Visual Inspection
Visual inspection is the first and most basic aspect of OQC. It involves a thorough examination of the product’s appearance, including its color, texture, finish, and overall aesthetics. The following are some of the key points to consider during visual inspection:
Surface Defects
Check for any visible surface defects such as scratches, dents, chips, or cracks. These defects can affect the product’s appearance and functionality and may lead to customer complaints or returns.
Color Consistency
Ensure that the color of the product matches the approved sample or color standard. Any variations in color may indicate issues with the raw materials, processing, or packaging.
Labeling and Packaging
Verify that the product labeling and packaging are correct, legible, and meet the required specifications. Check for any misspellings, incorrect information, or missing labels.
Dimensional Accuracy
Measure the product’s dimensions to ensure that they meet the specified tolerances. Any deviations from the required dimensions may affect the product’s fit, form, or function.
Aspect | Description | Tools Required |
---|---|---|
Surface Defects | Check for scratches, dents, chips, or cracks | Magnifying glass, flashlight |
Color Consistency | Ensure color matches approved sample or standard | Color swatch, spectrophotometer |
Labeling and Packaging | Verify labeling and packaging are correct and legible | Ruler, magnifying glass |
Dimensional Accuracy | Measure dimensions to ensure they meet tolerances | Calipers, micrometer, gauge |
Functional Testing
Functional testing is the process of verifying that the product performs as intended and meets the required specifications. The following are some of the key aspects of functional testing:
Performance Testing
Test the product’s performance under various conditions to ensure that it meets the required standards. This may include testing the product’s speed, accuracy, durability, or efficiency.
Safety Testing
Verify that the product meets the required safety standards and does not pose any risk to the user or the environment. This may include testing for electrical safety, fire resistance, or chemical stability.
Compatibility Testing
Test the product’s compatibility with other products or systems to ensure that it functions as intended. This may include testing the product’s interoperability, connectivity, or software compatibility.
Environmental Testing
Test the product’s performance under various environmental conditions such as temperature, humidity, or altitude. This may include testing the product’s resistance to heat, cold, moisture, or vibration.
Aspect | Description | Tools Required |
---|---|---|
Performance Testing | Test product performance under various conditions | Specialized testing equipment |
Safety Testing | Verify product meets required safety standards | Safety testing equipment |
Compatibility Testing | Test product compatibility with other products or systems | Compatibility testing equipment |
Environmental Testing | Test product performance under various environmental conditions | Environmental testing chamber |
Material Testing
Material testing is the process of verifying that the product’s materials meet the required specifications and are free from defects or contaminants. The following are some of the key aspects of material testing:
Raw Material Inspection
Inspect the raw materials used in the product to ensure that they meet the required specifications and are free from defects or contaminants. This may include testing for purity, composition, or physical properties.
Finished Product Testing
Test the finished product to ensure that it meets the required specifications and is free from defects or contaminants. This may include testing for strength, durability, or chemical resistance.
Compliance Testing
Verify that the product’s materials comply with the required regulations and standards such as RoHS, REACH, or FDA. This may include testing for restricted substances or hazardous materials.
Aspect | Description | Tools Required |
---|---|---|
Raw Material Inspection | Inspect raw materials for defects or contaminants | Microscope, chemical testing equipment |
Finished Product Testing | Test finished product for defects or non-conformities | Specialized testing equipment |
Compliance Testing | Verify product materials comply with regulations and standards | Chemical testing equipment |
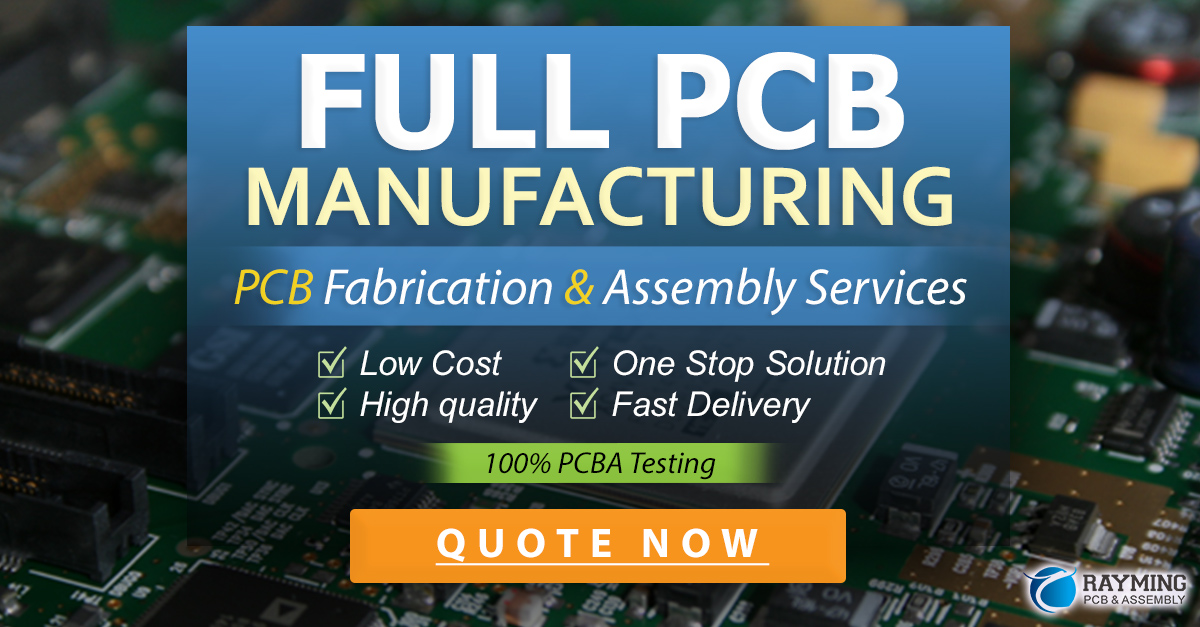
Documentation Review
Documentation review is the process of verifying that the product’s documentation is complete, accurate, and meets the required standards. The following are some of the key aspects of documentation review:
Technical Specifications
Review the product’s technical specifications to ensure that they are complete, accurate, and meet the required standards. This may include reviewing the product’s drawings, schematics, or test reports.
Certificates of Conformity
Verify that the product has the required certificates of conformity such as CE, UL, or ISO. These certificates indicate that the product has been tested and meets the required safety and quality standards.
Labeling and Packaging Artwork
Review the product’s labeling and packaging artwork to ensure that it is complete, accurate, and meets the required standards. This may include reviewing the product’s instructions, warnings, or ingredient lists.
Aspect | Description | Tools Required |
---|---|---|
Technical Specifications | Review product specifications for completeness and accuracy | Technical expertise |
Certificates of Conformity | Verify product has required certificates of conformity | Knowledge of relevant standards |
Labeling and Packaging Artwork | Review labeling and packaging artwork for completeness and accuracy | Attention to detail |
Frequently Asked Questions (FAQ)
1. What is OQC?
OQC stands for Outgoing Quality Control. It is a process of inspecting and testing finished products before they are shipped to customers to ensure that they meet the required quality standards.
2. Why is OQC important?
OQC is important because it helps to identify and prevent defects or non-conformities in products before they reach customers. This can help to reduce customer complaints, returns, and warranty claims, and improve customer satisfaction and loyalty.
3. What are the key aspects of OQC?
The key aspects of OQC include visual inspection, functional testing, material testing, and documentation review. Each of these aspects involves a thorough examination of the product’s appearance, performance, materials, and documentation to ensure that it meets the required quality standards.
4. What tools are used in OQC?
The tools used in OQC vary depending on the aspect being checked. For visual inspection, tools such as magnifying glasses, flashlights, color swatches, and rulers may be used. For functional testing, specialized testing equipment may be required. For material testing, microscopes and chemical testing equipment may be used. For documentation review, technical expertise and attention to detail are essential.
5. How can OQC be improved?
OQC can be improved by implementing a robust quality management system that includes clear quality standards, regular training and audits, and continuous improvement initiatives. Automation and data analytics can also help to streamline the OQC process and identify areas for improvement. Collaboration with suppliers and customers can also help to align quality expectations and improve the overall quality of products.
In conclusion, OQC is a critical process in manufacturing that helps to ensure the quality of products before they are shipped to customers. By checking the various aspects of visual inspection, functional testing, material testing, and documentation review, manufacturers can identify and prevent defects or non-conformities in products and improve customer satisfaction and loyalty. Implementing a robust quality management system, automation, data analytics, and collaboration with suppliers and customers can help to further improve the effectiveness and efficiency of OQC.
Leave a Reply