Introduction to BOM and its Significance in PCB Manufacturing
In the world of electronics manufacturing, particularly in the realm of printed circuit boards (PCBs), the Bill of Materials (BOM) plays a crucial role. A BOM is a comprehensive list of all the components, materials, and quantities required to manufacture a product, such as a PCB. It serves as a roadmap for the entire manufacturing process, ensuring that all necessary parts are accounted for and procured in a timely manner. The importance of a well-structured and accurate BOM cannot be overstated, as it directly impacts the efficiency, cost-effectiveness, and quality of the final product.
What is a Bill of Materials (BOM)?
A Bill of Materials, often referred to as a BOM, is a detailed document that lists all the components, parts, and materials needed to manufacture a product. In the context of PCB manufacturing, a BOM typically includes information such as:
- Component names and descriptions
- Manufacturer part numbers
- Quantities required for each component
- Reference designators (e.g., R1, C2, U3) that link components to their locations on the PCB
- Procurement information (e.g., supplier names, lead times)
The BOM acts as a central repository of information, enabling various departments within an organization (e.g., engineering, purchasing, manufacturing) to collaborate effectively and ensure that the right components are sourced and used in the production process.
Types of BOMs in PCB Manufacturing
In the PCB manufacturing process, there are typically two types of BOMs:
-
Engineering BOM (EBOM): The EBOM is created by the design team and contains all the components and materials required to design and prototype the PCB. It may include multiple options for each component, allowing for flexibility during the design phase.
-
Manufacturing BOM (MBOM): The MBOM is derived from the EBOM and is tailored specifically for the manufacturing process. It contains the final, approved components and quantities required to mass-produce the PCB. The MBOM may also include additional information, such as packaging and shipping requirements.
Understanding the differences between EBOMs and MBOMs is essential for ensuring a smooth transition from design to manufacturing.
The Role of BOM in PCB Design and Development
Facilitating Communication Between Design and Manufacturing Teams
One of the primary functions of a BOM is to bridge the gap between the design and manufacturing teams. The design team creates the initial BOM (EBOM) based on the PCB schematic and layout. This BOM is then reviewed and refined by the manufacturing team to ensure that all components are readily available, cost-effective, and compatible with the manufacturing process. By fostering clear communication and collaboration between these two teams, the BOM helps to minimize errors, delays, and potential design issues.
Enabling Design for Manufacturability (DFM)
Design for Manufacturability (DFM) is a critical aspect of PCB design that focuses on creating designs that are optimized for the manufacturing process. A well-structured BOM plays a vital role in DFM by:
- Identifying components that may be difficult to source or have long lead times
- Highlighting components that are nearing end-of-life (EOL) and suggesting suitable alternatives
- Ensuring that the selected components are compatible with the chosen manufacturing processes (e.g., surface mount technology, through-hole mounting)
By considering these factors early in the design phase, engineers can create PCB designs that are more cost-effective, reliable, and easier to manufacture.
Supporting Prototype Development and Testing
During the prototype development and testing phase, the BOM serves as a reference for assembling and verifying the functionality of the PCB. It ensures that the correct components are used and that the prototype accurately reflects the intended design. Additionally, the BOM can be used to track any changes or modifications made during the prototyping process, which can then be incorporated into the final design.
BOM and Supply Chain Management
Streamlining Component Procurement
An accurate and well-maintained BOM is essential for efficient component procurement. By providing a clear list of required components, quantities, and supplier information, the BOM enables the purchasing team to:
- Negotiate better prices with suppliers based on the total quantity of components required
- Identify potential supply chain risks and develop contingency plans
- Optimize inventory levels and minimize the risk of component shortages or overstock
A streamlined procurement process helps to reduce lead times, minimize costs, and ensure that the necessary components are available when needed for production.
Managing Inventory and Avoiding Shortages
Effective inventory management is crucial for maintaining a smooth and uninterrupted PCB manufacturing process. The BOM plays a central role in inventory management by:
- Providing accurate information on the required quantities of each component
- Enabling the tracking of component stock levels and reorder points
- Facilitating the identification of slow-moving or obsolete components
By closely monitoring inventory levels and proactively addressing potential shortages, manufacturers can avoid production delays and ensure that PCBs are delivered to customers on time.
Facilitating Supplier Collaboration and Communication
A well-structured BOM also serves as a foundation for effective supplier collaboration and communication. By sharing the BOM with suppliers, manufacturers can:
- Ensure that suppliers have a clear understanding of the required components and specifications
- Receive feedback from suppliers on component availability, pricing, and potential alternatives
- Collaborate with suppliers to optimize the supply chain and identify cost-saving opportunities
Strong supplier relationships, built on clear communication and trust, are essential for maintaining a resilient and efficient supply chain.
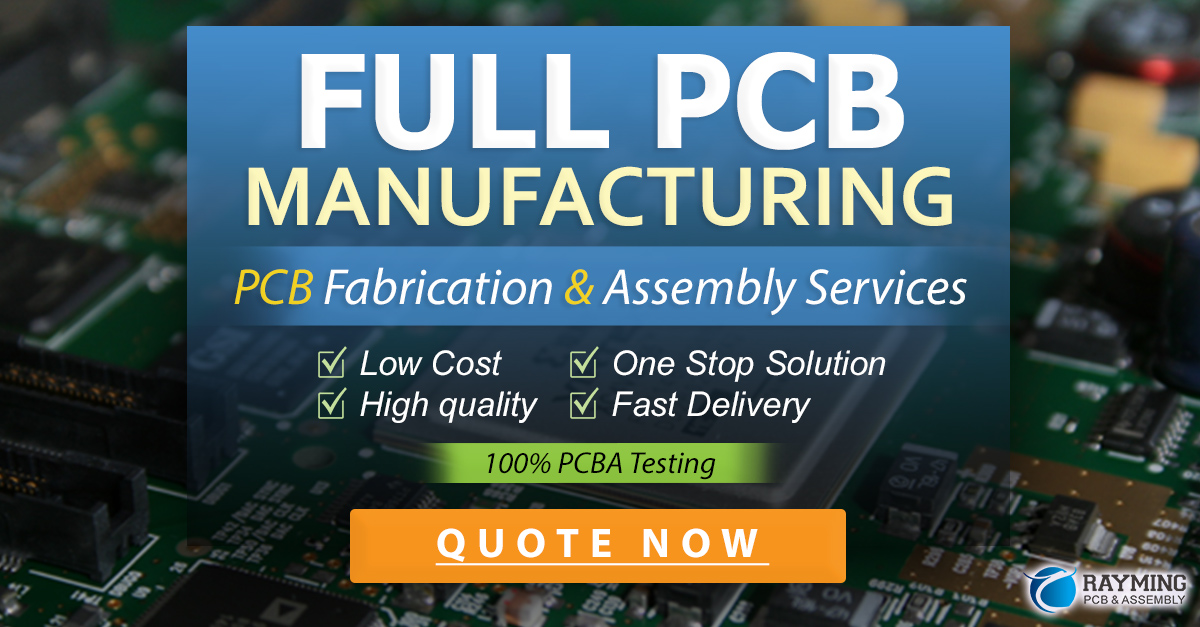
BOM and Quality Control
Ensuring Consistency and Reliability in PCB Manufacturing
Consistency and reliability are paramount in PCB manufacturing, as even minor variations can lead to performance issues or product failures. The BOM plays a critical role in ensuring consistency by:
- Providing a standardized list of components and materials to be used in the manufacturing process
- Enabling the establishment of quality control checkpoints throughout the production process
- Facilitating the tracking and traceability of components used in each PCB
By adhering to a well-defined BOM, manufacturers can minimize the risk of human error, reduce variability, and maintain a high level of product quality.
Facilitating Traceability and Root Cause Analysis
In the event of a product failure or quality issue, the BOM serves as a valuable tool for traceability and root cause analysis. By maintaining accurate records of the components used in each PCB, manufacturers can:
- Quickly identify the specific batch or lot of components associated with the issue
- Trace the origin of the problematic components and collaborate with suppliers to resolve the issue
- Implement corrective actions to prevent similar issues from occurring in the future
Effective traceability and root cause analysis help to minimize the impact of quality issues, protect brand reputation, and maintain customer satisfaction.
Supporting Compliance with Industry Standards and Regulations
Many industries, such as automotive, aerospace, and medical devices, have strict standards and regulations governing the design and manufacture of electronic products. The BOM plays a vital role in supporting compliance with these standards by:
- Ensuring that all components used in the PCB meet the required specifications and certifications
- Providing documentation of the materials and processes used in the manufacturing process
- Enabling the creation of compliance reports and audit trails
By maintaining a comprehensive and accurate BOM, manufacturers can demonstrate their adherence to industry standards and regulations, reducing the risk of non-compliance and potential legal liabilities.
BOM and Cost Management
Enabling Accurate Cost Estimation and Budgeting
An accurate BOM is essential for estimating the cost of a PCB and creating a realistic budget for the project. By providing a detailed breakdown of the required components, quantities, and pricing information, the BOM enables:
- Accurate cost calculations based on the current market prices of components
- Identification of potential cost-saving opportunities (e.g., alternative components, bulk purchasing)
- Creation of detailed financial projections and budgets for the PCB project
Accurate cost estimation and budgeting help manufacturers to make informed decisions, optimize resource allocation, and maintain profitability.
Facilitating Cost Reduction and Optimization Efforts
The BOM also serves as a foundation for cost reduction and optimization efforts. By analyzing the BOM, manufacturers can:
- Identify components that are driving up the overall cost of the PCB
- Evaluate alternative components or suppliers that offer better pricing or performance
- Optimize the PCB design to reduce the number of components or simplify the manufacturing process
Continuous cost reduction and optimization efforts help manufacturers to remain competitive in the market, improve profit margins, and deliver better value to their customers.
BOM and Product Lifecycle Management
Supporting Product Updates and Revisions
Throughout a product’s lifecycle, updates and revisions are often necessary to improve performance, address customer feedback, or comply with new regulations. The BOM plays a crucial role in managing these updates by:
- Providing a clear record of the current components and materials used in the PCB
- Enabling the identification of components that need to be updated or replaced
- Facilitating the communication of changes to the design and manufacturing teams
By maintaining an up-to-date BOM, manufacturers can ensure that product updates and revisions are implemented smoothly and efficiently.
Facilitating End-of-Life (EOL) Management
As components reach their end-of-life (EOL), manufacturers must proactively manage the transition to newer components to avoid disruptions in the supply chain. The BOM supports EOL management by:
- Providing a comprehensive view of the components used in the PCB
- Enabling the identification of components that are nearing EOL
- Facilitating the selection of suitable replacement components
Effective EOL management helps manufacturers to minimize the risk of obsolescence, ensure the long-term availability of their products, and maintain customer satisfaction.
Conclusion
The Bill of Materials (BOM) is a critical component of the PCB manufacturing process, serving as a central source of information that guides the design, procurement, production, and quality control efforts. By maintaining an accurate and comprehensive BOM, manufacturers can streamline their operations, reduce costs, improve product quality, and effectively manage the entire product lifecycle.
As the electronics industry continues to evolve, the importance of a well-structured and efficiently managed BOM will only continue to grow. Manufacturers that prioritize the development and maintenance of accurate BOMs will be better positioned to navigate the challenges of an increasingly competitive and complex market, ultimately delivering superior products and value to their customers.
Frequently Asked Questions (FAQ)
- What is the difference between an Engineering BOM (EBOM) and a Manufacturing BOM (MBOM)?
-
An Engineering BOM (EBOM) is created by the design team and contains all the components and materials required to design and prototype the PCB. It may include multiple options for each component, allowing for flexibility during the design phase. A Manufacturing BOM (MBOM) is derived from the EBOM and is tailored specifically for the manufacturing process. It contains the final, approved components and quantities required to mass-produce the PCB.
-
How does a BOM support Design for Manufacturability (DFM)?
-
A well-structured BOM supports Design for Manufacturability (DFM) by identifying components that may be difficult to source or have long lead times, highlighting components that are nearing end-of-life (EOL) and suggesting suitable alternatives, and ensuring that the selected components are compatible with the chosen manufacturing processes. By considering these factors early in the design phase, engineers can create PCB designs that are more cost-effective, reliable, and easier to manufacture.
-
What role does the BOM play in managing inventory and avoiding shortages?
-
The BOM plays a central role in inventory management by providing accurate information on the required quantities of each component, enabling the tracking of component stock levels and reorder points, and facilitating the identification of slow-moving or obsolete components. By closely monitoring inventory levels and proactively addressing potential shortages, manufacturers can avoid production delays and ensure that PCBs are delivered to customers on time.
-
How does the BOM facilitate traceability and root cause analysis?
-
In the event of a product failure or quality issue, the BOM serves as a valuable tool for traceability and root cause analysis. By maintaining accurate records of the components used in each PCB, manufacturers can quickly identify the specific batch or lot of components associated with the issue, trace the origin of the problematic components, and collaborate with suppliers to resolve the issue. This helps to minimize the impact of quality issues, protect brand reputation, and maintain customer satisfaction.
-
What is the significance of the BOM in managing product updates and revisions?
- Throughout a product’s lifecycle, updates and revisions are often necessary to improve performance, address customer feedback, or comply with new regulations. The BOM plays a crucial role in managing these updates by providing a clear record of the current components and materials used in the PCB, enabling the identification of components that need to be updated or replaced, and facilitating the communication of changes to the design and manufacturing teams. By maintaining an up-to-date BOM, manufacturers can ensure that product updates and revisions are implemented smoothly and efficiently.
Component Type | Importance in BOM |
---|---|
Resistors | Essential for controlling current flow and voltage levels in the PCB. Accurate specification of resistance values, power ratings, and tolerances in the BOM is crucial for ensuring proper circuit functionality and reliability. |
Capacitors | Critical for filtering, decoupling, and energy storage in PCB circuits. The BOM must specify the capacitance values, voltage ratings, and dielectric materials to ensure optimal performance and compatibility with the design. |
Inductors | Used for energy storage, filtering, and impedance matching in PCB designs. Accurate specification of inductance values, current ratings, and tolerances in the BOM is essential for achieving the desired circuit behavior. |
Integrated Circuits (ICs) | The “brains” of the PCB, performing complex functions such as signal processing, control, and communication. The BOM must specify the exact IC part numbers, package types, and any required firmware or software to ensure proper functionality and compatibility. |
Connectors | Enable the PCB to interface with external devices, power sources, and other PCBs. The BOM must accurately specify the connector types, pin counts, and mating requirements to ensure reliable connections and avoid assembly issues. |
Leave a Reply