Introduction to 8 Layer PCBs
An 8 layer printed circuit board (PCB) is a complex, high-density board that consists of eight conductive copper layers laminated together with insulating material. These advanced PCBs are used in sophisticated electronic devices that require high speed, high performance, and miniaturization, such as smartphones, computers, medical equipment, aerospace systems, and more.
Compared to simpler 2 or 4 layer boards, 8 layer PCBs offer several advantages:
- Higher component density and functionality in a smaller footprint
- Improved signal integrity and reduced crosstalk
- Better power delivery and heat dissipation
- Enhanced electromagnetic compatibility (EMC)
However, designing and manufacturing 8 layer PCBs is also much more complex and costly. It requires specialized knowledge, advanced equipment, stringent quality control, and close collaboration between the PCB designer and the manufacturer.
How 8 Layer PCBs Are Manufactured
The fabrication process for 8 layer PCBs involves multiple steps and precise control at every stage to ensure reliability and performance. Here is an overview of the key steps:
-
Design and Validation: The PCB design is created using EDA software, following the customer’s specifications and industry standards. The design files (Gerber, ODB++, IPC-2581, etc.) are carefully reviewed and validated for manufacturability before production begins.
-
Material Selection: The base material (substrate) and copper foil are selected based on the electrical, thermal, and mechanical requirements of the application. The most common materials for 8 layer PCBs are FR-4, high-Tg FR-4, polyimide, and PTFE laminates.
-
Inner Layer Processing: The inner layers are patterned using photolithography and Etching Processes. The copper foil is coated with a photoresist, exposed to UV light through a phototool (mask), developed, and etched to create the desired circuit pattern. The etched panels are then inspected using automated optical inspection (AOI) to detect any defects.
-
Lamination: The patterned inner layers are stacked together with insulating prepreg sheets and copper foils for the outer layers. The stack-up is then laminated under high pressure and temperature in a vacuum press to cure the prepreg and bond the layers together.
-
Drilling: After lamination, the board is drilled with CNC machines to create through-holes and vias that connect the layers electrically. The holes are then cleaned and deburred to remove any debris.
-
Plating: The drilled holes are plated with copper using electroless and electrolytic plating processes to create conductive paths between the layers. The outer layers are also patterned and plated at this stage.
-
Soldermask and Silkscreen: A soldermask layer is applied and patterned to protect the copper traces and prevent Solder Bridging. A silkscreen layer is then printed to add component labels, logos, and other markings.
-
Surface Finish: The exposed copper pads are coated with a surface finish, such as HASL, ENIG, or OSP, to protect them from oxidation and enhance solderability.
-
Electrical Test: The finished boards are electrically tested using Flying Probe or Bed-of-Nails Testers to verify connectivity and detect any shorts or opens.
-
Final Inspection and Packaging: The boards undergo a final visual inspection and are then packaged and shipped to the customer.
Choosing the Right 8 Layer PCB Manufacturer
Selecting a reliable and experienced 8 layer PCB manufacturer is critical for ensuring the quality, performance, and reliability of your end product. Here are some key factors to consider when choosing a manufacturer:
Technical Capabilities
Make sure the manufacturer has the necessary equipment, processes, and expertise to fabricate 8 layer PCBs according to your specifications. Some key capabilities to look for include:
- Fine line and space (3/3 mil or below)
- Thin material (1 mil core, 2 mil prepreg)
- Microvias and buried vias
- Impedance control (±5% or better)
- Tight tolerances (±0.5 mil or better)
- Advanced surface finishes (ENIG, ENEPIG, immersion silver/tin)
- Electrical testing (flying probe, ICT)
Quality Management System
A robust quality management system is essential for ensuring consistent and reliable output. Look for manufacturers with the following certifications:
- ISO 9001 (quality management)
- ISO 14001 (environmental management)
- IATF 16949 (automotive quality management)
- AS9100 (aerospace quality management)
- IPC-A-600 (acceptability of printed boards)
- IPC-6012 (qualification and performance of rigid PCBs)
Experience and Reputation
Choose a manufacturer with a proven track record of producing high-quality 8 layer PCBs for customers in your industry. Look for case studies, testimonials, and references that demonstrate their expertise and reliability.
Communication and Support
Clear and timely communication is key to a successful PCB manufacturing project. Make sure the manufacturer has a responsive and knowledgeable support team that can answer your questions, provide design feedback, and keep you informed throughout the production process.
Cost and Lead Time
While cost is an important consideration, it should not be the only factor in your decision. Look for a manufacturer that offers competitive pricing without compromising on quality or service. Also, consider their lead times and flexibility in accommodating your scheduling needs.
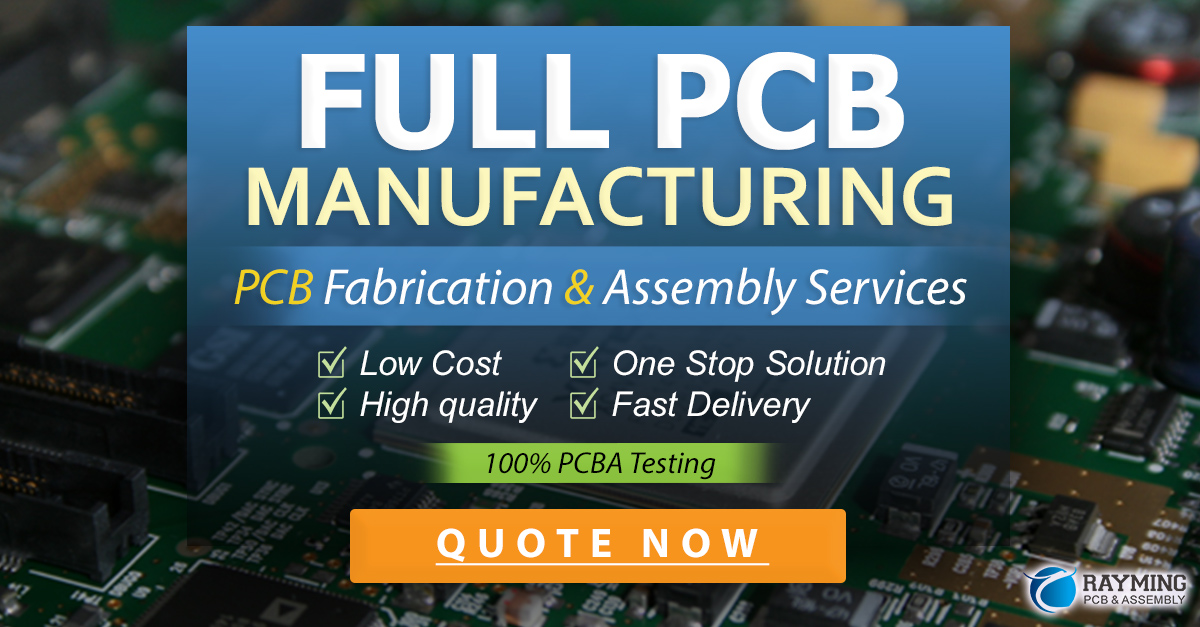
Common Design Challenges and Solutions
Designing an 8 layer PCB requires careful planning and attention to detail to ensure signal integrity, power delivery, and manufacturability. Here are some common design challenges and solutions:
Signal Integrity
- Use proper layer stack-up and routing techniques to minimize crosstalk and EMI
- Match trace impedances to the driver and receiver for optimal signal quality
- Use ground planes and power planes to provide shielding and reduce ground bounce
- Minimize via stubs and unterminated traces to prevent reflections and ringing
Power Delivery
- Use wide and short traces for power and ground to minimize voltage drop and inductance
- Place decoupling capacitors close to ICs to reduce power supply noise
- Use multiple power and ground planes to distribute current evenly and reduce IR drop
- Use solid copper fills for heat dissipation and thermal management
EMC
- Follow proper grounding and shielding techniques to minimize radiated and conducted emissions
- Use filters and transient suppressors to protect against ESD and power surges
- Keep high-speed signals away from board edges and connectors to reduce fringing effects
- Use guard traces and copper pours to isolate sensitive signals from noisy ones
Manufacturability
- Follow the manufacturer’s design rules and guidelines for minimum feature sizes, clearances, and tolerances
- Use standard via sizes and pad stacks to reduce tooling costs and improve yields
- Avoid acute angles and small copper features that can cause acid traps and etching issues
- Use symmetrical and balanced copper distribution to prevent warpage and delamination
FAQ
What is the typical turnaround time for 8 layer PCBs?
The lead time for 8 layer PCBs can vary depending on the complexity of the design, the material availability, and the manufacturer’s capacity. Typical turnaround times range from 2-3 weeks for standard designs to 4-6 weeks for more complex boards with custom materials or finishes.
What is the minimum feature size for 8 layer PCBs?
The minimum feature size depends on the manufacturer’s capabilities and the specific design requirements. Most 8 layer PCB Manufacturers can achieve line width and spacing down to 3/3 mil or 4/4 mil. Some advanced manufacturers can go down to 2/2 mil or even 1/1 mil for high-density designs.
Can I use a mix of materials in an 8 layer PCB?
Yes, it is possible to use different materials for the core and prepreg layers in an 8 layer PCB to optimize the electrical and thermal performance. For example, you can use a high-Tg FR-4 material for the outer layers and a low-loss material like Rogers for the inner layers that carry high-speed signals. However, mixed material stack-ups are more complex to design and manufacture and may have higher costs and longer lead times.
What is the maximum size for an 8 layer PCB?
The maximum size depends on the manufacturer’s equipment and process limitations. Most 8 layer PCB manufacturers can produce boards up to 24″ x 36″ or larger. However, larger boards are more challenging to handle and may require special tooling and processing, which can increase the cost and lead time.
How much does an 8 layer PCB cost?
The cost of an 8 layer PCB depends on various factors, such as the board size, material, quantity, surface finish, and technical requirements. Typical prices for a standard 8 layer PCB (6″ x 6″, FR-4, HASL) range from $50 to $200 per board for small quantities (1-10 pcs) and can drop to $10 to $50 per board for larger volumes (1000+ pcs). However, prices can vary widely depending on the specific design and manufacturer, so it is best to get quotes from multiple sources based on your actual requirements.
Conclusion
8 layer PCBs are a critical component in many advanced electronic systems that require high performance, reliability, and miniaturization. Designing and manufacturing these complex boards requires specialized knowledge, equipment, and processes to ensure signal integrity, power delivery, and manufacturability.
Choosing the right 8 layer PCB manufacturer is essential for the success of your project. Look for a supplier with the necessary technical capabilities, quality management system, experience, and support to meet your specific needs and requirements.
By following proper design guidelines and working closely with your manufacturer, you can overcome common challenges and ensure a smooth and successful production of your 8 layer PCBs.
Here is a summary table of the key considerations for 8 layer PCB manufacturing:
Factor | Consideration |
---|---|
Technical Capabilities | – Fine line and space – Thin material – Microvias and buried vias – Impedance control – Tight tolerances – Advanced surface finishes – Electrical testing |
Quality Management | – ISO 9001 – ISO 14001 – IATF 16949 – AS9100 – IPC-A-600 – IPC-6012 |
Experience and Reputation | – Track record in your industry – Case studies and testimonials – References |
Communication and Support | – Responsive and knowledgeable team – Design feedback and guidance – Regular project updates |
Cost and Lead Time | – Competitive pricing – Flexibility in scheduling – Reasonable lead times |
By carefully considering these factors and working with a reputable 8 layer PCB manufacturer, you can ensure the quality, reliability, and performance of your end product.
Leave a Reply