Understanding PCB Tolerance for 0201 and Micro BGA Components
In the world of electronics manufacturing, printed circuit board (PCB) tolerance plays a crucial role in ensuring the reliability and functionality of the final product. As technology advances and components become smaller, such as 0201 and Micro Ball Grid Array (BGA) packages, maintaining tight PCB tolerances becomes increasingly challenging. This article delves into the intricacies of PCB tolerance for 0201 and Micro BGA components, discussing the importance of proper design, manufacturing processes, and quality control measures.
What is PCB Tolerance?
PCB tolerance refers to the acceptable variation in the dimensions and positioning of features on a printed circuit board. These features include the size and location of pads, holes, traces, and other elements that make up the PCB. Maintaining tight tolerances is essential for ensuring proper component placement, solderability, and overall reliability of the assembled board.
The Challenges of 0201 and Micro BGA Components
0201 components, named for their dimensions of 0.02 inches by 0.01 inches (0.5mm x 0.25mm), are among the smallest surface-mount devices (SMDs) used in modern electronics. Their compact size allows for higher component density on PCBs but also presents challenges in terms of placement accuracy and soldering.
Micro BGA packages, on the other hand, feature a grid of solder balls on the underside of the component. These packages offer high I/O density and improved electrical performance compared to traditional SMDs. However, the small pitch (distance between solder balls) and the need for precise alignment during placement make Micro BGAs particularly sensitive to PCB tolerance issues.
Designing for Tight Tolerances
To accommodate 0201 and Micro BGA components, PCB designers must adhere to strict design rules and guidelines. Some key considerations include:
-
Pad Size and Shape: The pads for 0201 components must be carefully designed to ensure proper soldering and prevent tombstoning (when a component stands up on one end due to uneven solder melting). IPC-7351B provides recommended pad dimensions for various component sizes.
-
Solder Mask Clearance: Adequate solder mask clearance around pads is crucial for preventing solder bridging and ensuring proper solder joint formation. The clearance should be large enough to account for any misalignment during the solder mask application process.
-
Routing and Trace Width: When dealing with high-density designs, it is essential to maintain appropriate trace widths and spacing to minimize signal integrity issues and prevent short circuits. The use of controlled impedance traces may be necessary for high-speed signals.
-
Via Size and Placement: Vias, which are used to connect traces on different layers of the PCB, must be carefully sized and placed to avoid interfering with component pads and to ensure reliable electrical connections.
Manufacturing Process Control
Achieving tight PCB tolerances for 0201 and Micro BGA components requires strict control over the manufacturing process. Some critical aspects include:
-
Material Selection: The choice of PCB substrate material can impact dimensional stability and the ability to maintain tight tolerances. High-quality, low-expansion materials such as polyimide or FR-4 with a low coefficient of thermal expansion (CTE) are often preferred for demanding applications.
-
Fabrication Techniques: Advanced fabrication techniques, such as laser drilling and direct imaging, can help improve the accuracy and consistency of PCB features. These methods allow for finer detail and tighter tolerances compared to traditional mechanical drilling and photolithography.
-
Lamination Process: The lamination process, which involves bonding the layers of the PCB together under heat and pressure, must be carefully controlled to minimize distortion and maintain uniform thickness across the board.
-
Plating and Finishing: The quality of the copper plating and the choice of surface finish can affect the solderability and reliability of the PCB. Proper process control is necessary to ensure consistent plating thickness and avoid defects such as voids or nodules.
Quality Control and Inspection
To ensure that PCBs meet the required tolerances for 0201 and Micro BGA components, robust quality control and inspection procedures must be in place. Some common methods include:
-
Automated Optical Inspection (AOI): AOI systems use high-resolution cameras and advanced image processing algorithms to detect defects and measure critical dimensions on the PCB. These systems can quickly identify issues such as pad size variations, trace width deviations, and solder mask misalignment.
-
X-Ray Inspection: X-ray inspection is particularly useful for evaluating the quality of solder joints in BGA packages, as the solder balls are hidden beneath the component. This method can detect voids, bridging, and other defects that may not be visible through optical inspection.
-
Electrical Testing: Electrical testing, such as flying probe or bed-of-nails testing, can verify the continuity and isolation of PCB traces and ensure that the board functions as intended. This testing can help identify any issues related to PCB tolerance, such as short circuits or open connections.
-
Statistical Process Control (SPC): Implementing SPC methods allows manufacturers to monitor the stability and capability of their processes over time. By tracking key metrics such as dimensional variations and defect rates, manufacturers can identify trends and make necessary adjustments to maintain tight tolerances.
The Impact of PCB Tolerance on Assembly and Reliability
PCB tolerance plays a significant role in the assembly process and the overall reliability of the final product. Poor tolerance control can lead to various issues, such as:
-
Component Misalignment: If the pads on the PCB are not precisely located or sized, components may be misaligned during placement. This misalignment can result in poor solder joint formation, reduced electrical performance, and even component failure.
-
Solder Joint Defects: Inconsistent pad sizes, solder mask clearance issues, or surface finish defects can contribute to solder joint problems such as bridging, insufficient solder, or voids. These defects can compromise the mechanical and electrical integrity of the solder joint, leading to reliability issues.
-
Electrical Performance: Trace width and spacing variations can impact the electrical performance of the PCB, particularly for high-speed signals. Inconsistent impedance, crosstalk, and signal reflections can degrade signal quality and cause intermittent or complete system failures.
-
Rework and Scrap: When PCBs fail to meet the required tolerances, they may need to be reworked or scrapped entirely. This rework not only increases production costs but can also introduce additional stress on the components and the board itself, potentially impacting long-term reliability.
Best Practices for Achieving Tight PCB Tolerances
To consistently achieve tight PCB tolerances for 0201 and Micro BGA components, consider the following best practices:
-
Collaborate with Experienced PCB Manufacturers: Work with PCB manufacturers who have experience in producing high-density boards with tight tolerances. These manufacturers should have a proven track record of delivering quality products and be willing to invest in advanced equipment and processes.
-
Communicate Design Intent: Clearly communicate your design intent and requirements to the PCB manufacturer. Provide detailed documentation, including CAD files, fabrication drawings, and assembly instructions, to ensure that all stakeholders understand the critical tolerances and specifications.
-
Perform Design for Manufacturability (DFM) Analysis: Before finalizing your PCB design, conduct a thorough DFM analysis to identify any potential issues related to tolerances, component placement, or routing. This analysis can help you optimize your design for manufacturing and minimize the risk of defects or assembly problems.
-
Implement Robust Quality Control: Establish a comprehensive quality control plan that includes incoming material inspection, in-process monitoring, and final product testing. Work with your PCB manufacturer to define acceptable quality levels (AQLs) and develop a system for tracking and resolving any tolerance-related issues.
-
Monitor and Continuously Improve: Regularly monitor the performance of your PCBs and gather feedback from customers or end-users. Use this information to identify areas for improvement and work with your PCB manufacturer to implement process enhancements or design changes that can further optimize tolerance control.
Frequently Asked Questions (FAQ)
-
What is the minimum pad size for 0201 components?
The recommended minimum pad size for 0201 components, according to IPC-7351B, is 0.2mm x 0.4mm (0.008″ x 0.016″). However, the exact dimensions may vary depending on the specific component and the PCB manufacturer’s capabilities. -
How does solder mask clearance affect PCB tolerance?
Solder mask clearance refers to the distance between the edge of a pad and the opening in the solder mask layer. Insufficient clearance can lead to solder bridging, while excessive clearance can result in exposed copper and potential corrosion. Maintaining the proper solder mask clearance is crucial for achieving reliable solder joints and maintaining tight PCB tolerances. -
What is the typical pitch for Micro BGA packages?
The pitch, or distance between solder balls, for Micro BGA packages can vary depending on the specific package size and design. Common pitches for Micro BGAs range from 0.3mm to 0.8mm, with some packages having pitches as small as 0.25mm. -
How can X-ray inspection help with PCB tolerance control?
X-ray inspection is a valuable tool for evaluating the quality of solder joints in BGA packages, as the solder balls are hidden beneath the component. This method can detect voids, bridging, and other defects that may not be visible through optical inspection. By identifying these issues, manufacturers can make necessary adjustments to their processes to maintain tight PCB tolerances. -
What is the role of statistical process control (SPC) in maintaining PCB tolerances?
Statistical process control (SPC) involves monitoring key metrics, such as dimensional variations and defect rates, to assess the stability and capability of the PCB manufacturing process. By tracking these metrics over time, manufacturers can identify trends and make data-driven decisions to maintain tight tolerances. SPC helps to detect process shifts early, allowing for timely corrective actions and continuous improvement.
Conclusion
Maintaining tight PCB tolerances for 0201 and Micro BGA components is a complex challenge that requires careful design, advanced manufacturing processes, and rigorous quality control. By understanding the unique requirements of these components and implementing best practices throughout the PCB lifecycle, manufacturers can consistently produce high-quality boards that meet the demands of today’s miniaturized electronics.
As technology continues to evolve and component sizes shrink further, the importance of PCB tolerance control will only increase. By staying at the forefront of design and manufacturing techniques, collaborating with experienced partners, and fostering a culture of continuous improvement, the electronics industry can overcome the challenges posed by ever-tightening tolerances and deliver innovative, reliable products to consumers worldwide.
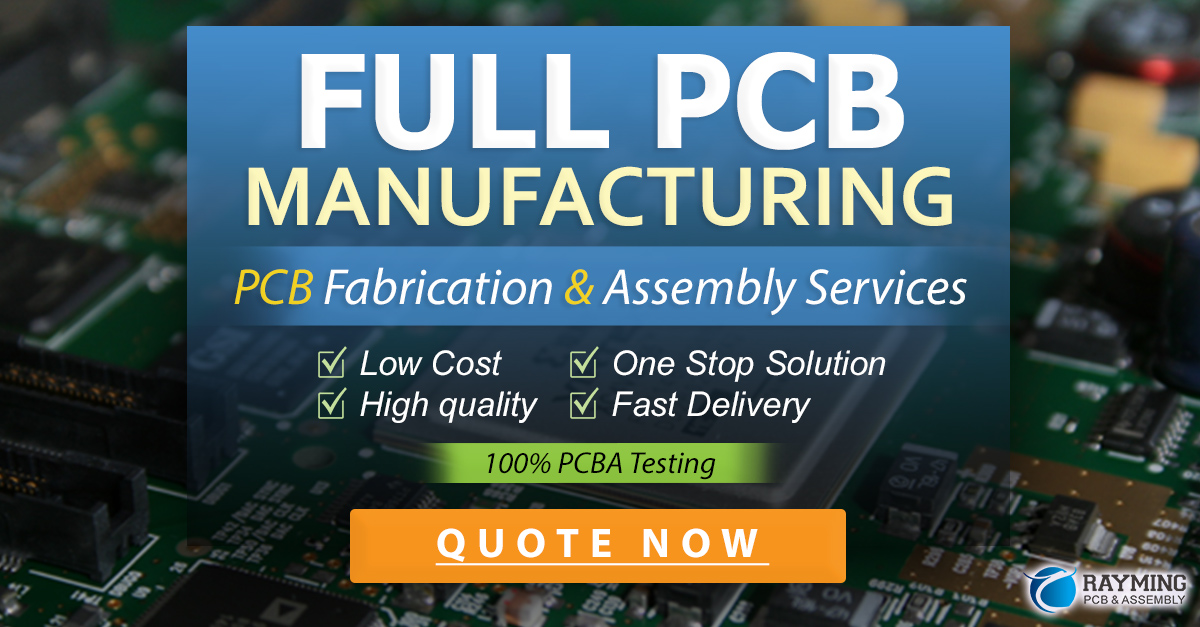
Leave a Reply