What are RoHS Compliant Circuit Boards?
RoHS stands for the Restriction of Hazardous Substances. It is a directive that originated in the European Union and restricts the use of specific hazardous materials found in electrical and electronic products. The directive went into effect on July 1, 2006.
RoHS compliant circuit boards are those that meet the strict RoHS guidelines for hazardous substances. The main objective of RoHS is to limit the levels of the following six hazardous materials:
- Lead (Pb)
- Mercury (Hg)
- Cadmium (Cd)
- Hexavalent chromium (Cr6+)
- Polybrominated biphenyls (PBB)
- Polybrominated diphenyl ether (PBDE)
By adhering to RoHS, manufacturers ensure their circuit boards contain only trace amounts of these hazardous substances below specified threshold limits. This makes the circuit boards safer for humans and more environmentally-friendly.
RoHS Maximum Concentration Values
The maximum allowed concentrations of the six restricted substances are defined in the RoHS directive. The limits are as follows:
Substance | Allowable Limit |
---|---|
Lead (Pb) | 0.1% |
Mercury (Hg) | 0.1% |
Cadmium (Cd) | 0.01% |
Hexavalent Chromium (Cr6+) | 0.1% |
Polybrominated Biphenyls (PBB) | 0.1% |
Polybrominated Diphenyl Ethers (PBDE) | 0.1% |
These maximum concentration values are weight-by-weight and apply to homogeneous materials, meaning each individual material in the circuit board must comply. For example, the solder and copper traces are considered separate homogeneous materials.
Benefits of Using RoHS Compliant Circuit Boards
There are several key benefits and reasons to use RoHS compliant printed circuit boards:
1. Environmental Protection
One of the primary goals of the RoHS directive is to protect the environment. By limiting the use of hazardous substances in electronics, it reduces pollution and contamination when these products are disposed of or recycled at end-of-life.
The restricted materials can cause significant environmental harm:
– Lead and cadmium are toxic heavy metals that can contaminate soil and water
– Mercury is a potent neurotoxin that bioaccumulates up the food chain
– Hexavalent chromium is carcinogenic and mutagenic
– PBB and PBDE are harmful brominated flame retardants that persist in the environment
Keeping these substances out of circuit boards makes them greener and less damaging when they eventually enter the waste stream. RoHS is part of a global effort to make electronics more sustainable.
2. Consumer Health and Safety
In addition to environmental protection, RoHS also aims to enhance consumer safety. Many of the restricted substances are toxic to humans.
Lead is perhaps the most notable – it can damage almost every system in the body and is especially harmful to children’s developing brains. Even low-level lead exposure has been linked to neurological problems, kidney damage, and reproductive issues.
Cadmium and hexavalent chromium are also known human carcinogens. Mercury can cause neurological damage and impaired cognitive development.
By limiting human exposure to these toxins in electronics, RoHS helps safeguard consumer health. It’s especially important given the prevalence of electronics in homes and workplaces.
3. Regulatory Compliance
For electronics manufacturers, using RoHS compliant circuit boards and components is often necessary for regulatory compliance and market access.
RoHS began as an EU directive but has since been adopted by many other countries, including:
– United Kingdom
– China
– Japan
– India
– South Korea
– Turkey
– Ukraine
– United Arab Emirates
– California (USA)
While the exact RoHS regulations and exemptions may vary slightly by country, the general substance restrictions are similar. Compliance is mandatory to legally sell many types of electronics in these markets.
Even where RoHS isn’t a legal requirement, many companies choose to comply voluntarily. Using RoHS compliant circuit boards demonstrates a commitment to sustainability and consumer safety. It can also simplify the supply chain by allowing standardized BOM for products sold globally.
4. Improved Reliability
While some manufacturers initially worried that lead-free electronics required under RoHS might be less reliable, this has proven not to be the case. In fact, RoHS compliance can actually improve product reliability in some ways.
The switch to lead-free solders drove research and innovation in solder alloys and reflow profiles. Modern lead-free solders can provide excellent mechanical strength and resistance to thermal cycling. Some studies have found lead-free solder joints exhibit better reliability in drop tests.
RoHS has also spurred the electronics industry to reduce its reliance on hazardous substances in general. This has led to the development of new materials and design approaches prioritizing environmental performance. By moving away from problematic substances even beyond the six restricted by RoHS, manufacturers can enhance durability.
Of course, RoHS circuit board design and assembly does require care and process control to ensure reliability. But this is achievable with the right expertise, equipment, and lead-free materials.
Challenges of RoHS Compliance for Circuit Boards
While the benefits of RoHS are clear, compliance does come with some challenges and considerations for circuit board manufacturing. Key issues include:
Lead-Free Soldering
One of the most significant impacts of RoHS on circuit board assembly is the restriction of lead in solder. Traditionally, tin-lead solders were used extensively in electronics manufacturing.
Lead was an ideal alloying element for solder – it provided good wetting, a low melting point, ductility to resist mechanical stress, and helped prevent the growth of tin whiskers. Tin-lead solder was extremely reliable and well understood.
With RoHS limiting lead to 0.1% by weight in homogeneous materials, manufacturers had to switch to lead-free solders. Common alternatives include:
– Tin-silver-copper (SAC) alloys like SAC305
– Tin-copper (SnCu) alloys
– Tin-bismuth (SnBi) alloys
These lead-free solders have higher melting points than tin-lead eutectic solder (217°C vs 183°C for SnPb). This means reflow soldering processes must use higher temperatures, typically peak temperatures around 240-250°C.
The higher reflow temperatures required for lead-free soldering introduce challenges. PCB substrates and components must be able to withstand the increased thermal stress. Some temperature-sensitive parts may not be compatible.
Careful profile development is necessary to ensure good wetting and joint formation without damaging parts. Nitrogen reflow is often used to improve results.
Lead-free solder joints can also be more brittle and prone to mechanical cracking than SnPb joints. Underfill may be needed to reinforce lead-free BGA and CSP solder joints.
Material Declarations and Traceability
To ensure RoHS compliance, electronics manufacturers need to carefully control their material supply chain. Every part and material that goes into the product must be validated as RoHS compliant.
This requires collecting material declarations and certificates of compliance from suppliers. Full material disclosures, lab testing reports, and/or signed declarations stating RoHS conformance are typically needed.
Component manufacturers must exercise due diligence to ensure their parts meet RoHS limits. Switching to compliant surface finishes, leads, and other materials may be necessary. For example, using pure tin or nickel-palladium-gold finishes instead of tin-lead.
Detailed material traceability is a must. Manufacturers need to document the RoHS status of every homogeneous material. Proper labeling and material controls are essential to avoid mixing compliant and non-compliant inventory.
Maintaining RoHS compliance requires ongoing supply chain scrutiny. Due diligence is needed to address the risk of counterfeit components or changes in supplier processes. Regular audits and testing can catch issues.
Legacy Components and Spare Parts
Another challenge of RoHS is dealing with legacy designs and spare parts. Many long-lifecycle products were originally designed with non-RoHS components and materials.
Redesigning these products to be RoHS compliant can be costly and time-consuming. Manufacturers may need to source alternate components, modify the circuit board layout, and re-qualify the assembly process.
In some cases, the original components may no longer be available in RoHS compliant versions. This can necessitate a major redesign to integrate newer parts.
Even if not redesigning legacy products, manufacturers need to carefully manage spare parts and repairs. RoHS does include some exemptions for spare parts to support legacy products. But these are limited in scope.
Mixing RoHS and non-RoHS components in the same assembly should be avoided. This could make the entire product non-compliant. Strict segregation and traceability is a must.
As time goes on, sourcing non-RoHS parts will become increasingly difficult as more suppliers shift to RoHS compliance. Planning ahead for legacy support and last-time buys of non-RoHS parts is advisable.
Testing and Validation
Confirming RoHS compliance requires testing and validation. Manufacturers must ensure every homogeneous material in the product meets the maximum concentration limits for restricted substances.
Several analytical techniques can be used to verify RoHS compliance, including:
– X-ray fluorescence (XRF) spectroscopy
– Scanning electron microscopy/energy dispersive X-ray (SEM/EDX)
– Inductively coupled plasma (ICP) testing
– Atomic absorption spectroscopy (AAS)
Proper sample preparation and test methods are critical for accurate results. For example, preparing samples by grinding or digestion to access internal materials. following standard test procedures like IEC 62321.
Many manufacturers work with third-party labs to analyze material samples and certify RoHS compliance. Comprehensive testing can be expensive and time-consuming.
To minimize the compliance burden, component-level testing is often used instead of board-level. Ensuring each individual component is RoHS compliant can avoid the need for more extensive testing on the assembled board.
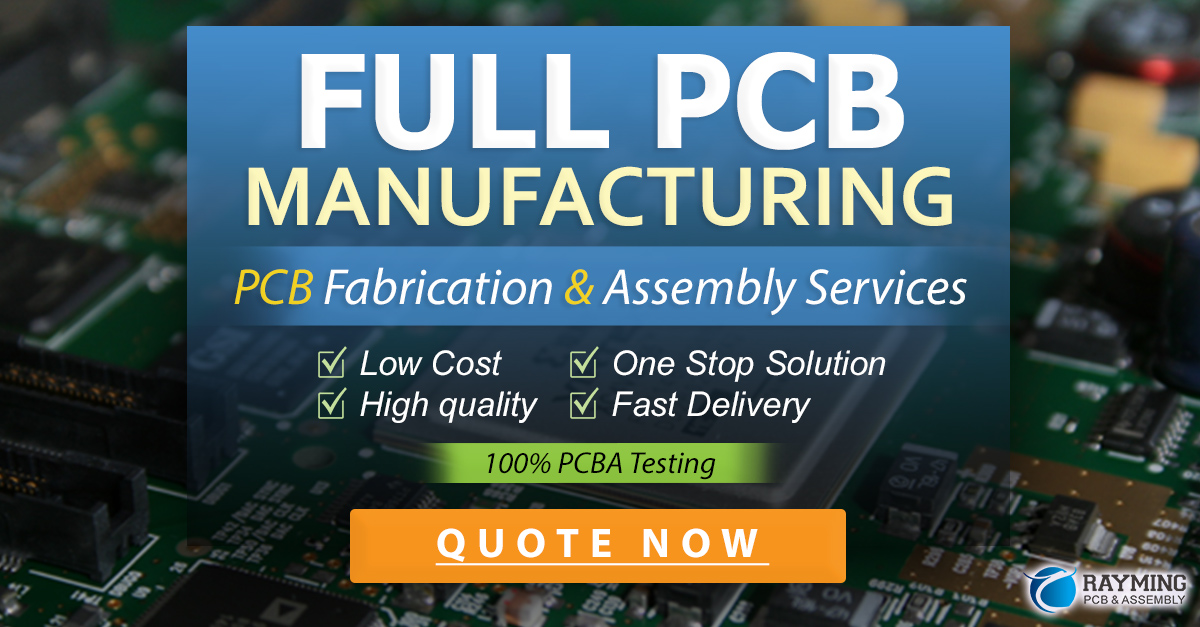
How to Design RoHS Compliant PCBs
So with all these issues in mind, what are some best practices for designing RoHS compliant printed circuit boards?
1. Choose RoHS Compliant Base Materials
When selecting PCB materials, make sure they are RoHS compliant. This includes the substrate material, copper foil, solder mask, silkscreen, and any other coatings or finishes.
Common RoHS compliant PCB substrates include:
– FR-4 epoxy-glass
– Polyimide
– Ceramic
– Metal core (MCPCB)
– Halogen-free materials (HF-FR4)
Avoid materials that may contain restricted substances. For example, some older ceramic substrates used lead in the glass matrix. Make sure to specify RoHS compliant materials in the PCB fabrication drawing.
2. Specify RoHS Compliant Surface Finishes
The choice of solderable surface finish is important for RoHS compliance. Traditional finishes like hot air solder leveling (HASL) used tin-lead alloys and are not RoHS compliant.
Instead, choose a lead-free surface finish such as:
– Immersion tin
– Immersion silver
– Electroless nickel immersion gold (ENIG)
– Electroless nickel electroless palladium immersion gold (ENEPIG)
– Organic solderability preservative (OSP)
Each finish has its own advantages and disadvantages in terms of cost, shelf life, and assembly process compatibility. But all of the above can meet RoHS requirements when properly specified and applied.
3. Use Lead-Free Solder Mask and Marking Inks
Solder mask and marking inks used on the PCB must also be RoHS compliant. Most modern solder mask formulations are lead-free and compliant.
However, it’s important to specifically call out RoHS compliance in the fabrication drawing. Be sure to follow the solder mask manufacturer’s recommended application and curing process for best results.
Some specialized solder masks may contain non-compliant additives. For example, some thermal-cure masks used for high-reliability applications may have fillers that are not RoHS compliant. Always verify the compliance status of any specialty masks.
Similarly, marking inks used for component legends, barcodes, or other silkscreen markings must be RoHS compliant. Many standard white, yellow, and black inks are lead-free and compliant. But double-check the ink composition with your supplier.
4. Select RoHS Compliant Components
A key aspect of RoHS PCB design is selecting components that are all RoHS compliant. This can be one of the most challenging parts of the design process.
Work with component suppliers who can provide RoHS certificates of compliance and material declarations. Make sure to check the RoHS status of all parts, including:
– Passive components like resistors, capacitors, inductors
– Active components like ICs, transistors, diodes
– Electromechanical parts like connectors and switches
– Solder paste and wire
Be aware that some components may be available in both RoHS and non-RoHS versions. Carefully check the part number and datasheet to make sure you are getting the RoHS compliant option.
Some older components may not have a RoHS compliant version available. In these cases, you may need to redesign the circuit to use a newer RoHS compliant alternative.
5. Panelize for Lead-Free Assembly
If the PCB will be assembled using lead-free solder, optimize the panelization for lead-free reflow. This may require adjusting the tab and route locations and sizes.
Because lead-free solder has a higher melting point, the assembly panels will be exposed to more thermal stress during reflow. Overly thin tabs can break or warp.
Placing additional sacrificial tabs at high-stress areas can help. V-score or perforated breakaway tabs are preferred to reduce mechanical stresses.
Panels should be designed to avoid solder bridging. Sufficient spacing is needed between boards and around edge castellations. Lead-free solder tends to wet more readily than SnPb solder.
6. Consider Thermal Reliability
The higher reflow temperatures used for lead-free assembly put more thermal stress on the PCB and components. This can lead to reliability issues if not properly addressed in the design.
Use a thermally-robust PCB substrate material that can handle the higher soldering temperatures without degrading or delaminating. High-Tg FR-4 or polyimide laminates are often used.
Choose components rated for the expected reflow profile and peak temperature. Avoid parts with limited thermal tolerance.
Copper weights and via placement can also affect thermal reliability. Heavier copper weights can help conduct heat away from sensitive areas. Strategic use of thermal vias and planes can also improve heat dissipation.
7. Allow for Lead-Free Rework
Even with a well-optimized lead-free assembly process, some rework may still be necessary. Design the PCB to allow for lead-free rework and repair.
Provide adequate access and clearance for rework tools. Leadless packages like QFNs and LGAs can be especially challenging to rework with lead-free solder.
Use rework-friendly component packages where possible. For example, choosing J-lead or gull-wing leads instead of leadless styles. Including rework test points on the PCB can also aid in troubleshooting.
Designing for selective soldering or localized heating can make rework easier. For example, providing a local thermal relief area around a BGA component.
FAQs About RoHS Compliant Circuit Boards
1. What is the difference between RoHS and REACH?
While both RoHS and REACH are European Union regulations related to chemical substances, they have some key differences:
-
RoHS specifically restricts the use of ten hazardous substances in electrical and electronic equipment. REACH is a broader regulation that covers all chemicals, not just those used in electronics.
-
RoHS compliance is mandatory for many types of electronic products sold in the EU. REACH requires registration of chemicals and notification of substances of very high concern (SVHC). But it does not necessarily restrict their use.
-
RoHS restricts substances at the homogeneous material level, with specific concentration limits. REACH looks at the tonnage of chemicals used and requires different actions based on the volume and hazard.
So while there is some overlap between the two regulations, they serve distinct purposes. RoHS focuses on making electronics safer and more environmentally friendly. REACH aims to improve general chemical safety knowledge and management.
2. How can I tell if a component is RoHS compliant?
There are a few ways to verify if an electronic component is RoHS compliant:
-
Check the manufacturer’s datasheet or website. Many component suppliers will clearly indicate RoHS compliance status in the part documentation. Look for statements like “RoHS Compliant”, “Lead-Free”, or “Green”.
-
Look for the RoHS compliant part number suffix. Some manufacturers use specific suffixes to distinguish RoHS versions of their parts. Common examples include “-G”,
Leave a Reply