1. Understanding the PCB Design Flow
The PCB design flow is a systematic approach to creating a functional and reliable printed circuit board. The process typically includes the following stages:
- Schematic design
- Component selection
- PCB layout
- Design rule checking (DRC)
- Gerber file generation
- PCB fabrication
- PCB Assembly
- Testing and debugging
- Revisions and optimization
By following this structured approach, designers can ensure that their PCB Prototypes meet the required specifications and perform as expected.
2. Schematic Design: The Foundation of PCB Prototyping
The schematic design is the first step in the PCB design flow and serves as the foundation for the entire project. It is a graphical representation of the electronic circuit, showing the interconnections between components and the overall functionality of the device.
When creating a schematic, consider the following best practices:
- Use clear and consistent naming conventions for components and nets
- Group related components together for better organization
- Use appropriate symbols for each component
- Include power and ground connections
- Add notes and comments to clarify the design intent
A well-designed schematic will make the subsequent stages of the PCB design flow more efficient and less prone to errors.
3. Component Selection: Balancing Cost, Performance, and Availability
Choosing the right components for your PCB prototype is essential for ensuring optimal performance and reliability. When selecting components, consider the following factors:
- Functionality: Ensure that the component meets the required specifications and performs the intended function.
- Cost: Balance the component cost with the overall project budget, considering both the prototype and potential production costs.
- Availability: Choose components that are readily available from reliable suppliers to avoid delays in the prototyping process.
- Footprint: Select components with footprints that are compatible with your PCB layout software and manufacturing capabilities.
Creating a bill of materials (BOM) is an essential part of component selection. A BOM is a comprehensive list of all the components required for the PCB, including their quantities, part numbers, and suppliers.
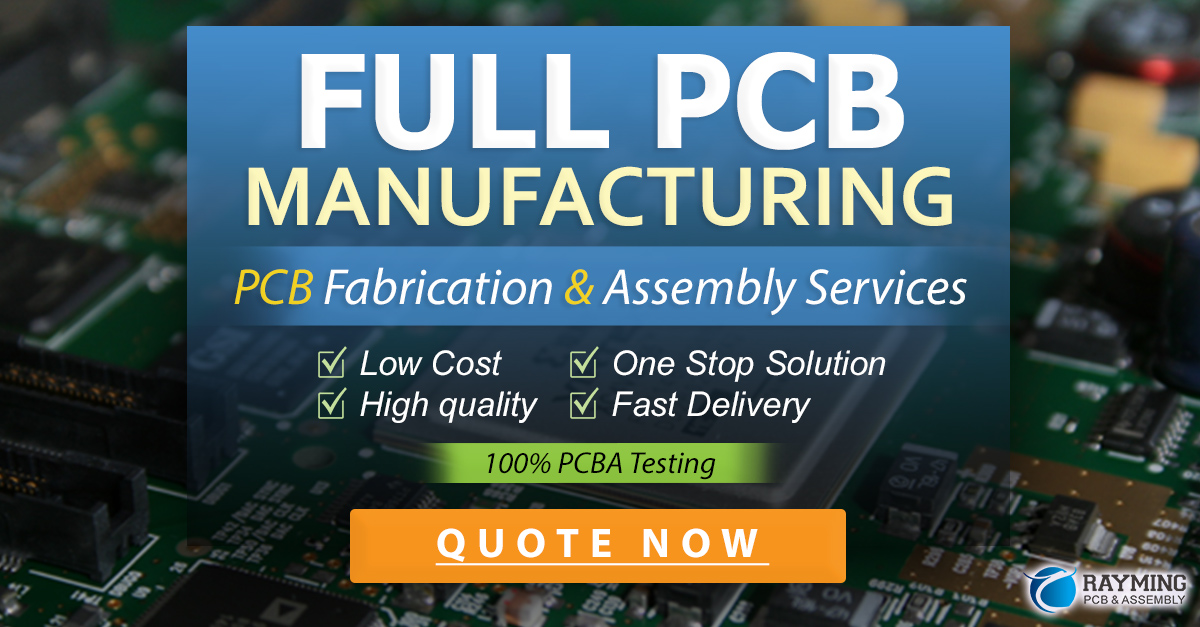
4. PCB Layout: Designing for Manufacturability and Performance
The PCB layout stage involves translating the schematic design into a physical layout of the components and traces on the PCB. A well-designed PCB layout is crucial for ensuring manufacturability, signal integrity, and overall performance.
When designing a PCB layout, keep the following guidelines in mind:
- Use appropriate trace widths and spacing to minimize signal interference and ensure manufacturability
- Properly route power and ground planes to minimize noise and ensure stable power delivery
- Place components strategically to minimize trace lengths and optimize signal paths
- Use vias judiciously to connect traces on different layers
- Follow the manufacturer’s design rules and guidelines for the chosen PCB fabrication process
Proper PCB layout techniques can help minimize design iterations and reduce the time and cost associated with PCB prototyping.
5. Design Rule Checking (DRC): Verifying the PCB Layout
Design rule checking (DRC) is an automated process that verifies the PCB layout against a set of predefined design rules. These rules ensure that the PCB layout meets the manufacturing requirements and industry standards, reducing the likelihood of fabrication issues and improving overall reliability.
Common design rules include:
- Minimum trace width and spacing
- Minimum drill hole size
- Clearance between components and traces
- Solder mask and silkscreen requirements
Running a DRC before generating the final Gerber files can help identify and correct any design issues, saving time and cost in the long run.
6. Gerber File Generation: Preparing Files for PCB Fabrication
Gerber files are the industry-standard format for communicating PCB design information to fabrication houses. These files contain all the necessary information for manufacturing the PCB, including the copper layers, solder mask, silkscreen, and drill data.
When generating Gerber files, ensure that you:
- Use the correct file format and naming conventions specified by the fabrication house
- Include all the necessary layers and files (e.g., copper layers, solder mask, silkscreen, drill files)
- Verify the Gerber files using a Gerber viewer to ensure accuracy and completeness
- Communicate any special requirements or instructions to the fabrication house
Properly generated Gerber files will minimize the risk of manufacturing issues and ensure a smooth transition from design to fabrication.
7. PCB Fabrication: Choosing the Right Manufacturing Partner
Selecting the right PCB fabrication partner is crucial for ensuring the quality and reliability of your PCB prototype. When choosing a manufacturer, consider the following factors:
- Capabilities: Ensure that the manufacturer can accommodate your PCB design’s specific requirements, such as layer count, material, and finish.
- Quality: Look for manufacturers with a proven track record of producing high-quality PCBs and a commitment to quality control processes.
- Lead time: Consider the manufacturer’s lead time for prototype and production runs to ensure that it aligns with your project timeline.
- Cost: Compare pricing from multiple manufacturers, but don’t sacrifice quality for cost savings.
- Communication: Choose a manufacturer with responsive and clear communication channels to facilitate collaboration and address any issues promptly.
Building a strong relationship with your PCB fabrication partner can streamline the prototyping process and ensure the success of your project.
8. PCB Assembly: Bringing the Prototype to Life
PCB assembly involves soldering components onto the fabricated PCB to create a functional prototype. There are two primary methods for PCB assembly:
- Through-hole assembly: Components with wire leads are inserted through holes in the PCB and soldered on the opposite side.
- Surface-mount assembly: Components are placed directly onto pads on the PCB surface and soldered in place.
When planning for PCB assembly, consider the following:
- Component placement: Ensure that the component placement is optimized for ease of assembly and minimizes the risk of assembly errors.
- Soldering techniques: Choose the appropriate soldering technique (e.g., hand soldering, reflow soldering, wave soldering) based on the components and PCB design.
- Assembly documentation: Provide clear and comprehensive assembly instructions, including the BOM, component placement diagram, and any special handling requirements.
Properly planned and executed PCB assembly will result in a functional prototype that accurately represents the intended design.
9. Testing and Debugging: Validating the PCB Prototype
Testing and debugging are essential steps in validating the functionality and performance of the PCB prototype. This process involves:
- Visual inspection: Carefully inspect the assembled PCB for any visible defects, such as incorrect component placement, solder bridges, or damaged components.
- Power-on testing: Apply power to the PCB and verify that it powers up correctly without any shorts or excessive current draw.
- Functional testing: Test the PCB’s functionality against the design specifications, ensuring that all features and interfaces work as intended.
- Signal integrity testing: Use oscilloscopes or logic analyzers to verify signal integrity and identify any issues related to noise, crosstalk, or signal reflections.
- Environmental testing: If required, subject the PCB prototype to environmental stress tests, such as temperature cycling or vibration testing, to ensure its reliability under the intended operating conditions.
When issues are identified during testing, use debugging techniques such as probing, signal tracing, and component substitution to isolate and resolve the problems. Thorough testing and debugging will help refine the PCB design and ensure a more reliable final product.
Revisions and Optimization
Based on the results of testing and debugging, it may be necessary to make revisions to the PCB design to improve performance, reliability, or manufacturability. This iterative process involves:
- Identifying areas for improvement: Analyze the test results and user feedback to identify specific aspects of the design that need refinement.
- Implementing design changes: Make the necessary modifications to the schematic, PCB layout, or component selection to address the identified issues.
- Generating new prototypes: Fabricate and assemble new PCB prototypes incorporating the design changes.
- Retesting and validation: Repeat the testing and debugging process to validate the effectiveness of the design changes and ensure that the revised prototype meets the required specifications.
This iterative process of revision and optimization helps to refine the PCB design and ultimately leads to a high-quality, reliable final product.
Frequently Asked Questions (FAQ)
1. What is the difference between a PCB prototype and a production PCB?
A PCB prototype is a small-scale, initial version of a PCB design used for testing and validation purposes. It may have limited functionality or may not be fully optimized for mass production. In contrast, a production PCB is the final, fully functional version of the PCB designed for large-scale manufacturing and intended for use in the end product.
2. How long does it typically take to create a PCB prototype?
The time required to create a PCB prototype can vary depending on the complexity of the design, the chosen fabrication and assembly methods, and the manufacturer’s lead time. Simple PCB prototypes can be created in a matter of days, while more complex designs may take several weeks. It’s essential to plan ahead and allow sufficient time for the prototyping process to ensure that the project stays on schedule.
3. What are some common mistakes to avoid in PCB prototyping?
Some common mistakes to avoid in PCB prototyping include:
- Failing to properly verify the schematic design and PCB layout before fabrication
- Choosing components that are not suitable for the intended application or are not readily available
- Ignoring manufacturer design rules and guidelines, leading to manufacturability issues
- Inadequate testing and debugging of the assembled prototype
- Not allowing sufficient time for revisions and optimization based on prototype testing results
By being aware of these potential pitfalls and taking steps to mitigate them, designers can streamline the PCB prototyping process and achieve better results.
4. How can I reduce the cost of PCB prototyping?
There are several strategies for reducing the cost of PCB prototyping, including:
- Optimizing the PCB design for manufacturability, which can help reduce fabrication costs
- Choosing cost-effective components that meet the required specifications
- Leveraging open-source hardware and software tools to minimize design and development costs
- Selecting a PCB fabrication partner that offers competitive pricing and volume discounts
- Properly planning and executing the prototyping process to minimize the need for extensive revisions and rework
By implementing these cost-saving measures, designers can create high-quality PCB prototypes while staying within budget constraints.
5. What are the benefits of working with a professional PCB design service?
Working with a professional PCB design service can offer several benefits, including:
- Access to experienced designers with expertise in PCB layout, signal integrity, and manufacturability
- Faster turnaround times and reduced time-to-market due to streamlined design processes and established manufacturer relationships
- Higher-quality PCB designs that are optimized for performance, reliability, and manufacturability
- Reduced risk of design errors and manufacturability issues, which can save time and cost in the long run
- Support and guidance throughout the entire PCB prototyping and production process, from concept to final product
For companies or individuals without in-house PCB design expertise, partnering with a professional PCB design service can be a valuable investment in the success of their electronic product development efforts.
Conclusion
PCB prototyping is a vital stage in the development of electronic devices, enabling designers to test and refine their designs before committing to full-scale production. By understanding the nine fundamental aspects of PCB prototyping and the PCB design flow, designers can create high-quality, reliable prototypes that meet their project requirements.
From schematic design and component selection to PCB layout and assembly, each stage of the process plays a critical role in the success of the final product. By following best practices, leveraging the right tools and resources, and partnering with experienced professionals when necessary, designers can navigate the PCB prototyping process with confidence and achieve optimal results.
As the demand for innovative electronic products continues to grow, mastering the art of PCB prototyping will remain an essential skill for engineers, designers, and hobbyists alike. By staying up-to-date with the latest techniques and technologies, and continually refining their skills through hands-on experience, designers can push the boundaries of what is possible in the world of electronic product development.
Leave a Reply