Introduction to BGA Soldering
Ball Grid Array (BGA) soldering is a critical process in Surface Mount Technology (SMT) assembly, which involves attaching a BGA component to a Printed Circuit Board (PCB). BGA packages have become increasingly popular due to their high density of interconnects and small footprint, enabling the miniaturization of electronic devices. However, BGA soldering can be challenging due to the hidden solder joints beneath the component. In this article, we will discuss nine ways to achieve reliable BGA soldering on PCBs in SMT Assembly.
1. Proper PCB Design for BGA Soldering
1.1 PCB Pad Design
The first step in ensuring successful BGA soldering is proper PCB pad design. The PCB pads should be designed according to the BGA package specifications, considering factors such as pad size, shape, and pitch. The pad size should be slightly larger than the BGA ball diameter to allow for proper solder joint formation. Solder mask defined (SMD) pads are commonly used for BGA soldering, as they provide better control over the solder joint shape and prevent bridging.
1.2 PCB Substrate Material
The choice of PCB substrate material is crucial for BGA soldering. The substrate should have good thermal stability and low coefficient of thermal expansion (CTE) to minimize warpage during the soldering process. FR-4 is a commonly used substrate material for BGA soldering, but high-performance materials such as polyimide or BT (Bismaleimide Triazine) may be required for more demanding applications.
1.3 Thermal Vias
Thermal vias are used to improve heat transfer from the BGA package to the PCB during soldering. They help in achieving uniform heating and cooling of the BGA solder joints, reducing thermal stress and improving reliability. The number and size of thermal vias should be optimized based on the BGA package size and power dissipation requirements.
2. Solder Paste Selection for BGA Soldering
2.1 Solder Paste Alloy
The choice of solder paste alloy is important for BGA soldering. Lead-free solder alloys, such as SAC305 (Sn96.5Ag3.0Cu0.5), are widely used due to environmental regulations. These alloys have higher melting temperatures compared to leaded solders, requiring higher reflow temperatures. The solder paste alloy should be compatible with the BGA package and PCB Finishes to ensure good wettability and strong solder joints.
2.2 Solder Paste Particle Size
The solder paste particle size should be selected based on the BGA pitch and pad size. Type 3 (25-45 μm) or Type 4 (20-38 μm) solder paste is commonly used for BGA soldering. Smaller particle sizes provide better print definition and reduce the risk of bridging, especially for fine-pitch BGA packages.
2.3 Solder Paste Flux
The solder paste flux plays a crucial role in removing oxides and promoting solder wetting during the reflow process. No-clean fluxes are preferred for BGA soldering, as they leave minimal residue and eliminate the need for post-soldering cleaning. The flux activity should be selected based on the surface finishes and soldering requirements, ensuring adequate oxide removal without causing excessive solder balling or voiding.
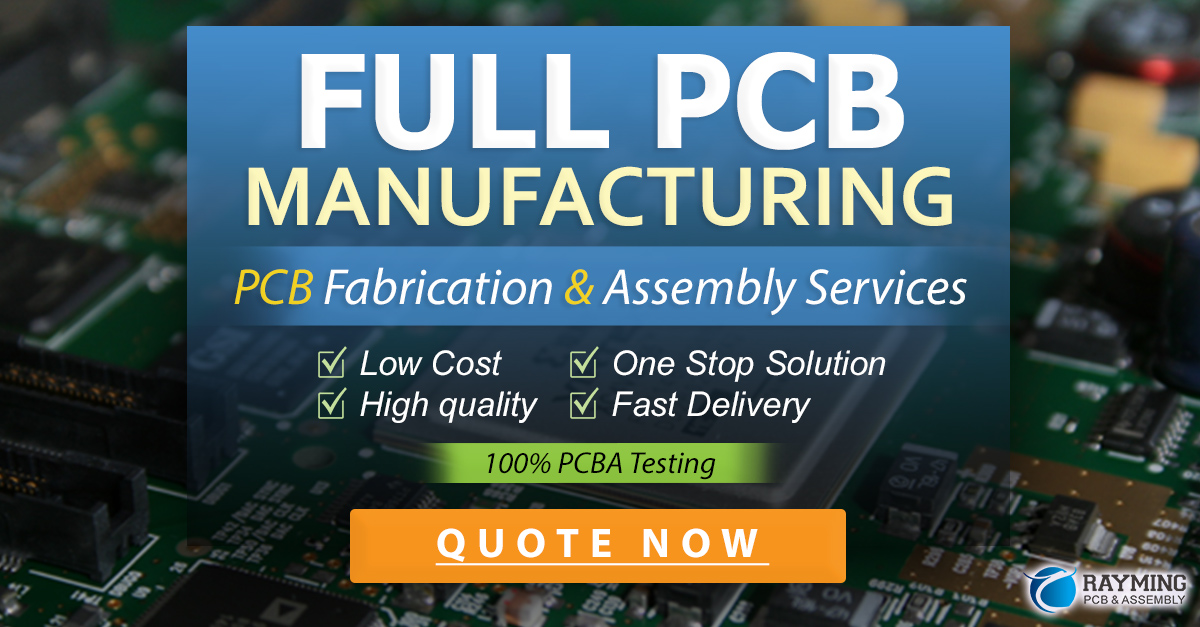
3. Stencil Design for BGA Soldering
3.1 Stencil Thickness
The stencil thickness should be selected based on the BGA ball size and pitch. A typical stencil thickness for BGA soldering ranges from 0.1 mm to 0.15 mm (4-6 mils). Thinner stencils are used for smaller BGA packages to prevent excessive solder paste deposition, while thicker stencils are used for larger packages to ensure sufficient solder volume.
3.2 Aperture Design
The stencil aperture design should be optimized for BGA soldering to ensure consistent solder paste deposition. Circular apertures are commonly used, with the aperture size slightly smaller than the PCB pad size to prevent solder bridging. The aperture wall should have a smooth finish to facilitate solder paste release. Tapered apertures or stepped stencils can be used for fine-pitch BGA packages to improve solder paste transfer efficiency.
3.3 Stencil Material
The stencil material should be selected based on the durability and print quality requirements. Stainless steel is the most commonly used material for BGA soldering stencils due to its good wear resistance and tensile strength. Nickel-plated stencils offer improved paste release and are suitable for fine-pitch applications. Polymer stencils, such as polyimide or epoxy, are also used for their flexibility and conformability to uneven surfaces.
4. Solder Paste Printing for BGA Soldering
4.1 Printer Setup
The solder paste printer should be properly set up for BGA soldering to ensure consistent and accurate paste deposition. The print parameters, such as squeegee pressure, speed, and separation distance, should be optimized based on the solder paste rheology and stencil design. The printer should be equipped with a vision system for automatic stencil-to-PCB alignment and print quality inspection.
4.2 Print Process Control
The solder paste printing process should be monitored and controlled to maintain consistent print quality. Regular checks should be performed to verify the paste volume, height, and shape using 3D solder paste inspection (SPI) systems. The printing environment should be controlled for temperature and humidity to maintain the solder paste properties. Proper cleaning and maintenance of the stencil and printer components are essential to prevent defects and ensure long-term reliability.
5. Component Placement for BGA Soldering
5.1 Pick and Place Machine Setup
The pick and place machine should be properly set up for BGA component placement to ensure accurate and reliable positioning. The machine vision system should be calibrated for the specific BGA package type and orientation. The placement force and speed should be optimized to prevent component damage or misalignment. The nozzle type and size should be selected based on the BGA package dimensions and weight.
5.2 Component Alignment
Accurate component alignment is critical for BGA soldering to ensure proper solder joint formation. The pick and place machine should have high-precision placement capability, with a placement accuracy of ±50 μm or better for fine-pitch BGA packages. Vision-based alignment systems, such as fiducial recognition or corner detection, should be used to compensate for any PCB or component variations. Post-placement inspection should be performed to verify the component position and orientation before reflow soldering.
6. Reflow Soldering Profile for BGA
6.1 Reflow Profile Development
The reflow soldering profile should be carefully developed for BGA soldering to ensure proper solder joint formation and minimize thermal stress. The profile should be optimized based on the solder paste specifications, BGA package characteristics, and PCB design. The key parameters of the reflow profile include:
- Preheat temperature and time
- Soak temperature and time
- Reflow peak temperature and time above liquidus (TAL)
- Cooling rate
The reflow profile should be designed to achieve a gradual and uniform heating of the BGA package and PCB, avoiding excessive temperature gradients or thermal shock.
6.2 Reflow Profile Optimization
The reflow profile should be optimized through iterative testing and validation. Thermal profiling systems, such as thermocouples or thermal cameras, should be used to measure the actual temperature distribution across the BGA package and PCB during the reflow process. The profile should be fine-tuned to achieve the desired solder joint quality, while minimizing the risk of defects such as solder balling, voiding, or component damage. The optimized reflow profile should be documented and consistently maintained for production.
7. Inspection and Testing for BGA Soldering
7.1 Visual Inspection
Visual inspection is the first step in assessing the quality of BGA soldering. The solder joints should be examined for any visible defects, such as bridging, insufficient solder, or solder balls. Microscopic inspection using high-magnification cameras or digital microscopes can provide detailed images of the solder joint shape and surface condition. However, visual inspection has limitations in detecting hidden defects beneath the BGA package.
7.2 X-Ray Inspection
X-ray inspection is a non-destructive method for evaluating the internal structure of BGA solder joints. 2D X-ray systems provide a top-down view of the solder joints, allowing for the detection of bridging, voids, or missing balls. 3D X-ray systems, such as computed tomography (CT), offer a more comprehensive view of the solder joint geometry and can detect subtle defects. X-ray inspection is crucial for ensuring the reliability of BGA soldering, especially for high-density packages.
7.3 Electrical Testing
Electrical testing is performed to verify the functionality and performance of the BGA-soldered PCB. In-circuit testing (ICT) is commonly used to check for short circuits, open circuits, or component failures. Boundary scan testing (BST) can be used to test the interconnections between the BGA package and PCB. Functional testing is conducted to validate the overall system operation and ensure compliance with the design specifications.
8. Rework and Repair for BGA Soldering
8.1 BGA Rework Process
BGA rework involves removing a defective BGA package from the PCB and replacing it with a new one. The rework process should be carefully controlled to prevent damage to the PCB or adjacent components. The key steps in BGA rework include:
- Pre-heating the PCB and BGA package to the desired temperature
- Removing the defective BGA package using a hot air or infrared rework system
- Cleaning the PCB pads and removing any residual solder
- Aligning and placing the new BGA package on the PCB
- Reflowing the solder joints using a localized heating method
- Inspecting and testing the reworked BGA solder joints
8.2 BGA Repair Techniques
In some cases, BGA solder joint defects can be repaired without replacing the entire package. Common BGA repair techniques include:
- Solder bridging removal using a soldering iron or solder wick
- Solder ball attachment using a mini-stencil or solder preforms
- Void filling using a flux pen or solder paste dispensing
- Solder joint reinforcement using underfill or corner bonding
The choice of repair technique depends on the specific defect type, package size, and accessibility. Proper training and specialized tools are required for effective BGA rework and repair.
9. Process Control and Optimization for BGA Soldering
9.1 Statistical Process Control (SPC)
Statistical Process Control (SPC) is a methodology for monitoring and controlling the BGA soldering process to ensure consistent quality. Key process parameters, such as solder paste print volume, reflow temperature profile, and solder joint dimensions, are measured and analyzed using statistical tools. Control charts are used to detect any process variations or trends, enabling timely corrective actions. SPC helps in identifying the root causes of BGA soldering defects and optimizing the process for improved yield and reliability.
9.2 Design of Experiments (DOE)
Design of Experiments (DOE) is a systematic approach for optimizing the BGA soldering process parameters. DOE involves conducting a series of controlled experiments to determine the effect of different factors, such as stencil aperture size, reflow peak temperature, or cooling rate, on the solder joint quality. The experimental data is analyzed using statistical methods to identify the optimal process settings that maximize the solder joint reliability while minimizing defects. DOE helps in developing robust BGA soldering processes that are less sensitive to external variations.
Conclusion
BGA soldering is a critical process in SMT assembly that requires careful control and optimization to achieve reliable solder joints. The nine ways discussed in this article, including proper PCB design, solder paste selection, stencil design, solder paste printing, component placement, reflow soldering profile, inspection and testing, rework and repair, and process control and optimization, provide a comprehensive approach for ensuring successful BGA soldering on PCBs. By understanding and implementing these techniques, manufacturers can improve the quality, reliability, and productivity of their BGA soldering processes.
Frequently Asked Questions (FAQ)
-
What is BGA soldering, and why is it important in SMT assembly?
BGA soldering is the process of attaching a Ball Grid Array (BGA) component to a Printed Circuit Board (PCB) using solder balls. It is important in SMT assembly because BGA packages offer high interconnect density, better electrical performance, and reduced package size compared to other SMT components. -
What are the challenges associated with BGA soldering?
The main challenges in BGA soldering include: - Achieving consistent solder paste deposition and reflow profile
- Ensuring accurate component placement and alignment
- Detecting and preventing solder joint defects, such as bridging, voids, or insufficient solder
-
Performing rework and repair without damaging the PCB or components
-
How can I optimize the reflow soldering profile for BGA soldering?
The reflow soldering profile for BGA soldering can be optimized by: - Selecting the appropriate solder paste alloy and flux
- Designing a profile with gradual and uniform heating, sufficient soak time, and controlled cooling rate
- Conducting thermal profiling to measure the actual temperature distribution across the BGA package and PCB
-
Fine-tuning the profile parameters based on the solder joint quality and defect analysis
-
What inspection methods are used for evaluating BGA solder joint quality?
The common inspection methods for BGA solder joint quality include: - Visual inspection using high-magnification cameras or digital microscopes
- X-ray inspection (2D or 3D) to detect internal defects, such as voids or bridging
-
Electrical testing, such as in-circuit testing (ICT) or boundary scan testing (BST), to verify functionality and interconnections
-
How can Statistical Process Control (SPC) and Design of Experiments (DOE) help in optimizing BGA soldering processes?
SPC and DOE are powerful tools for optimizing BGA soldering processes: - SPC helps in monitoring and controlling the process parameters, detecting variations, and identifying the root causes of defects
- DOE enables the systematic optimization of process parameters, such as stencil design or reflow profile, to improve solder joint quality and reliability
- Both techniques contribute to developing robust and consistent BGA soldering processes that are less sensitive to external variations.
Leave a Reply