What is a PCB Solder Mask?
A PCB (printed circuit board) solder mask, also known as a solder resist or solder stop mask, is a thin lacquer-like layer of polymer applied to the copper traces of a PCB. The main purpose of the solder mask is to prevent solder from bridging between conductors and creating short circuits during the soldering process. It also provides protection against oxidation and contamination of the copper traces.
The solder mask is applied to the PCB after the copper traces have been etched but before the components are soldered onto the board. Openings in the solder mask, called pads or lands, expose areas of the underlying copper layer where solder is to be applied to create electrical connections.
Why is a Solder Mask Important in PCB Manufacturing?
A solder mask serves several critical functions in the PCB manufacturing process and for the overall reliability of the finished circuit board:
-
Prevents solder bridges: The primary purpose of the solder mask is to prevent solder from unintentionally bridging adjacent copper traces during the soldering process, which would create short circuits and cause the PCB to malfunction.
-
Protects against oxidation: Exposed copper traces can oxidize over time, leading to reduced conductivity and potential signal integrity issues. The solder mask acts as a barrier, protecting the copper from oxidation and ensuring long-term reliability.
-
Guards against contamination: The solder mask also helps to prevent contamination of the copper traces from dust, dirt, and other environmental factors that could degrade the performance of the PCB.
-
Improves aesthetics: Solder masks are available in various colors, with green being the most common. The uniform color of the solder mask enhances the visual appearance of the PCB and makes it easier to inspect for defects.
-
Aids in component placement: The openings in the solder mask clearly define where components should be soldered onto the PCB, making the assembly process more efficient and reducing the likelihood of errors.
-
Enhances insulation: The solder mask provides an additional layer of insulation between copper traces, helping to prevent electrical leakage and improve the overall performance of the PCB.
The 4 Main Types of PCB Solder Mask
There are four primary types of solder mask used in PCB manufacturing, each with its own unique characteristics and advantages:
1. Liquid Photoimageable Solder Mask (LPSM)
Liquid photoimageable solder mask (LPSM) is the most common type of solder mask used in PCB manufacturing. LPSM is a liquid polymer that is applied to the PCB using a screen printing process or a curtain coating method. Once applied, the LPSM is exposed to UV light through a photomask, which hardens the exposed areas while leaving the unexposed areas soluble. The soluble areas are then removed using a developer solution, revealing the copper pads beneath.
Advantages of LPSM:
– High resolution and precision
– Excellent adhesion to the PCB surface
– Good electrical insulation properties
– Available in a variety of colors
– Cost-effective for high-volume production
Disadvantages of LPSM:
– Requires a clean room environment for application
– Longer processing time compared to other methods
– Higher setup costs for low-volume production
2. Dry Film Photoimageable Solder Mask (DFSM)
Dry film photoimageable solder mask (DFSM) is a solid film version of the photoimageable solder mask. The DFSM is laminated onto the PCB surface using heat and pressure, then exposed to UV light through a photomask. The unexposed areas are removed using a developer solution, similar to the LPSM process.
Advantages of DFSM:
– Faster application process compared to LPSM
– More consistent thickness across the PCB surface
– Better suited for high-density PCB designs
– Requires less equipment and setup than LPSM
Disadvantages of DFSM:
– Higher material costs compared to LPSM
– Limited color options (primarily green)
– Reduced adhesion to the PCB surface compared to LPSM
– May require additional surface preparation for optimal adhesion
3. Liquid Screen Printed Solder Mask (LSPSM)
Liquid screen printed solder mask (LSPSM) is applied to the PCB using a traditional screen printing process. A stencil with openings corresponding to the desired solder mask pattern is placed over the PCB, and the liquid solder mask is pushed through the openings using a squeegee. The solder mask is then cured using heat or UV light.
Advantages of LSPSM:
– Lower cost compared to photoimageable solder masks
– Faster application process than LPSM
– Can be used for low-volume production or prototyping
– Available in a variety of colors
Disadvantages of LSPSM:
– Lower resolution and precision compared to photoimageable solder masks
– Increased risk of solder mask bridging between pads
– Requires frequent stencil cleaning and maintenance
– May require touch-ups or rework after application
4. Peelable Solder Mask (PSM)
Peelable solder mask (PSM) is a temporary solder mask that is applied to the PCB to protect specific areas during the soldering process. PSM is typically a latex-based material that is applied by screen printing or manual application. After soldering, the PSM can be easily peeled off, leaving the protected areas clean and free of solder.
Advantages of PSM:
– Protects specific areas of the PCB during soldering
– Easily removed after soldering
– Can be used for rework or repair of PCBs
– Low cost and simple application process
Disadvantages of PSM:
– Not suitable for permanent solder mask applications
– Limited protection against oxidation and contamination
– May leave residue on the PCB surface after removal
– Requires manual application and removal
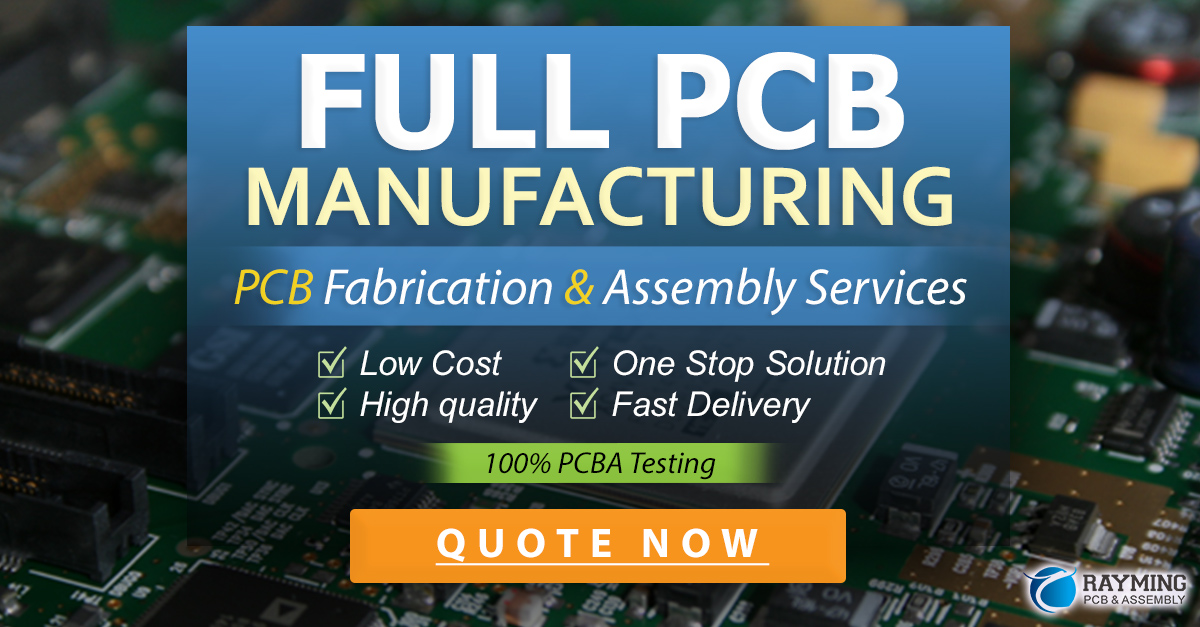
Choosing the Right Solder Mask for Your PCB
When selecting a solder mask for your PCB, consider the following factors:
-
PCB design complexity: For high-density PCB designs with fine pitch components, photoimageable solder masks (LPSM or DFSM) are recommended due to their high resolution and precision.
-
Production volume: LPSM is more cost-effective for high-volume production, while DFSM and LSPSM are better suited for low-volume or prototyping projects.
-
Color requirements: LPSM and LSPSM offer a wider range of color options compared to DFSM, which is primarily available in green.
-
Environmental factors: Consider the operating environment of the PCB and choose a solder mask with appropriate resistance to heat, chemicals, and moisture.
-
Budget and time constraints: LSPSM and PSM are lower-cost options but may require more processing time and manual labor. LPSM and DFSM have higher setup costs but offer faster processing times for large-scale production.
Solder Mask Application Process
The solder mask application process varies depending on the type of solder mask being used but generally follows these steps:
-
Surface preparation: The PCB surface is cleaned and preprocessed to ensure optimal adhesion of the solder mask.
-
Solder mask application: The solder mask is applied to the PCB using the appropriate method (screen printing, curtain coating, lamination, or manual application).
-
Curing or exposure: The solder mask is cured using heat or UV light. For photoimageable solder masks, the mask is exposed to UV light through a photomask to harden the desired areas.
-
Developing: For photoimageable solder masks, the unexposed areas are removed using a developer solution, revealing the copper pads beneath.
-
Final curing: The solder mask undergoes a final curing process to ensure complete polymerization and optimal mechanical and chemical properties.
-
Inspection: The PCB is inspected for any defects or irregularities in the solder mask application, such as bridging, pinholes, or misalignment.
Solder Mask Defects and Troubleshooting
Several common defects can occur during the solder mask application process:
-
Solder mask bridging: This occurs when the solder mask inadvertently covers the copper pads or bridges adjacent pads, preventing proper soldering. Bridging can be caused by incorrect exposure, development, or application of the solder mask.
-
Pinholes: Small holes in the solder mask can expose the underlying copper, leading to oxidation and potential short circuits. Pinholes can be caused by contaminants on the PCB surface, air bubbles in the solder mask, or incorrect curing.
-
Poor adhesion: If the solder mask does not adhere properly to the PCB surface, it can peel or flake off, exposing the copper traces to damage. Poor adhesion can be caused by inadequate surface preparation, incompatible materials, or incorrect curing parameters.
-
Misalignment: Misalignment of the solder mask with the copper pads can lead to exposed copper or solder mask covering the pads, both of which can cause soldering issues. Misalignment can be caused by incorrect registration of the photomask or stencil, or by PCB warpage during the application process.
To troubleshoot and prevent solder mask defects:
- Ensure proper surface preparation and cleaning of the PCB before solder mask application.
- Use compatible materials and follow the manufacturer’s recommended application and curing parameters.
- Implement strict process controls and regular maintenance of application equipment.
- Conduct thorough inspections of the PCB after solder mask application to identify and correct any defects.
FAQ
1. What is the most common color for PCB solder masks?
The most common color for PCB solder masks is green. However, solder masks are available in a variety of colors, including blue, red, yellow, black, and white.
2. Can solder mask be applied to both sides of a PCB?
Yes, solder mask can be applied to both sides of a PCB. This is common for double-sided PCBs that have components and solder connections on both the top and bottom surfaces.
3. How thick is a typical solder mask layer?
A typical solder mask layer is between 0.0005 to 0.002 inches (0.0127 to 0.0508 mm) thick. The exact thickness can vary depending on the type of solder mask and the application method used.
4. Is solder mask required for all PCBs?
While solder mask is highly recommended for most PCBs, it is not always required. Some simple, low-density PCBs or those used in low-risk applications may not necessarily need a solder mask. However, using a solder mask is generally considered good practice for ensuring the reliability and longevity of the PCB.
5. Can solder mask be removed if needed?
Yes, solder mask can be removed if needed, although it is not a simple process. Specialized chemicals or abrasive methods may be used to strip away the solder mask. However, removing the solder mask can potentially damage the underlying copper traces, so it should only be done when absolutely necessary and with great care.
Conclusion
PCB solder mask is a critical component in the manufacturing of reliable and high-quality printed circuit boards. By understanding the different types of solder mask available and their unique properties, PCB designers and manufacturers can select the best option for their specific application. Proper application and process control are essential for achieving a defect-free solder mask that provides optimal protection and functionality for the PCB.
As PCB technology continues to advance, with increasing complexity and miniaturization of components, the role of solder mask in ensuring the reliability and performance of these circuits will only become more important. By staying informed about the latest developments in solder mask materials and application methods, PCB professionals can continue to push the boundaries of what is possible in electronic design and manufacturing.
Leave a Reply