Step 1: Maintain Proper Solder Paste Storage and Handling
Proper storage and handling of solder paste is crucial for preventing solder ball formation. Follow these guidelines to ensure the integrity of your solder paste:
- Store solder paste in a refrigerator at the manufacturer-recommended temperature (typically between 0°C and 10°C).
- Allow the solder paste to reach room temperature before opening the container to prevent condensation.
- Gently stir the solder paste before use to ensure homogeneity and prevent separation of the solder particles and flux.
- Use solder paste within its shelf life and discard any expired or contaminated paste.
Solder Paste Storage Temperature | Shelf Life |
---|---|
0°C to 10°C (Refrigerated) | 6 months |
20°C to 25°C (Room Temperature) | 1 month |
Step 2: Optimize Stencil Design and Thickness
The stencil design and thickness play a significant role in controlling solder paste deposition and minimizing solder ball formation. Consider the following:
- Use a stencil thickness appropriate for the pitch and size of the components being assembled. A typical stencil thickness ranges from 0.100mm to 0.150mm (4 to 6 mils).
- Ensure that the stencil apertures are well-defined and free from any damage or contamination.
- Incorporate additional features such as home plate designs or rounded corners to improve paste release and reduce the risk of Solder Beading.
- Regularly inspect and clean the stencil to maintain its integrity and performance.
Step 3: Control Solder Paste Printing Parameters
Properly controlling the solder paste printing process parameters is essential for achieving consistent paste deposits and minimizing solder ball formation. Key parameters to consider include:
- Print speed: Adjust the print speed based on the solder paste viscosity and stencil design. Typical print speeds range from 25mm/s to 200mm/s.
- Print pressure: Apply sufficient pressure to ensure proper paste transfer without causing excessive squeeze-out or scooping. Typical print pressures range from 0.2kg to 1kg.
- Separation speed: Set the separation speed to allow for a clean and controlled release of the stencil from the PCB. Typical separation speeds range from 0.5mm/s to 10mm/s.
Parameter | Typical Range |
---|---|
Print Speed | 25mm/s – 200mm/s |
Print Pressure | 0.2kg – 1kg |
Separation Speed | 0.5mm/s – 10mm/s |
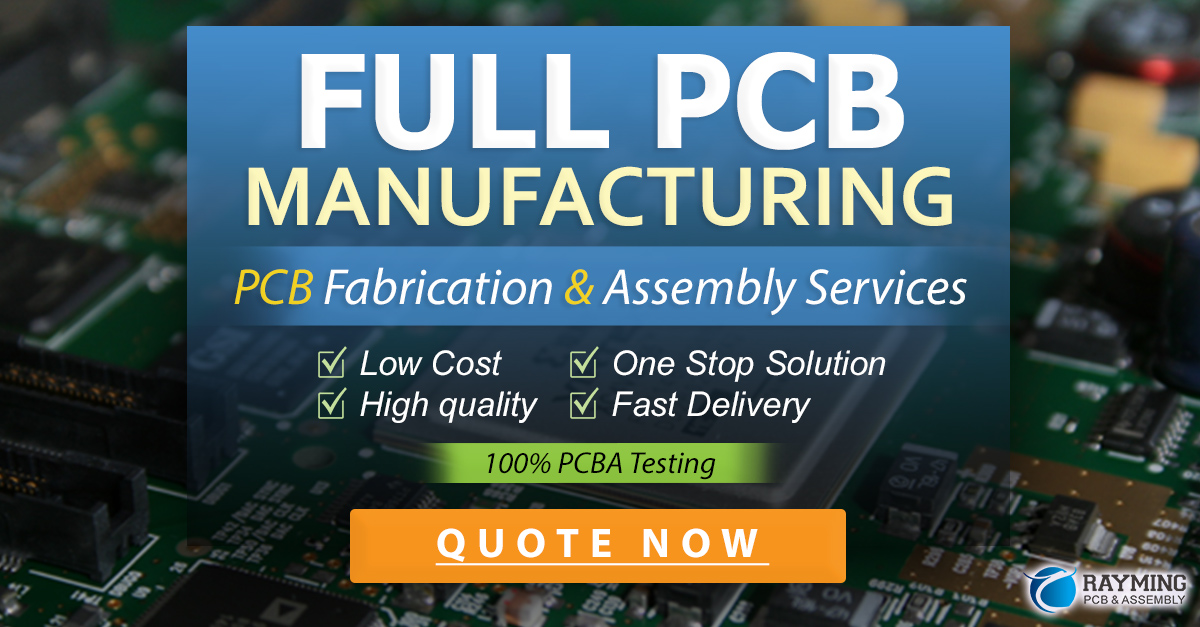
Step 4: Maintain Proper Paste Roll and Aperture Fill
Ensuring proper paste roll and aperture fill during the printing process helps to minimize solder ball formation. Consider the following:
- Use a sufficient volume of solder paste on the stencil to maintain a consistent roll in front of the squeegee.
- Adjust the squeegee angle and pressure to achieve optimal aperture fill without causing excessive paste deposition.
- Regularly replenish the solder paste on the stencil to maintain a consistent print quality throughout the production run.
Step 5: Implement Effective PCB Support and Clamping
Proper PCB support and clamping during the printing process helps to prevent board warpage and ensure consistent paste deposition. Follow these guidelines:
- Use a dedicated PCB support system with adjustable pins or vacuum to maintain flatness and prevent board movement during printing.
- Ensure that the PCB is securely clamped to the support system without causing excessive stress or deformation.
- Regularly inspect and maintain the PCB support system to ensure its accuracy and functionality.
Step 6: Optimize Reflow Oven Temperature Profile
An optimized reflow oven temperature profile is crucial for minimizing solder ball formation and ensuring proper solder joint formation. Consider the following:
- Follow the solder paste manufacturer’s recommended temperature profile, which typically includes preheat, soak, reflow, and cooling zones.
- Ensure that the peak reflow temperature is within the specified range for the solder paste and components being assembled.
- Maintain a consistent and controlled temperature gradient throughout the reflow process to prevent thermal shock and solder balling.
- Regularly calibrate and maintain the reflow oven to ensure its accuracy and performance.
Reflow Zone | Typical Temperature Range |
---|---|
Preheat | 150°C – 180°C |
Soak | 180°C – 200°C |
Reflow | 230°C – 250°C |
Cooling | < 100°C |
Step 7: Control PCB and Component Cleanliness
Maintaining cleanliness of the PCB and components is essential for minimizing solder ball formation. Follow these guidelines:
- Ensure that the PCB and components are free from any dirt, dust, or contaminants before the assembly process.
- Use appropriate cleaning methods such as isopropyl alcohol (IPA) or deionized water to remove any residues or flux from the PCB and components.
- Implement a controlled environment with proper filtration and humidity control to minimize airborne contaminants.
Step 8: Manage Component Placement Accuracy
Accurate component placement is crucial for minimizing solder ball formation and ensuring proper solder joint formation. Consider the following:
- Use a high-precision pick-and-place machine with vision systems to ensure accurate component placement.
- Regularly calibrate and maintain the pick-and-place machine to ensure its accuracy and performance.
- Implement a robust process for managing component feeders and reels to prevent misalignment or damage during the placement process.
Step 9: Implement Effective Nitrogen Reflow Environment
Using a nitrogen reflow environment can help to minimize solder ball formation by reducing oxidation and improving solder joint quality. Follow these guidelines:
- Implement a nitrogen reflow system with a purity level of at least 99.999% (5N).
- Maintain a consistent nitrogen flow rate and pressure throughout the reflow process.
- Ensure proper sealing of the reflow oven to prevent nitrogen leakage and maintain the desired oxygen level (typically below 100 ppm).
Step 10: Conduct Regular Process Monitoring and Quality Control
Regular process monitoring and quality control are essential for identifying and addressing any issues related to solder ball formation. Consider the following:
- Implement a robust statistical process control (SPC) system to monitor key process parameters such as paste volume, print accuracy, and reflow temperatures.
- Conduct regular visual inspections of the assembled PCBs using microscopes or automated optical inspection (AOI) systems to detect any solder ball defects.
- Perform cross-sectional analysis of solder joints to assess the quality and integrity of the solder connections.
- Establish a continuous improvement process to identify and eliminate the root causes of solder ball formation.
Step 11: Provide Proper Training and Education for Operators
Providing proper training and education for operators is crucial for ensuring consistent and high-quality SMT assembly processes. Consider the following:
- Develop comprehensive training programs that cover all aspects of the SMT assembly process, including solder paste handling, stencil printing, component placement, and reflow soldering.
- Provide hands-on training and demonstrations to help operators understand the critical factors that influence solder ball formation and how to prevent them.
- Encourage operators to report any issues or observations related to solder ball formation and involve them in problem-solving and continuous improvement efforts.
- Regularly update and refresh training materials to ensure that operators are knowledgeable about the latest best practices and technologies in SMT assembly.
Frequently Asked Questions (FAQ)
What are solder balls, and why are they a concern in SMT manufacturing?
Solder balls are small, spherical accumulations of solder that form on PCBs or components during the reflow soldering process. They are a concern because they can lead to short circuits, poor electrical connections, and other issues that impact the performance and reliability of electronic assemblies.
What are the main causes of solder ball formation in SMT assembly?
The main causes of solder ball formation include improper solder paste handling and storage, suboptimal stencil design and printing parameters, PCB and component contamination, inaccurate component placement, and inadequate reflow temperature profiles.
How can I optimize my stencil design to minimize solder ball formation?
To optimize your stencil design, consider factors such as stencil thickness, aperture size and shape, and additional features like home plate designs or rounded corners. Ensure that the stencil is well-maintained and free from damage or contamination.
What are the key parameters to control during solder paste printing to prevent solder balls?
The key parameters to control during solder paste printing include print speed, print pressure, and separation speed. Adjust these parameters based on the solder paste characteristics and stencil design to achieve consistent paste deposits and minimize solder beading.
How can implementing a nitrogen reflow environment help to reduce solder ball formation?
Implementing a nitrogen reflow environment helps to reduce solder ball formation by minimizing oxidation and improving solder joint quality. Maintain a high nitrogen purity level (5N) and ensure proper sealing of the reflow oven to achieve the desired oxygen level (below 100 ppm).
By following these 11 easy steps and best practices, you can effectively minimize the occurrence of solder balls in your SMT manufacturing process, improve your production yield, and ensure the long-term reliability of your electronic products. Remember that continuous process monitoring, quality control, and operator training are essential for maintaining a high-quality and efficient SMT assembly operation.
Leave a Reply