Introduction
Preparing comprehensive and accurate documentation is a critical step in the printed circuit board (PCB) assembly process. PCB documentation serves as a roadmap for the manufacturing team, guiding them through the assembly process and ensuring that the final product meets the required specifications. In this article, we will discuss seven essential tips to help you create effective PCB Assembly documentation.
Tip 1: Create a Clear Bill of Materials (BOM)
A Bill of Materials (BOM) is a comprehensive list of all the components required to assemble the PCB. It is a crucial document that helps the manufacturing team procure the necessary parts and ensures that the assembly process runs smoothly. Here are some key points to keep in mind when creating a BOM:
- Include a unique identifier for each component, such as a part number or reference designator
- Specify the quantity of each component required
- Provide a detailed description of each component, including the manufacturer, value, and package type
- Indicate any special handling or storage requirements for sensitive components
Here’s an example of a simple BOM table:
Ref Des | Qty | Manufacturer | Part Number | Description |
---|---|---|---|---|
C1, C2 | 2 | Murata | GRM188R71C104KA01D | 0.1uF 16V X7R 0603 |
R1 | 1 | Yageo | RC0603FR-071KL | 1K Ohm 1% 0603 |
U1 | 1 | Texas Instruments | LM3940IMP-3.3/NOPB | 3.3V LDO Regulator |
Tips for Creating an Effective BOM
- Use a spreadsheet or specialized BOM management software to organize the data
- Double-check the accuracy of part numbers and quantities
- Include alternate part numbers if applicable
- Collaborate with the design and procurement teams to ensure the BOM is complete and up-to-date
Tip 2: Provide Detailed Assembly Drawings
Assembly drawings are visual representations of the PCB that provide guidance on component placement, orientation, and soldering requirements. They help the assembly team accurately position components on the board and identify any special assembly instructions. When creating assembly drawings, consider the following:
- Use clear, high-resolution images or vector graphics
- Include a scale and dimensions for reference
- Clearly label component locations and orientations
- Highlight any special assembly requirements, such as hand soldering or selective soldering
- Provide multiple views of the PCB, including top, bottom, and side views if necessary
Best Practices for Assembly Drawings
- Use a consistent naming convention for files and revisions
- Include a legend or key to explain any symbols or abbreviations used
- Ensure that the drawings are legible when printed
- Collaborate with the design team to ensure accuracy and completeness
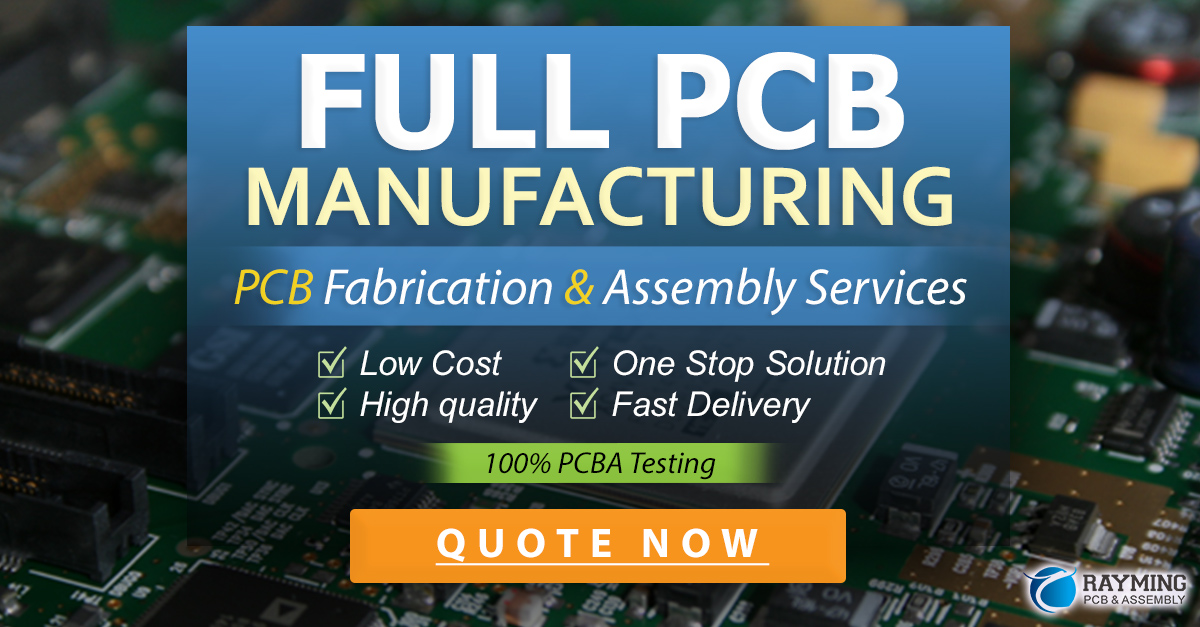
Tip 3: Specify Solder Paste Stencil Requirements
Solder paste stencils are used to apply solder paste to the PCB pads prior to component placement. Properly designed stencils ensure that the correct amount of solder paste is applied, leading to reliable solder joints. When specifying solder paste stencil requirements, consider the following:
- Provide the stencil thickness and material (e.g., laser-cut stainless steel)
- Specify the aperture size and shape for each component pad
- Include any special features, such as stepped stencils or solder paste dams
- Provide the necessary files for stencil fabrication, such as Gerber or CAD files
Solder Paste Stencil Design Guidelines
- Use the appropriate aperture size and shape for each component type
- Consider the PCB Surface Finish and solder paste properties when selecting the stencil thickness
- Incorporate fiducial marks for alignment and registration
- Consult with the assembly team and stencil manufacturer for guidance and best practices
Tip 4: Include Detailed Soldering Instructions
Soldering is a critical step in the PCB assembly process, and proper soldering techniques are essential for ensuring reliable and robust solder joints. When preparing soldering instructions, consider the following:
- Specify the solder alloy and flux type to be used
- Provide the recommended soldering temperature profile and time
- Include any special soldering requirements, such as selective soldering or hand soldering
- Provide guidance on solder joint inspection and acceptance criteria
Soldering Best Practices
- Follow industry standards, such as IPC-A-610, for Soldering Guidelines
- Use the appropriate soldering iron tip size and temperature for each component type
- Ensure proper ventilation and fume extraction during soldering
- Provide training and guidance to the assembly team on soldering techniques and quality control
Tip 5: Provide Comprehensive Test and Inspection Requirements
Testing and inspection are critical steps in ensuring the quality and functionality of the assembled PCB. When preparing test and inspection requirements, consider the following:
- Specify the required tests, such as in-circuit testing (ICT), functional testing, or boundary scan testing
- Provide test specifications and acceptance criteria
- Include any special test fixtures or equipment required
- Specify the inspection criteria for solder joints, component placement, and overall board quality
Test and Inspection Best Practices
- Develop a comprehensive test plan that covers all functional requirements
- Use automated test equipment (ATE) when possible to ensure consistency and accuracy
- Establish clear pass/fail criteria for each test and inspection step
- Document and analyze test results for continuous process improvement
Tip 6: Include Rework and Repair Instructions
Despite best efforts, sometimes assembLED PCBs may require rework or repair due to component failures, assembly errors, or design changes. When preparing rework and repair instructions, consider the following:
- Provide guidelines for identifying and diagnosing common issues
- Specify the appropriate rework and repair techniques for each component type
- Include any special tools or equipment required for rework and repair
- Provide guidance on re-testing and re-inspection after rework or repair
Rework and Repair Best Practices
- Use the appropriate tools and techniques for each rework or repair operation
- Follow industry standards, such as IPC-7711/7721, for rework and repair procedures
- Document all rework and repair operations for traceability and quality control
- Provide training and guidance to the rework and repair team on best practices and techniques
Tip 7: Maintain Revision Control and Document Management
As PCB designs evolve and change over time, it is essential to maintain accurate and up-to-date documentation. Effective revision control and document management practices help ensure that the assembly team always has access to the latest and most accurate information. Consider the following:
- Use a version control system, such as Git or SVN, to manage document revisions
- Clearly label each document with a unique identifier, revision number, and date
- Establish a formal change control process for updating and approving documents
- Ensure that all relevant team members have access to the latest document revisions
Document Management Best Practices
- Use a centralized document repository or document management system
- Establish clear roles and responsibilities for document creation, review, and approval
- Regularly review and update documents to ensure accuracy and relevance
- Provide training and guidance to team members on document management procedures
FAQ
Q1: What is the purpose of a Bill of Materials (BOM) in PCB assembly?
A1: A Bill of Materials (BOM) is a comprehensive list of all the components required to assemble a PCB. It helps the manufacturing team procure the necessary parts and ensures that the assembly process runs smoothly. The BOM includes information such as part numbers, quantities, and descriptions for each component.
Q2: Why are assembly drawings important in PCB assembly documentation?
A2: Assembly drawings provide visual guidance to the assembly team on component placement, orientation, and soldering requirements. They help ensure that components are accurately positioned on the PCB and that any special assembly instructions are clearly communicated. Clear and detailed assembly drawings are essential for consistent and high-quality PCB assembly.
Q3: What factors should be considered when specifying solder paste stencil requirements?
A3: When specifying solder paste stencil requirements, consider factors such as the stencil thickness, material, aperture size and shape, and any special features like stepped stencils or solder paste dams. The stencil design should be optimized for the specific components and PCB surface finish to ensure the correct amount of solder paste is applied for reliable solder joints.
Q4: Why is it important to include test and inspection requirements in PCB assembly documentation?
A4: Including comprehensive test and inspection requirements in the PCB assembly documentation is crucial for ensuring the quality and functionality of the assembled PCB. Tests such as in-circuit testing, functional testing, and boundary scan testing help identify any defects or issues early in the assembly process. Clear inspection criteria for solder joints, component placement, and overall board quality help maintain consistent and high-quality results.
Q5: How can effective document management practices benefit PCB assembly?
A5: Effective document management practices, such as version control and centralized document repositories, help ensure that the assembly team always has access to the latest and most accurate documentation. This reduces the risk of errors and inconsistencies in the assembly process. Regular document reviews and updates help maintain the accuracy and relevance of the documentation over time. Clear roles and responsibilities for document creation, review, and approval streamline the documentation process and ensure accountability.
Conclusion
Preparing comprehensive and accurate PCB assembly documentation is essential for ensuring a smooth and successful manufacturing process. By following the seven tips outlined in this article, you can create effective documentation that guides the assembly team and ensures consistent, high-quality results.
Remember to create a clear and detailed Bill of Materials, provide accurate assembly drawings, specify solder paste stencil requirements, include soldering instructions, define test and inspection criteria, provide rework and repair guidance, and maintain effective document management practices.
By investing time and effort into preparing thorough PCB assembly documentation, you can minimize errors, reduce manufacturing time and costs, and ultimately deliver a high-quality product to your customers.
Leave a Reply