMs used in PCBs include:
- Thermal greases: Silicone-based pastes that fill microscopic irregularities and improve thermal contact.
- Thermal pads: Soft, conformable materials that provide electrical insulation and thermal conductivity.
- Phase change materials: Solid materials that melt at operating temperatures to fill gaps and improve thermal contact.
The selection of TIMs depends on factors such as thermal conductivity, electrical insulation requirements, ease of application, and long-term stability.
5. Dielectric Layers and Thermal Vias
In multi-layer PCBs, the presence of dielectric layers and thermal vias can impact the overall thermal conductivity of the aluminum substrate. Dielectric layers, such as FR-4 or polyimide, have lower thermal conductivities compared to aluminum and can act as thermal barriers, impeding heat flow.
To mitigate this issue, thermal vias are often incorporated into the PCB design. Thermal vias are conductive pathways that penetrate through the dielectric layers, allowing heat to flow more efficiently from the aluminum substrate to the surface or other layers. The number, size, and placement of thermal vias are crucial factors in optimizing the thermal performance of the PCB.
Measuring and Simulating Thermal Conductivity
To ensure effective thermal management in PCBs, it is essential to accurately measure and simulate the thermal conductivity of the aluminum substrate and the overall PCB assembly. Various techniques and tools are employed for this purpose:
-
Thermal conductivity measurement: Specialized instruments, such as the guarded hot plate method or the laser flash method, can be used to measure the thermal conductivity of aluminum samples directly.
-
Thermal simulation software: Finite element analysis (FEA) software tools, such as ANSYS or COMSOL, can simulate the thermal behavior of PCBs, considering factors such as material properties, geometry, and boundary conditions. These simulations help in optimizing the thermal design and identifying potential hot spots.
-
Thermal imaging: Infrared cameras can be used to visualize the temperature distribution across a PCB during operation, providing insights into the effectiveness of the thermal management solution.
By leveraging these measurement and simulation techniques, PCB designers can make informed decisions regarding the selection of aluminum alloys, thicknesses, surface finishes, and thermal management strategies to achieve the desired thermal performance.
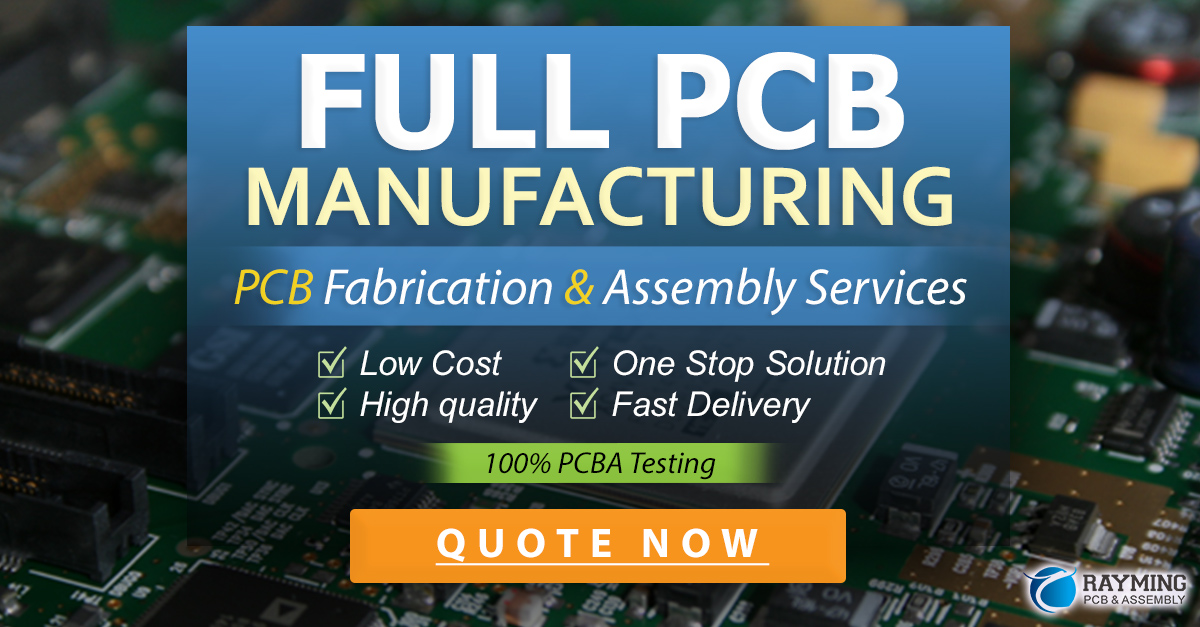
Frequently Asked Questions (FAQ)
1. What is the typical thermal conductivity range for aluminum used in PCBs?
The thermal conductivity of aluminum used in PCBs can vary depending on the specific alloy composition. Pure aluminum (1100 alloy) has a thermal conductivity of around 222 W/mK, while common aluminum alloys used in PCBs, such as 6061 and 5052, have thermal conductivities ranging from 138 to 167 W/mK.
2. How does the thickness of the aluminum layer affect thermal conductivity in PCBs?
Thicker aluminum layers provide a larger cross-sectional area for heat conduction, allowing for more efficient heat dissipation. Increasing the aluminum thickness enhances the thermal conductivity of the PCB. However, the choice of aluminum thickness also depends on other factors such as the overall PCB thickness, weight, and manufacturing constraints.
3. What surface finishing techniques are used to improve the thermal conductivity of aluminum in PCBs?
Various surface finishing techniques are employed to enhance the thermal conductivity of aluminum in PCBs, including chemical etching, anodizing, and mechanical polishing. These techniques help to create a smooth and uniform surface finish, reducing thermal resistance and promoting better contact between the aluminum and adjacent layers.
4. How do thermal interface materials (TIMs) contribute to the thermal conductivity of PCBs?
Thermal interface materials (TIMs) are used to fill gaps and improve thermal contact between the aluminum layer and other components or heatsinks in a PCB. TIMs, such as thermal greases, pads, or phase change materials, help to reduce thermal resistance and enhance heat transfer by minimizing air gaps and providing a conductive path for heat flow.
5. What role do thermal vias play in the thermal conductivity of multi-layer PCBs?
In multi-layer PCBs, thermal vias are conductive pathways that penetrate through the dielectric layers, allowing heat to flow more efficiently from the aluminum substrate to the surface or other layers. The number, size, and placement of thermal vias are crucial factors in optimizing the thermal performance of the PCB and enhancing overall thermal conductivity.
Conclusion
The thermal conductivity of aluminum in PCBs is influenced by several factors, including aluminum alloy composition, thickness, surface finish, thermal interface materials, and the presence of dielectric layers and thermal vias. Understanding these factors is crucial for designing PCBs with effective thermal management solutions.
By selecting appropriate aluminum alloys, optimizing layer thicknesses, employing suitable surface finishing techniques, and incorporating thermal interface materials and vias, PCB designers can enhance the thermal conductivity of the aluminum substrate and ensure efficient heat dissipation. Accurate measurement and simulation techniques further aid in the optimization of the thermal design.
As electronic devices continue to push the boundaries of performance and miniaturization, the importance of effective thermal management in PCBs cannot be overstated. By considering the factors that influence the thermal conductivity of aluminum and implementing appropriate design strategies, PCB manufacturers can create reliable and thermally efficient solutions for a wide range of applications.
Leave a Reply