Introduction to PCB Stackups
A printed circuit board (PCB) stackup refers to the arrangement of copper and insulating layers that make up a PCB. The stackup defines the number of layers, their order, thickness, and materials. Choosing the right PCB stackup is crucial for ensuring proper functionality, signal integrity, and manufacturability of the board.
In this article, we will focus on 6 layer PCB stackups, their types, and manufacturing considerations. We’ll also explore the benefits and applications of 6 layer PCBs.
What is a 6 Layer PCB?
A 6 layer PCB is a multi-layer board that consists of six conductive copper layers separated by insulating dielectric material. The copper layers are used for routing traces, power planes, and ground planes. The insulating layers provide electrical isolation between the conductive layers.
6 layer PCBs offer several advantages over fewer-layer boards:
- Increased routing density and complexity
- Better signal integrity and noise reduction
- Improved power delivery and heat dissipation
- Reduced board size and weight
However, 6 layer PCBs are also more expensive and complex to manufacture compared to 2 or 4 layer boards. Careful design and stackup planning are essential for successful 6 layer PCB Fabrication.
Types of 6 Layer PCB Stackups
There are several common types of 6 layer PCB stackups, each with its own characteristics and benefits. The choice of stackup depends on the specific requirements of the application, such as signal speed, power delivery, EMI Shielding, and cost.
1. Standard 6 Layer Stackup
The standard 6 layer stackup is the most basic and widely used configuration. It consists of the following layers (from top to bottom):
- Signal layer 1
- Ground plane
- Signal layer 2
- Power plane
- Signal layer 3
- Signal layer 4
The signal layers are used for routing traces, while the ground and power planes provide low-impedance paths for return currents and power distribution. This stackup offers a good balance between signal integrity, power delivery, and manufacturing cost.
2. 6 Layer Stackup with Dual Ground Planes
For applications that require better signal integrity and EMI reduction, a 6 layer stackup with dual ground planes can be used. This stackup has the following configuration:
- Signal layer 1
- Ground plane 1
- Signal layer 2
- Power plane
- Ground plane 2
- Signal layer 3
The two ground planes provide additional shielding and reduce crosstalk between signal layers. This stackup is suitable for high-speed digital designs or sensitive analog circuits.
3. 6 Layer Stackup with Buried and Blind Vias
Buried and blind vias are used to connect inner layers without penetrating the entire board thickness. This allows for more compact routing and reduces the number of drilling operations.
A 6 layer stackup with buried and blind vias may look like this:
- Signal layer 1 (with blind vias)
- Ground plane
- Signal layer 2 (with buried vias)
- Power plane
- Signal layer 3 (with buried vias)
- Signal layer 4 (with blind vias)
Buried vias connect inner layers (2-5), while blind vias connect outer layers (1-2 and 5-6). This stackup offers higher density and flexibility but is also more expensive due to the additional processing steps.
Stackup Comparison Table
Here’s a comparison table summarizing the key differences between the three 6 layer PCB stackups:
Stackup Type | Layers | Features | Benefits | Cost |
---|---|---|---|---|
Standard | S-G-S-P-S-S | Basic configuration | Balanced performance and cost | $ |
Dual Ground | S-G-S-P-G-S | Additional ground plane | Improved signal integrity and EMI reduction | $$ |
Buried/Blind | S-G-S-P-S-S (with vias) | Inner layer connections | Higher density and flexibility | $$$ |
S – Signal, G – Ground, P – Power
6 Layer PCB Manufacturing Process
Manufacturing a 6 layer PCB involves several steps, each requiring precise control and attention to detail. The basic process flow is as follows:
-
Design and Stackup Planning: The PCB design is created using EDA software, and the stackup is defined based on the application requirements and manufacturing constraints.
-
Material Selection: The appropriate copper foil, dielectric material, and solder mask are selected based on the desired electrical and mechanical properties.
-
Inner Layer Fabrication: The inner layers (2-5) are patterned and etched using photolithography and chemical Etching Processes. Alignment holes are drilled for registration.
-
Lamination: The inner layers are stacked and laminated together with prepreg (pre-impregnated) dielectric material under heat and pressure to form a solid board.
-
Drilling: Through-holes, vias, and tooling holes are drilled using CNC machines. For buried and blind vias, additional drilling steps are performed before lamination.
-
Plating: The drilled holes are plated with copper to form electrical connections between layers. Additional copper is plated on the outer layers to the desired thickness.
-
Outer Layer Patterning: The outer layers (1 and 6) are patterned and etched using similar processes as the inner layers.
-
Solder Mask Application: A solder mask is applied and patterned to protect the copper traces and prevent solder bridging during assembly.
-
Surface Finish: A surface finish (such as HASL, ENIG, or OSP) is applied to the exposed copper areas to prevent oxidation and enhance solderability.
-
Silkscreen and Legend: Text, logos, and component designators are printed on the board using silkscreen or direct legend processes.
-
Electrical Testing: The finished board is tested for continuity, insulation resistance, and other electrical parameters to ensure functionality and reliability.
Manufacturing Challenges and Considerations
Manufacturing 6 layer PCBs presents several challenges and considerations compared to simpler boards:
- Tighter tolerances and registration requirements
- Increased risk of defects and yield loss
- Higher material and processing costs
- Longer lead times and minimum order quantities
- Specialized equipment and expertise needed
To ensure successful 6 layer PCB manufacturing, it’s important to work closely with an experienced and capable PCB manufacturer. The manufacturer should have the necessary technologies, processes, and quality control measures in place to handle the complexity of 6 layer boards.
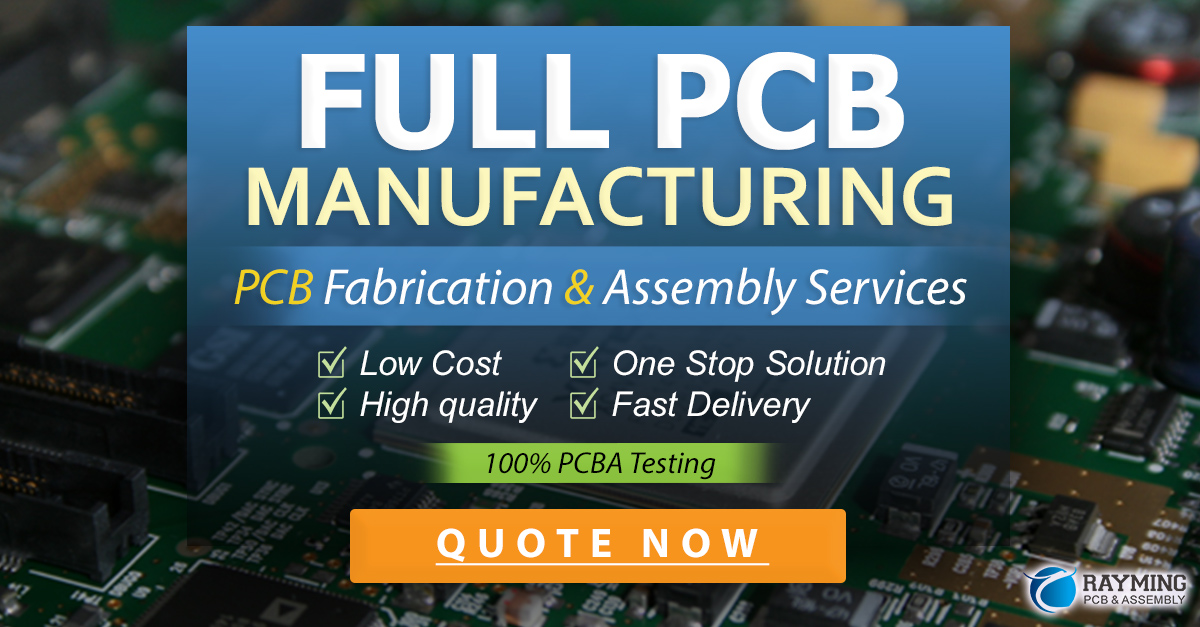
Benefits and Applications of 6 Layer PCBs
6 layer PCBs offer several benefits that make them suitable for a wide range of applications:
Benefits
- High routing density and complexity
- Improved signal integrity and noise reduction
- Better power delivery and heat dissipation
- Reduced board size and weight
- Increased reliability and durability
Applications
- High-speed digital systems (e.g., computers, networking equipment)
- Telecommunications and wireless devices
- Industrial controls and automation
- Medical devices and instrumentation
- Aerospace and defense systems
- Automotive electronics
Frequently Asked Questions (FAQ)
1. What is the typical thickness of a 6 layer PCB?
The typical thickness of a 6 layer PCB ranges from 0.8mm to 2.0mm, depending on the copper weight and dielectric material used. The most common thickness is around 1.6mm.
2. Can 6 layer PCBs be made with flexible materials?
Yes, 6 layer PCBs can be made with flexible materials such as polyimide or PET. Flexible 6 layer PCBs are used in applications that require bending or folding, such as wearable devices or compact electronics.
3. What is the minimum feature size achievable on a 6 layer PCB?
The minimum feature size (trace width and spacing) on a 6 layer PCB depends on the manufacturing capabilities of the PCB fabricator. Typically, 3 mil (0.075mm) traces and spaces are achievable on inner layers, while 4-5 mil (0.1-0.125mm) is more common on outer layers.
4. How much does a 6 layer PCB cost compared to a 4 layer board?
The cost of a 6 layer PCB is typically 30-50% higher than a comparable 4 layer board, due to the additional materials, processing steps, and complexity involved. However, the exact cost difference depends on factors such as board size, quantity, and design features.
5. What are the lead times for manufacturing 6 layer PCBs?
Lead times for 6 layer PCBs are generally longer than for simpler boards, due to the additional processing steps and quality control measures required. Typical lead times range from 2-4 weeks, depending on the manufacturer’s capacity and the specific requirements of the project.
Conclusion
6 layer PCBs are a versatile and high-performance option for a wide range of electronic applications. By understanding the different stackup types, manufacturing processes, and design considerations involved, engineers and product designers can effectively utilize 6 layer PCBs to achieve their goals.
Choosing the right 6 layer PCB stackup and working with an experienced manufacturer are key factors in ensuring a successful outcome. With careful planning and execution, 6 layer PCBs can provide the routing density, signal integrity, and power delivery needed for today’s complex electronic systems.
Leave a Reply