Introduction to PCB Design and Common Mistakes
Printed Circuit Board (PCB) design is a crucial aspect of electronic product development. A well-designed PCB ensures that the electronic components function correctly, reliably, and efficiently. However, designing a PCB is not always a straightforward process, and even experienced designers can make mistakes that can lead to costly delays, malfunctions, or even complete failure of the end product.
In this article, we will discuss the five most common mistakes in PCB design and how to avoid them. By understanding these mistakes and following best practices, you can create high-quality PCBs that meet your project requirements and exceed customer expectations.
Mistake 1: Inadequate Planning and Design Specification
One of the most critical steps in PCB design is planning and creating a comprehensive design specification. Failing to plan adequately can lead to numerous issues down the line, such as incorrect component selection, incompatible footprints, and layout problems.
Importance of Planning and Design Specification
A thorough design specification should include:
- Project goals and requirements
- Component selection and specifications
- Schematic design
- Layout constraints
- Manufacturing and assembly considerations
By having a clear and detailed design specification, you can ensure that all stakeholders are on the same page and that the PCB design meets the project’s requirements.
How to Avoid Inadequate Planning and Design Specification
- Involve all stakeholders in the planning process
- Create a detailed design specification document
- Review and update the design specification regularly
- Use a version control system to track changes
Mistake 2: Improper Component Selection and Placement
Selecting the wrong components or placing them incorrectly on the PCB can lead to various issues, such as signal integrity problems, thermal management issues, and mechanical interference.
Importance of Component Selection and Placement
Proper component selection and placement are essential for:
- Ensuring correct functionality
- Optimizing signal integrity
- Minimizing electromagnetic interference (EMI)
- Facilitating manufacturing and assembly
How to Avoid Improper Component Selection and Placement
- Choose components that meet the design requirements
- Use computer-aided design (CAD) tools to optimize component placement
- Follow best practices for component placement, such as grouping related components and minimizing trace lengths
- Consider manufacturing and assembly constraints when placing components
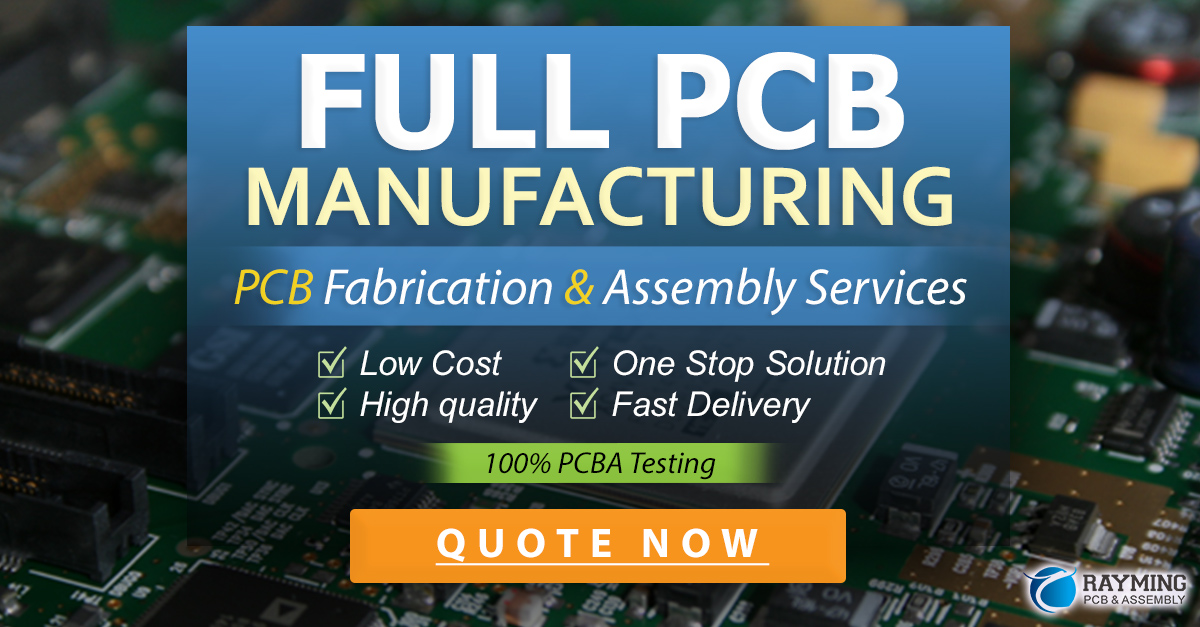
Mistake 3: Neglecting Signal Integrity and EMI
Signal integrity and EMI are critical aspects of PCB design that can significantly impact the performance and reliability of the end product. Neglecting these factors can lead to issues such as crosstalk, reflections, and radiated emissions.
Importance of Signal Integrity and EMI
Proper signal integrity and EMI management are essential for:
- Ensuring reliable data transmission
- Minimizing crosstalk and reflections
- Complying with electromagnetic compatibility (EMC) regulations
- Preventing interference with other electronic devices
How to Avoid Neglecting Signal Integrity and EMI
- Use controlled impedance traces for high-speed signals
- Implement proper grounding and shielding techniques
- Follow best practices for routing, such as avoiding sharp bends and minimizing trace lengths
- Perform signal integrity simulations and EMI testing to validate the design
Mistake 4: Ignoring Thermal Management
Thermal management is crucial for ensuring the long-term reliability and performance of electronic components. Ignoring thermal management can lead to overheating, reduced component lifespan, and even complete failure of the PCB.
Importance of Thermal Management
Proper thermal management is essential for:
- Preventing component overheating
- Ensuring long-term reliability
- Maintaining optimal performance
- Avoiding premature component failure
How to Avoid Ignoring Thermal Management
- Select components with appropriate power ratings and thermal characteristics
- Use thermal simulation tools to analyze heat distribution on the PCB
- Implement proper heat dissipation techniques, such as using heatsinks and thermal vias
- Consider the operating environment and design for worst-case scenarios
Mistake 5: Overlooking Manufacturing and Assembly Considerations
PCB design does not end with the layout and routing. It is essential to consider manufacturing and assembly aspects to ensure that the PCB can be produced efficiently and cost-effectively.
Importance of Manufacturing and Assembly Considerations
Considering manufacturing and assembly aspects is essential for:
- Ensuring design for manufacturability (DFM)
- Minimizing production costs
- Facilitating efficient assembly processes
- Avoiding production delays and quality issues
How to Avoid Overlooking Manufacturing and Assembly Considerations
- Follow the manufacturer’s design guidelines and constraints
- Use standard component packages and footprints
- Implement proper design for assembly (DFA) techniques, such as providing adequate clearances and using fiducial markers
- Communicate with the manufacturer and assembly provider throughout the design process
Frequently Asked Questions (FAQ)
1. What are the most common mistakes in PCB design?
The five most common mistakes in PCB design are:
- Inadequate planning and design specification
- Improper component selection and placement
- Neglecting signal integrity and EMI
- Ignoring thermal management
- Overlooking manufacturing and assembly considerations
2. How can I ensure proper signal integrity in my PCB design?
To ensure proper signal integrity in your PCB design, you should:
- Use controlled impedance traces for high-speed signals
- Follow best practices for routing, such as avoiding sharp bends and minimizing trace lengths
- Implement proper grounding and shielding techniques
- Perform signal integrity simulations to validate the design
3. What is thermal management in PCB design, and why is it important?
Thermal management in PCB design refers to the techniques used to dissipate heat generated by electronic components. It is essential for preventing component overheating, ensuring long-term reliability, maintaining optimal performance, and avoiding premature component failure.
4. How can I avoid manufacturing and assembly issues in my PCB design?
To avoid manufacturing and assembly issues in your PCB design, you should:
- Follow the manufacturer’s design guidelines and constraints
- Use standard component packages and footprints
- Implement proper design for assembly (DFA) techniques, such as providing adequate clearances and using fiducial markers
- Communicate with the manufacturer and assembly provider throughout the design process
5. What are the benefits of creating a comprehensive design specification for my PCB project?
Creating a comprehensive design specification for your PCB project offers several benefits, such as:
- Ensuring that all stakeholders are on the same page
- Providing a clear roadmap for the design process
- Facilitating better communication among team members
- Helping to identify potential issues early in the design process
- Ensuring that the final PCB design meets the project’s requirements
Conclusion
PCB design is a complex process that requires careful planning, attention to detail, and adherence to best practices. By understanding and avoiding the five most common mistakes in PCB design, you can create high-quality PCBs that meet your project requirements and exceed customer expectations.
Remember to create a comprehensive design specification, select components carefully, consider signal integrity and EMI, manage thermal issues, and account for manufacturing and assembly aspects. By following these guidelines and continuously learning from your experiences, you can become a proficient PCB designer and contribute to the success of your electronic projects.
Mistake | Importance | How to Avoid |
---|---|---|
Inadequate Planning and Design Specification | Ensures all stakeholders are on the same page and the PCB design meets project requirements | Involve stakeholders, create a detailed specification, review regularly, and use version control |
Improper Component Selection and Placement | Ensures correct functionality, optimizes signal integrity, minimizes EMI, and facilitates manufacturing and assembly | Choose components that meet requirements, use CAD tools, follow best practices, and consider manufacturing constraints |
Neglecting Signal Integrity and EMI | Ensures reliable data transmission, minimizes crosstalk and reflections, complies with EMC regulations, and prevents interference | Use controlled impedance traces, implement proper grounding and shielding, follow routing best practices, and perform simulations and testing |
Ignoring Thermal Management | Prevents component overheating, ensures long-term reliability, maintains optimal performance, and avoids premature failure | Select appropriate components, use thermal simulation tools, implement heat dissipation techniques, and design for worst-case scenarios |
Overlooking Manufacturing and Assembly Considerations | Ensures design for manufacturability, minimizes production costs, facilitates efficient assembly, and avoids delays and quality issues | Follow manufacturer’s guidelines, use standard components and footprints, implement DFA techniques, and communicate with the manufacturer and assembler |
Leave a Reply