Aluminum nitride PCBs are one of the most common types in the industry. So how do we distinguish them from others? These are simply conductive in nature. Such PCBs can show remarkable thermal conductivity properties.
They also comprise a highly powerful dielectric material, and their coefficient of thermal expansion is also low as compared to others. The range of availability of aluminum nitride in its colors is an impressive factor. Therefore, it is easier to use in different applications based on different properties and features.
Material Characteristics of Aluminum Nitride PCB
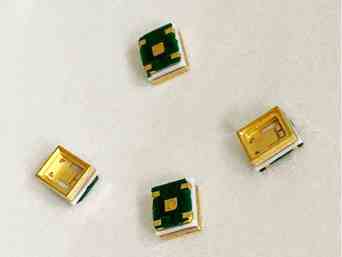
There is no doubt that aluminum nitride shows different chemical and physical attributes that make it interesting to produce. The following are the remarkable chemical properties of these PCBs.
- Good tensile strength
- More dense nature
- Powerful dielectric constant
- Impressive thermal conductivity
- Good breakdown potential
- Min and Max service temperature
Thermal Conductivity
Aluminum nitride PCB is outstanding in thermal conductivity, and therefore, for heat-sensitive applications, we can easily rely on such PCBs.
Thermal Expansion
The thermal expansion of these PCBs ranges between 4.3 to 5.6, and due to this reason, different applications that require thermal regulation can easily perform well with these PCBs.
Electrical Insulation
Such PCBs are remarkable in providing electrical resistance; therefore, with these PCBs, we can ensure the protection and durability of electronics.
Melting Point & Boiling Point
The MP of these PCBs is more than 200 degrees Celsius, and due to this reason, this feature makes them an ideal choice for specific applications.
Density
The density of such PCBs is always an optimum value of 3.26 grams, so the development of electronics can be made easier with their help.
Resistance To Temperature
You might not believe it, but it is true. These PCBs can easily resist a certain amount of temperature. Therefore electronics working at 1370 degrees and lower can easily house aluminum nitride and perform with these PCBs. If the temperature crosses this limit, it will cause oxidation of the metallic components leading to complete damage.
Resistance To Corrosion
Aluminum nitride PCB is also good in corrosion resistance and works well with PCB surface finish. Both these come together to ensure the full protection of PCBs on all counts.
UV Radiation
The oxide layer, in most cases, produces UV radiation, and therefore, these PCBs resist these harmful radiations as well.
Why select Aluminum Nitride PCB?
The reasons behind choosing aluminum nitride PCBs are many, but for every producer, these are different. Some producers rely on their efficient thermal conductivity, while others prefer these PCBs because of their remarkable resistance to temperature and corrosion. The integration makes these PCBs highly portable and small.
They are also supportive of hermetic packaging. There is no doubt that the list of attributes of aluminum nitride PCBs is many. Due to this reason, these are versatile PCBs and sit best for different simple to complex electronic devices. From LEDs to switches and much more, these PCBs are worth it.
There is a considerable addition of aluminum in these PCBs, and therefore, these are highly strong and durable PCB types available in the market. Since these are durable and last longer, there is no need to replace them and spend extra on their maintenance.
How can I Create Aluminum Nitride PCB?
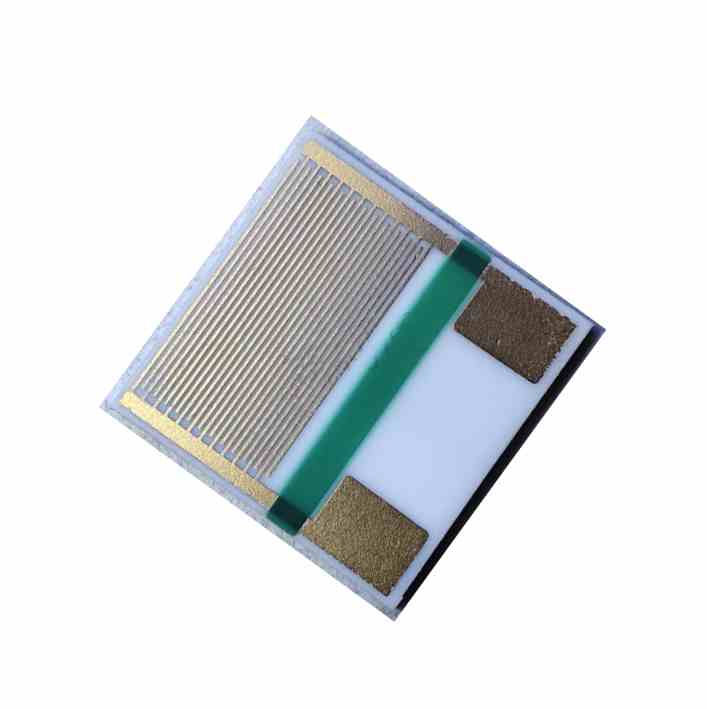
Aluminum nitride is inorganic in nature. For making these PCBs, we rely on different grades of aluminum and combine them with nitride.
There are two major steps involved in the development of aluminum nitride.
- Carbothermal reduction and nitridation
- Direct nitridation
If we compare the above two methods, direct nitridation is commonly used. Basically, we call develop aluminum nitride and alumina nitride both with the same method. In the reaction of aluminum and nitrogen, we see that the reaction burns the aluminum while there is nitrogen in the atmosphere around it. The final product is then treated by milling, and we develop it into different shapes as desired. Different producers rely on direct nitridation because it is feasible and also eco-friendly. The downside of direct nitridation is that purities can form during the process. If they are bigger in size, it will be difficult to handle them at the same time.
What is the cost of an Aluminum Nitride PCB?
The prices are different because of variable parameters. We can find different aluminum nitride PCBs based on their width, size, features, surface finish, and number of layers. However, it is important to get the perfect PCB that matches your needs so that your investment does not go to waste. Experts believe that it is better to research PCBs before buying them to see if their features meet your needs or not. Also, if you have alternative options that are affordable, then going with them is a good choice.
Applications of Aluminum Nitride PCB
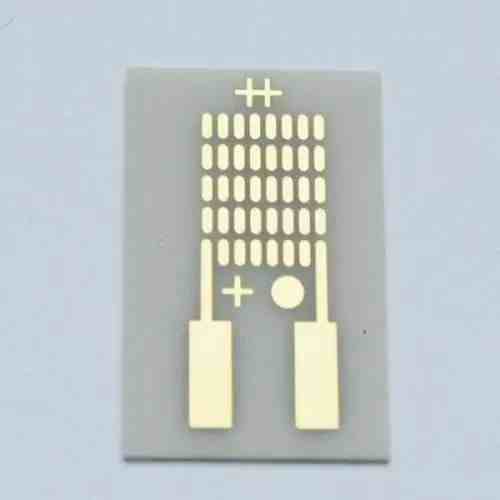
- Devices that need electrical insulation
- Electronics relying mainly on thermal regulation
- Telecommunication can also use aluminum nitride PCBs
- Transportation inverters and cooling systems
- Different types of semiconductor packaging
Limitations of Aluminum Nitride PCB
It is important to take a look at the downside of aluminum nitride PCBs so that you can see if you are really going to rely on them or not. The first negative point is that these PCBs are not affordable at all. Due to this reason, several producers cannot afford to produce them. Sometimes prolonged interaction with aluminum nitride can severely damage human health while targeting the lungs and bones.
Blister Formation and Aluminum Nitride PCB
There have been cases when blister formation complicated the aluminum nitride PCBs. Therefore this has been a common obstruction that many producers face. Let’s read about it more. Sometimes when debris, air pollutants, and metallic shards cannot escape your setup and stick to the boards, they form bumps and blisters. Due to this reason, it is important to remove them during the quality control procedures. Take solder mask blister, for example. It not only damages the appearance and look of the boards but also comprises the nearby components. Some common causes are:
- Improper application of surface finish on the boards can cause blisters.
- If the boards are unclean, they can form bumps as well.
- A blister can develop if the PCBs frequently interact with high temperatures since it deteriorates the protective coating on the boards.
- If the surface finish is uneven, it can be a huge reason behind the blister formation.
The durability of Aluminum Nitride PCB
Aluminum nitride PCB is one of the most durable PCB types produced. It can also perform well during unfavorable circumstances. Therefore by relying on these PCBs, there are little chances of electrical damage and heat fluctuation during the performance of electronics. You can even test such PCBs for stress, but the results will always be positive. All these attributes come together to prove that such PCBs are a good choice to go for electronics that work under stressful conditions. In this way, there will be more chances of improved longevity of these electronic devices as well.
Aluminum Nitride PCB and High-Temperature
These are temperature resistance but only to a certain limit. Don’t forget that excess hot temperature can cause irreversible damage to the PCBs leading to more expense on the reworking. The maximum temperature that these PCBs can hold is 1370 degrees Celsius. Higher temperatures than this range eventually cause oxidation which is not good for the performance of PCBs under stress conditions.
If there is carbon and hydrogen around these PCBs, then they can tolerate even less high temperatures ranging up to 980 degrees only. If you test these PCBs under fixed temperatures, you will realize that these do not undergo damage and also perform in a natural way. Due to this reason, nothing can match their temperature resistance for heat-sensitive applications.
Protective Coatings for Aluminum Nitride PCB
It is obvious that we want to protect our precious aluminum nitride PCBs, and for this purpose, we need something for their longevity. Therefore one solution to protect these PCBs is to use protective coatings or coverings. Different producers are now improving the quality of these PCBs by relying on such protective coverings for PCBs. The results regarding long-term performance and protection were remarkable after these tests were analyzed for the well-being of such PCBs. So below are the commonly used protective coatings suitable for aluminum nitride PCBs.
- It is important to protect the PCBs from corrosion, so in this case, special coatings prove to be handy for saving PCBs from corrosion.
- Thermal spray coating is also common, which completely covers the boards and makes their overall performance more efficient at the same time.
Conclusion
It comes in handy to learn about different aspects before making a decision to save you from loss and poor performance in the long run. The attributes of aluminum nitride PCBs make them highly reliable for durability and excellent performance in challenges. Now you know how these PCBs are an important part of major consumer electronics today!
Leave a Reply