1. Temperature Control
Maintaining the correct temperature during the soldering process is essential for achieving high-quality solder joints. Insufficient heat can lead to poor solder flow and weak connections, while excessive heat can cause damage to components and the PCB itself.
Recommended Soldering Temperatures
Component Type | Temperature Range |
---|---|
Through-hole | 300-350°C |
Surface Mount | 230-250°C |
Lead-free | 350-380°C |
To ensure proper temperature control:
– Use a high-quality soldering iron with adjustable temperature settings
– Monitor the temperature regularly using a thermocouple or built-in temperature sensor
– Adjust the temperature according to the type of components and solder being used
2. Solder Selection
Choosing the right type of solder is crucial for creating reliable solder joints. The most common types of solder used in PCB Soldering are lead-based and lead-free solder.
Comparison of Lead-based and Lead-free Solder
Property | Lead-based Solder | Lead-free Solder |
---|---|---|
Melting Point | 183°C | 217-227°C |
Strength | Lower | Higher |
Environmental | Hazardous | Eco-friendly |
Consider the following factors when selecting solder:
– Comply with RoHS (Restriction of Hazardous Substances) regulations
– Match the solder type with the component and PCB requirements
– Use solder with the appropriate diameter for the job
3. Flux Application
Flux is a chemical compound that helps to remove oxides and improve the wetting of the solder to the surfaces being joined. Proper flux application is essential for creating strong and reliable solder joints.
Types of Flux
- Rosin Flux
- Rosin-based fluxes are the most common type used in electronics soldering
- They are available in various activity levels: low, medium, and high
-
Rosin fluxes require cleaning after soldering to remove residue
-
Water-soluble Flux
- Water-soluble fluxes are more active than rosin fluxes and provide better oxide removal
- They require thorough cleaning with water after soldering
-
Improper cleaning can lead to corrosion and other issues
-
No-clean Flux
- No-clean fluxes are designed to leave minimal residue that does not require cleaning
- They are suitable for applications where cleaning is not possible or practical
- However, no-clean fluxes may not be as effective in removing oxides compared to other types
When applying flux:
– Use the appropriate type of flux for the specific application
– Apply flux sparingly, as excessive flux can lead to solder bridging and other defects
– Clean the PCB thoroughly after soldering if using rosin or water-soluble flux
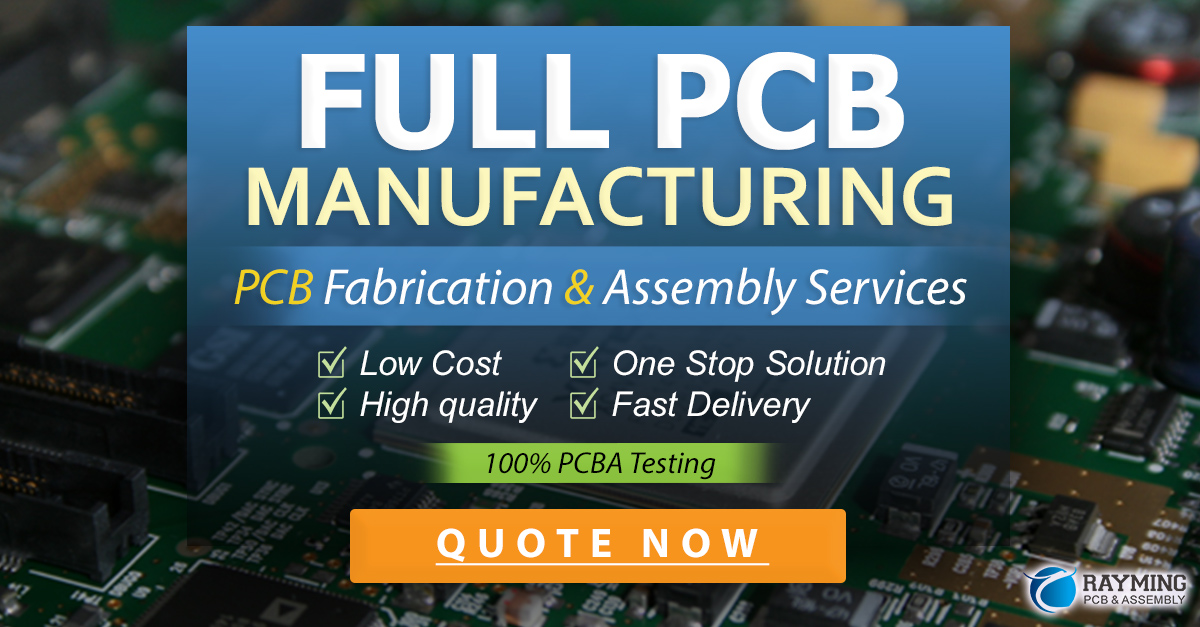
4. Preheating
Preheating the PCB and components before soldering helps to minimize thermal shock and reduce the risk of component damage. It also improves the wetting of the solder and reduces the chances of cold solder joints.
Preheating Methods
- Convection Oven
- Convection ovens provide even heating and are suitable for larger PCBs and batches
-
Preheat the PCB at a temperature of 100-150°C for 1-2 minutes before soldering
-
Hot Plate
- Hot plates are suitable for preheating smaller PCBs and individual components
- Place the PCB or component on the hot plate and preheat at a temperature of 100-150°C for 30-60 seconds
When preheating:
– Ensure the preheat temperature is appropriate for the components and PCB material
– Avoid overheating, as it can cause component damage and PCB warping
– Use a thermometer or thermocouple to monitor the preheat temperature
5. Soldering Technique
Proper soldering technique is essential for creating strong and reliable solder joints. The two main soldering techniques used in PCB soldering are hand soldering and wave soldering.
Hand Soldering
Hand soldering is a manual process that involves using a soldering iron to apply solder to the components and PCB pads. When hand soldering:
– Use a soldering iron with the appropriate tip size and shape for the job
– Apply the soldering iron to the component lead and PCB pad simultaneously
– Feed solder into the joint while keeping the soldering iron in place
– Remove the soldering iron and allow the joint to cool naturally
Wave Soldering
Wave soldering is an automated process that involves passing the PCB over a molten solder wave. When wave soldering:
– Ensure the PCB is properly cleaned and fluxed before soldering
– Adjust the wave height and speed according to the PCB and component requirements
– Monitor the solder temperature and composition regularly
– Inspect the soldered PCB for defects and make necessary adjustments
6. Cleaning
Cleaning the PCB after soldering is essential for removing flux residue, solder splashes, and other contaminants that can affect the performance and reliability of the final product.
Cleaning Methods
- Manual Cleaning
- Use a brush or swab dipped in isopropyl alcohol (IPA) to remove flux residue and solder splashes
- Pay special attention to areas around components and solder joints
-
Allow the PCB to dry completely before further processing
-
Ultrasonic Cleaning
- Place the PCB in an ultrasonic cleaning bath filled with a suitable cleaning solution
- The ultrasonic waves help to dislodge and remove contaminants from the PCB surface
- Rinse the PCB with deionized water and dry thoroughly after cleaning
When cleaning:
– Use the appropriate cleaning method and solution for the type of flux and contaminants present
– Ensure the PCB is completely dry before further processing or packaging
– Follow the manufacturer’s instructions for the cleaning solution and equipment
7. Inspection
Inspecting the soldered PCB is crucial for identifying defects and ensuring the quality of the final product. Visual inspection and automated optical inspection (AOI) are two common methods used for PCB Inspection.
Visual Inspection
Visual inspection involves examining the soldered PCB under a magnifying lens or microscope. When performing visual inspection:
– Check for proper solder joint formation, including shape, size, and wetting
– Look for defects such as solder bridges, cold solder joints, and insufficient solder
– Inspect component placement and alignment
Automated Optical Inspection (AOI)
AOI uses cameras and image processing software to automatically detect defects on the soldered PCB. When using AOI:
– Ensure the AOI system is properly calibrated and programmed for the specific PCB and components
– Set appropriate tolerance levels for defect detection
– Review and verify the AOI results, and make necessary repairs or adjustments
8. Rework and Repair
Despite best efforts, defects may still occur during the PCB soldering process. Rework and repair techniques are used to correct these defects and salvage the PCB.
Rework Techniques
- Desoldering
- Use a desoldering pump or vacuum to remove the defective solder joint
-
Apply fresh solder and flux to the joint and resolder using the proper technique
-
Component Replacement
- Remove the defective component using a desoldering tool or hot air gun
- Clean the PCB pads and replace the component with a new one
- Resolder the component using the proper technique
When performing rework and repair:
– Use the appropriate tools and techniques for the specific type of defect and component
– Take care not to damage the PCB or surrounding components during the rework process
– Inspect the repaired area to ensure proper solder joint formation and component placement
9. Solder Joint Reliability
Solder joint reliability is a critical factor in the overall reliability and longevity of the final product. Several factors can affect solder joint reliability, including thermal cycling, vibration, and mechanical stress.
Factors Affecting Solder Joint Reliability
- Thermal Cycling
- Temperature fluctuations can cause solder joints to expand and contract, leading to fatigue and cracking
-
Use solder alloys with appropriate thermal expansion coefficients and design PCBs with thermal relief pads
-
Vibration
- Vibration can cause solder joints to crack or fail due to mechanical stress
-
Use vibration-dampening mounting techniques and reinforce solder joints with underfill or conformal coating
-
Mechanical Stress
- Physical stress on the PCB, such as bending or twisting, can cause solder joints to fail
- Design PCBs with appropriate stiffness and use strain relief techniques for connectors and cables
To improve solder joint reliability:
– Follow best practices for PCB design, including pad size, shape, and spacing
– Use solder alloys with appropriate mechanical and thermal properties
– Implement stress-reducing techniques, such as underfill and conformal coating, where necessary
10. Training and Certification
Proper training and certification of soldering personnel are essential for ensuring consistent and high-quality PCB soldering. IPC (Association Connecting Electronics Industries) offers several standards and certification programs for PCB soldering.
IPC Soldering Standards and Certifications
- IPC J-STD-001
- Defines the requirements for materials, methods, and verification criteria for producing high-quality soldered interconnections
-
Covers hand soldering, wave soldering, and reflow soldering processes
-
IPC-A-610
- Defines the acceptability criteria for electronic assemblies, including soldered connections
-
Provides visual examples and illustrations of acceptable and defective solder joints
-
IPC Certification Programs
- IPC offers certification programs for soldering personnel, including Certified IPC Specialist (CIS) and Certified IPC Trainer (CIT)
- Certification ensures that personnel have the necessary knowledge and skills to produce high-quality soldered assemblies
To maintain a high level of soldering quality:
– Provide regular training and certification for soldering personnel
– Ensure that personnel are familiar with the relevant IPC standards and acceptability criteria
– Conduct periodic audits and assessments to verify compliance with standards and best practices
Frequently Asked Questions (FAQ)
1. What is the difference between lead-based and lead-free solder?
Lead-based solder contains a combination of tin and lead, while lead-free solder is typically made of tin, silver, and copper. Lead-free solder has a higher melting point and requires higher soldering temperatures compared to lead-based solder. Additionally, lead-free solder is more environmentally friendly and complies with RoHS regulations.
2. How do I select the appropriate solder wire diameter?
The choice of solder wire diameter depends on the size of the components and PCB pads being soldered. Generally, smaller diameter solder wire (0.5-0.7mm) is used for fine-pitch components and smaller pads, while larger diameter solder wire (0.8-1.2mm) is used for larger components and pads. It is essential to select a solder wire diameter that allows for proper solder flow and joint formation without causing bridging or excessive solder buildup.
3. What are the most common PCB Soldering Defects, and how can they be prevented?
Some of the most common PCB soldering defects include:
– Solder bridges: Caused by excessive solder or improper solder application, resulting in unintended connections between pads or pins. Prevention: Use appropriate solder amounts and proper soldering techniques.
– Cold solder joints: Occur when the solder does not melt completely or when there is insufficient heat transfer, resulting in a dull, cracked, or incomplete solder joint. Prevention: Ensure proper preheating and soldering temperatures, and use appropriate soldering techniques.
– Insufficient solder: Happens when not enough solder is applied to the joint, resulting in a weak or unreliable connection. Prevention: Apply the appropriate amount of solder and ensure proper solder flow.
– Tombstoning: Occurs when a surface-mount component stands up on one end due to uneven heating or solder surface tension. Prevention: Ensure even preheating and use appropriate solder paste and stencil design.
Regular inspection, proper training, and adherence to best practices can help prevent these and other soldering defects.
4. How often should I replace my soldering iron tip?
Soldering iron tips should be replaced when they become worn, pitted, or deformed. The frequency of replacement depends on factors such as the type of solder being used, the frequency of use, and the care and maintenance of the tip. In general, tips should be inspected regularly and replaced as needed to ensure optimal soldering performance. Proper tip maintenance, including cleaning and tinning, can help extend the life of the tip.
5. What are the benefits of using nitrogen in the soldering process?
Using nitrogen in the soldering process offers several benefits:
– Reduces oxidation: Nitrogen helps to displace oxygen from the soldering environment, reducing the formation of oxides on the solder and component surfaces. This results in better solder wetting and stronger solder joints.
– Improves solder joint appearance: Soldering in a nitrogen environment produces shinier and smoother solder joints, enhancing the overall appearance of the soldered assembly.
– Increases solder joint reliability: By reducing oxidation and improving solder wetting, nitrogen-assisted soldering helps to create more reliable and durable solder joints.
– Reduces solder defects: Nitrogen soldering can help minimize common soldering defects such as solder balling, bridging, and icicling, improving the overall quality of the soldered assembly.
While nitrogen soldering offers several advantages, it does require additional equipment and setup. The decision to use nitrogen in the soldering process should be based on the specific requirements and constraints of the application.
In conclusion, paying attention to these ten critical issues in PCB soldering can help ensure the production of high-quality, reliable electronic assemblies. By implementing best practices, using appropriate materials and techniques, and providing proper training and certification for personnel, manufacturers can minimize soldering defects, improve product performance, and enhance customer satisfaction.
Leave a Reply