Introduction: The Allure and Risks of Cheap PCBs
When it comes to manufacturing electronic devices, the printed circuit board (PCB) is a critical component that connects all the elements together. As a result, many companies and hobbyists are tempted to cut costs by opting for cheap PCBs. However, after nine years in the industry, I can confidently say that this is often a big trap that can lead to numerous problems down the line.
In this article, we will explore the various aspects of cheap PCBs, including their manufacturing process, potential issues, and long-term consequences. By the end, you will have a better understanding of why investing in quality PCBs is essential for the success of your projects.
The Manufacturing Process of Cheap PCBs
H3: Materials Used in Cheap PCBs
One of the primary reasons why some PCBs are cheaper than others is the use of lower-quality materials. These materials may include:
- Thin copper layers
- Low-grade FR-4 substrate
- Inferior solder mask
- Cheap silkscreen ink
While these materials may help reduce the initial cost of the PCB, they can lead to various issues, such as poor conductivity, reduced durability, and even complete failure of the board.
H3: Cutting Corners in the Manufacturing Process
Another way that PCB manufacturers can offer lower prices is by cutting corners during the production process. Some common cost-cutting measures include:
- Skipping or reducing the number of quality control checks
- Using outdated or poorly maintained equipment
- Employing less experienced or skilled workers
- Rushing through the manufacturing process to meet tight deadlines
These practices can result in PCBs with defects, inconsistencies, and reduced overall quality.
Potential Issues with Cheap PCBs
H3: Reduced Reliability and Durability
One of the most significant drawbacks of using cheap PCBs is their reduced reliability and durability. Due to the use of lower-quality materials and subpar manufacturing processes, these boards are more likely to experience issues such as:
- Delamination of layers
- Cracks in the substrate
- Broken or lifted traces
- Intermittent connections
- Complete failure of the board
These problems can lead to malfunctioning devices, increased repair costs, and even safety hazards in some cases.
H3: Inconsistent Performance
Another issue with cheap PCBs is their inconsistent performance. Even if a batch of boards appears to work initially, they may exhibit varying levels of performance over time. This can be due to factors such as:
- Uneven copper thickness
- Inconsistent hole drilling
- Poor alignment of layers
- Inadequate solder mask coverage
These inconsistencies can cause devices to behave unpredictably, leading to frustration for end-users and potential damage to your brand reputation.
H3: Compatibility Issues
Cheap PCBs may also suffer from compatibility issues, particularly when it comes to integrating with other components or systems. This can be caused by:
- Incorrect hole sizes or spacing
- Inaccurate trace widths or spacing
- Improper impedance matching
- Inadequate clearance between components
These compatibility issues can result in difficulties during the assembly process, increased manufacturing costs, and potential delays in product delivery.
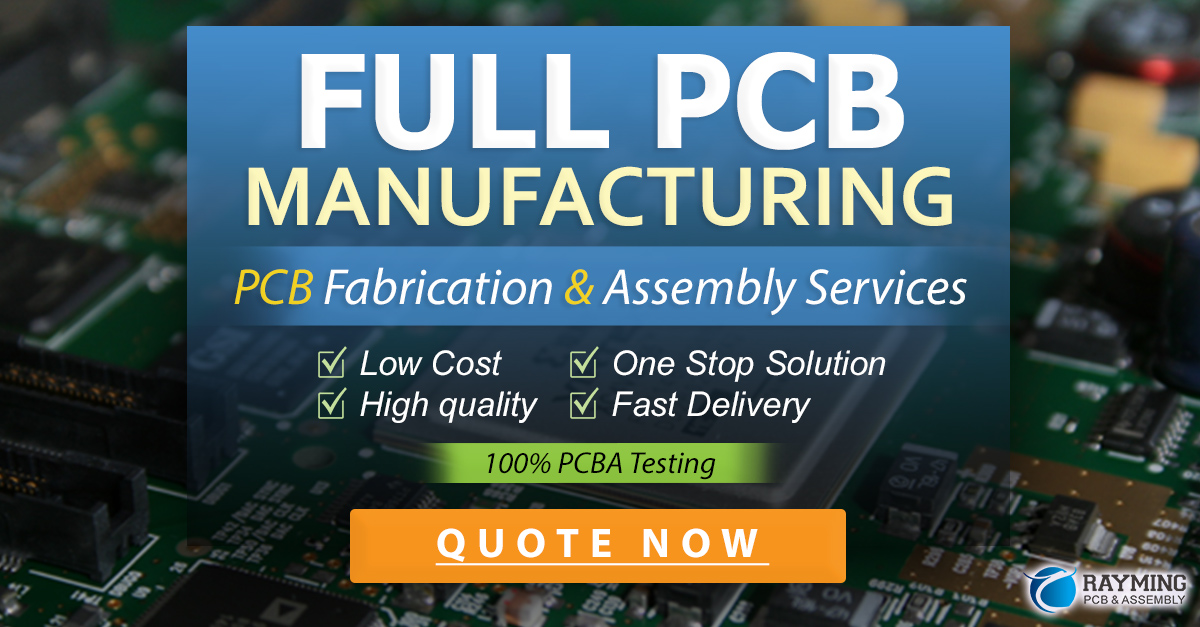
Long-Term Consequences of Using Cheap PCBs
H3: Increased Costs in the Long Run
While using cheap PCBs may seem like a cost-effective solution initially, it can actually lead to increased expenses in the long run. Some of these costs may include:
- Increased rework and repair costs due to PCB failures
- Higher warranty claims and returns from customers
- Potential legal costs associated with product liability issues
- Damage to your company’s reputation, leading to lost sales
In many cases, the long-term costs of using cheap PCBs far outweigh the initial savings.
H3: Delayed Time-to-Market
Another potential consequence of using cheap PCBs is delayed time-to-market for your products. If you encounter issues with your PCBs during the manufacturing or assembly process, you may need to:
- Rework or replace defective boards
- Redesign the PCB to address compatibility issues
- Find alternative suppliers to provide higher-quality boards
These setbacks can significantly delay your product launch, causing you to miss crucial market opportunities and potentially lose customers to competitors.
H3: Negative Environmental Impact
Finally, it’s essential to consider the environmental impact of using cheap PCBs. Many lower-quality boards are manufactured using processes that are harmful to the environment, such as:
- Using toxic chemicals in the manufacturing process
- Improper disposal of waste materials
- Lack of proper recycling or reclamation practices
By supporting these practices, you may be contributing to environmental damage and potentially harming the health of workers involved in the manufacturing process.
How to Avoid the Trap of Cheap PCBs
H3: Invest in Quality Materials and Manufacturing
To avoid the pitfalls of cheap PCBs, it’s essential to invest in quality materials and manufacturing processes. This may involve:
- Choosing reputable PCB Suppliers with a track record of producing high-quality boards
- Specifying the use of high-grade materials, such as thick copper layers and quality substrates
- Ensuring that proper quality control measures are in place throughout the manufacturing process
While this may result in a higher initial cost, the long-term benefits of using quality PCBs far outweigh the upfront expenses.
H3: Prioritize Reliability and Consistency
When selecting a PCB supplier, prioritize reliability and consistency over the lowest price. Look for manufacturers that have:
- Strict quality control standards
- Modern, well-maintained equipment
- Experienced and skilled workers
- A commitment to continuous improvement
By working with a reliable and consistent PCB supplier, you can minimize the risk of encountering issues with your boards and ensure the success of your projects.
H3: Consider the Total Cost of Ownership
When evaluating the cost of PCBs, it’s crucial to consider the total cost of ownership rather than just the initial purchase price. This includes factors such as:
- Expected lifespan of the PCB
- Potential repair and rework costs
- Warranty and return rates
- Impact on customer satisfaction and brand reputation
By taking a holistic view of the costs associated with your PCBs, you can make more informed decisions and avoid the trap of cheap, low-quality boards.
FAQ
Q1: How can I identify a reputable PCB supplier?
A1: To find a reputable PCB supplier, look for companies with a proven track record of producing high-quality boards, positive customer reviews, and certifications such as ISO 9001. Additionally, consider reaching out to industry peers or online forums for recommendations.
Q2: Are there any situations where using a cheap PCB might be acceptable?
A2: In some cases, such as prototyping or low-risk projects, using a cheaper PCB may be acceptable. However, it’s essential to weigh the potential risks and long-term consequences before making a decision.
Q3: How much more should I expect to pay for a high-quality PCB compared to a cheap one?
A3: The cost difference between a cheap and high-quality PCB can vary depending on factors such as the complexity of the design, the materials used, and the manufacturing process. In general, expect to pay anywhere from 20% to 100% more for a high-quality board.
Q4: What should I do if I encounter issues with a cheap PCB?
A4: If you encounter problems with a cheap PCB, first attempt to work with the supplier to resolve the issue. If the supplier is unresponsive or unable to provide a satisfactory solution, consider finding an alternative supplier and investing in higher-quality boards for future projects.
Q5: Can I negotiate with PCB suppliers to get a lower price without sacrificing quality?
A5: In some cases, it may be possible to negotiate a lower price with a PCB supplier without sacrificing quality. This can involve placing larger orders, agreeing to longer lead times, or offering a long-term contract. However, be cautious of suppliers that offer prices that seem too good to be true, as this may indicate a compromise in quality.
Conclusion
In conclusion, while the allure of cheap PCBs can be strong, it’s essential to recognize the potential traps and long-term consequences associated with these low-quality boards. By investing in quality materials, reliable manufacturing processes, and reputable suppliers, you can ensure the success of your projects and avoid the pitfalls of the Cheap PCB Trap.
Remember, the true cost of a PCB extends far beyond the initial purchase price. By considering factors such as reliability, consistency, and the total cost of ownership, you can make informed decisions that will benefit your business in the long run.
Aspect | Cheap PCBs | High-Quality PCBs |
---|---|---|
Materials | Thin copper, low-grade FR-4, inferior solder mask | Thick copper, high-grade FR-4, quality solder mask |
Manufacturing | Cutting corners, reduced quality control | Strict quality control, modern equipment, skilled workers |
Reliability | Reduced reliability and durability | High reliability and durability |
Performance | Inconsistent performance | Consistent performance |
Compatibility | Potential compatibility issues | Designed for compatibility |
Long-Term Costs | Increased repair, warranty, and reputation costs | Lower long-term costs due to higher quality |
Time-to-Market | Potential delays due to rework or redesign | Faster time-to-market due to fewer issues |
Environmental Impact | Potentially harmful manufacturing processes | More environmentally friendly practices |
By keeping these factors in mind and prioritizing quality over short-term cost savings, you can navigate the world of PCB manufacturing with confidence and set your projects up for long-term success.
Leave a Reply